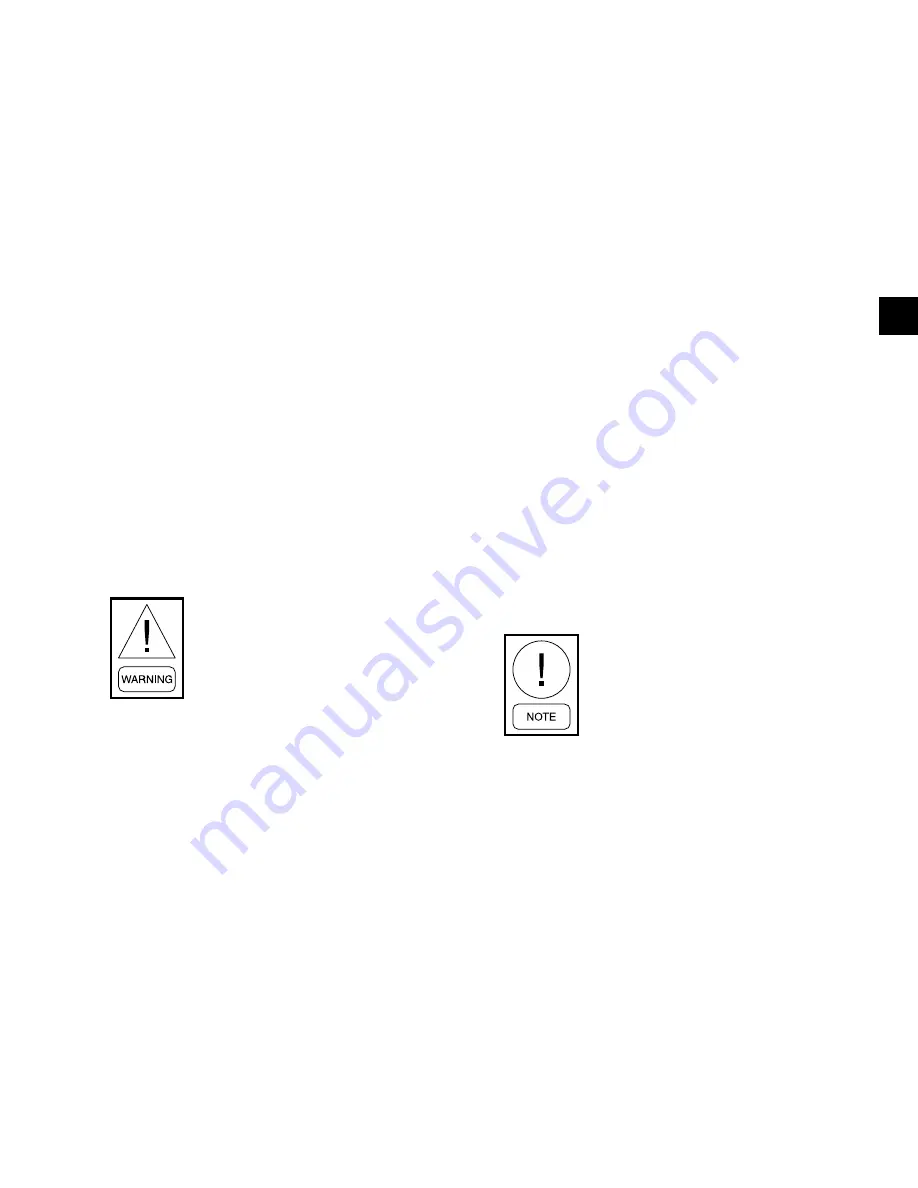
JOHNSON CONTROLS
121
SECTION 5 - MAINTENANCE
FORM 161.01-OM1
ISSUE DATE: 6/8/2018
5
4. Test around each joint and factory weld carefully
and thoroughly.
5. To check for tube or tube joint leaks:
a. Isolate and drain the condenser and evapora-
tor waterboxes
b. Purge the waterboxes and tubes with dry ni-
trogen through the vents or drains until the
detector does not indicate
c. Close the vents and drains and wait an hour
d. Open a vent or drain and insert the leak de-
tector. If a leak is detected, the heads must
be removed and the source of the leak de-
termined as outlined in the
6. Recover the test gas as applicable, make neces-
sary repairs, repeat leak tests, evacuate the chiller
and perform time hold test. Always consider the
effect of temperature change when performing
any time-based hold test. For an ideal gas, at time
1, pressure over temperature (absolute unit sys-
tem) = the ratio at time 2.
SYSTEM EVACUATION
Ensure power is removed from the input
side of the VSD at all times when the
chiller is under vacuum (less than atmo-
spheric pressure). The VSD maintains
voltage to ground on the motor when the
chiller is off while voltage is available to
the VSD. Insulating properties in the mo-
tor are reduced in vacuum and may not
insulate this voltage sufficiently.
After the pressure test has been completed, the vacuum
test should be conducted as follows:
1. Connect a high capacity vacuum pump, with in-
dicator, to the system charging valve as shown in
See
Vacuum Dehydration on page 121
2. Open wide all system valves. Be sure all valves to
the atmosphere are closed and flare caps installed
on outlets.
3. Operate the vacuum pump in accordance with
Vacuum Dehydration on page 121
in this section
until a wet bulb temperature of +32°F (0°C) or a
pressure of 5 mm Hg is reached.
See
for corresponding pressure values.
4. To improve evacuation circulate hot water, not
to exceed 120 °F (49 ºC) through the evaporator
and condenser tubes to thoroughly dehydrate the
shells. If a source of hot water is not readily avail-
able, a portable water heater should be employed.
DO NOT USE STEAM. A suggested method is
to connect a hose between the source of hot water
under pressure and the evaporator head drain con-
nection, out the evaporator vent connection, into
the condenser head drain and out the condenser
vent. To avoid the possibility of causing leaks, the
temperature should be brought up slowly so that
the tubes and shell are heated evenly.
5. Close the system charging valve and the stop
valve between the vacuum indicator and the vac-
uum pump. Then disconnect the vacuum pump
leaving the vacuum indicator in place.
6. Hold the vacuum obtained in
Step 3
above in the
system for 8 hours; the slightest rise in pressure
indicates a leak or the presence of moisture, or
both. It is important to check for pressure change
with the chiller at the same temperature. Pressure
will change proportional to temperature and affect
results. If after 24 hours the wet bulb temperature
in the vacuum indicator has not risen above 40°F
(4.4°C) or a pressure of 6.3 mm Hg, the system
may be considered tight.
Be sure the vacuum indicator is valved off
while holding the system vacuum and be
sure to open the valve between the vacuum
indicator and the system when checking
the vacuum after the 8 hour period.
7. If the vacuum does not hold for 8 hours within the
limits specified in
Step 6
above, the leak must be
found and repaired.
VACUUM DEHYDRATION
To obtain a sufficiently dry system, the following in-
structions have been assembled to provide an effective
method for evacuating and dehydrating a system in the
field. Although there are several methods of dehydrating
a system, we are recommending the following, as it pro-
duces one of the best results, and affords a means of ob-
taining accurate readings as to the extent of dehydration.
The equipment required to follow this method of dehy-
dration consists of a wet bulb indicator or vacuum gauge,
a chart showing the relation between dew point tempera-
ture and pressure in inches of mercury (vacuum), (
See
) and a vacuum pump capable of
pumping a suitable vacuum on the system.
Содержание YZ MODEL A
Страница 10: ...JOHNSON CONTROLS 10 FORM 161 01 OM1 ISSUE DATE 6 8 2018 THIS PAGE INTENTIONALLY LEFT BLANK...
Страница 118: ...JOHNSON CONTROLS 118 FORM 161 01 OM1 ISSUE DATE 6 8 2018 SECTION 4 VSD OPERATION THIS PAGE INTENTIONALLY LEFT BLANK...
Страница 138: ...JOHNSON CONTROLS 138 FORM 161 01 OM1 ISSUE DATE 6 8 2018 SECTION 6 PRINTING THIS PAGE INTENTIONALLY LEFT BLANK...
Страница 142: ...JOHNSON CONTROLS 142 FORM 161 01 OM1 ISSUE DATE 6 8 2018 Appendix Material Safety Data Sheets...
Страница 143: ...JOHNSON CONTROLS 143 Appendix Material Safety Data Sheets FORM 161 01 OM1 ISSUE DATE 6 8 2018...
Страница 144: ...JOHNSON CONTROLS 144 FORM 161 01 OM1 ISSUE DATE 6 8 2018 Appendix Material Safety Data Sheets...
Страница 145: ...JOHNSON CONTROLS 145 Appendix Material Safety Data Sheets FORM 161 01 OM1 ISSUE DATE 6 8 2018...
Страница 146: ...JOHNSON CONTROLS 146 FORM 161 01 OM1 ISSUE DATE 6 8 2018 Appendix Material Safety Data Sheets...
Страница 147: ...JOHNSON CONTROLS 147 Appendix Material Safety Data Sheets FORM 161 01 OM1 ISSUE DATE 6 8 2018...
Страница 148: ...JOHNSON CONTROLS 148 FORM 161 01 OM1 ISSUE DATE 6 8 2018 Appendix Material Safety Data Sheets...
Страница 149: ...JOHNSON CONTROLS 149 Appendix Material Safety Data Sheets FORM 161 01 OM1 ISSUE DATE 6 8 2018...
Страница 150: ...JOHNSON CONTROLS 150 FORM 161 01 OM1 ISSUE DATE 6 8 2018 Appendix Material Safety Data Sheets...
Страница 151: ...JOHNSON CONTROLS 151 Appendix Material Safety Data Sheets FORM 161 01 OM1 ISSUE DATE 6 8 2018...
Страница 152: ...JOHNSON CONTROLS 152 FORM 161 01 OM1 ISSUE DATE 6 8 2018 Appendix Material Safety Data Sheets...
Страница 153: ...JOHNSON CONTROLS 153 Appendix Material Safety Data Sheets FORM 161 01 OM1 ISSUE DATE 6 8 2018...
Страница 154: ...JOHNSON CONTROLS 154 FORM 161 01 OM1 ISSUE DATE 6 8 2018 Appendix Material Safety Data Sheets...