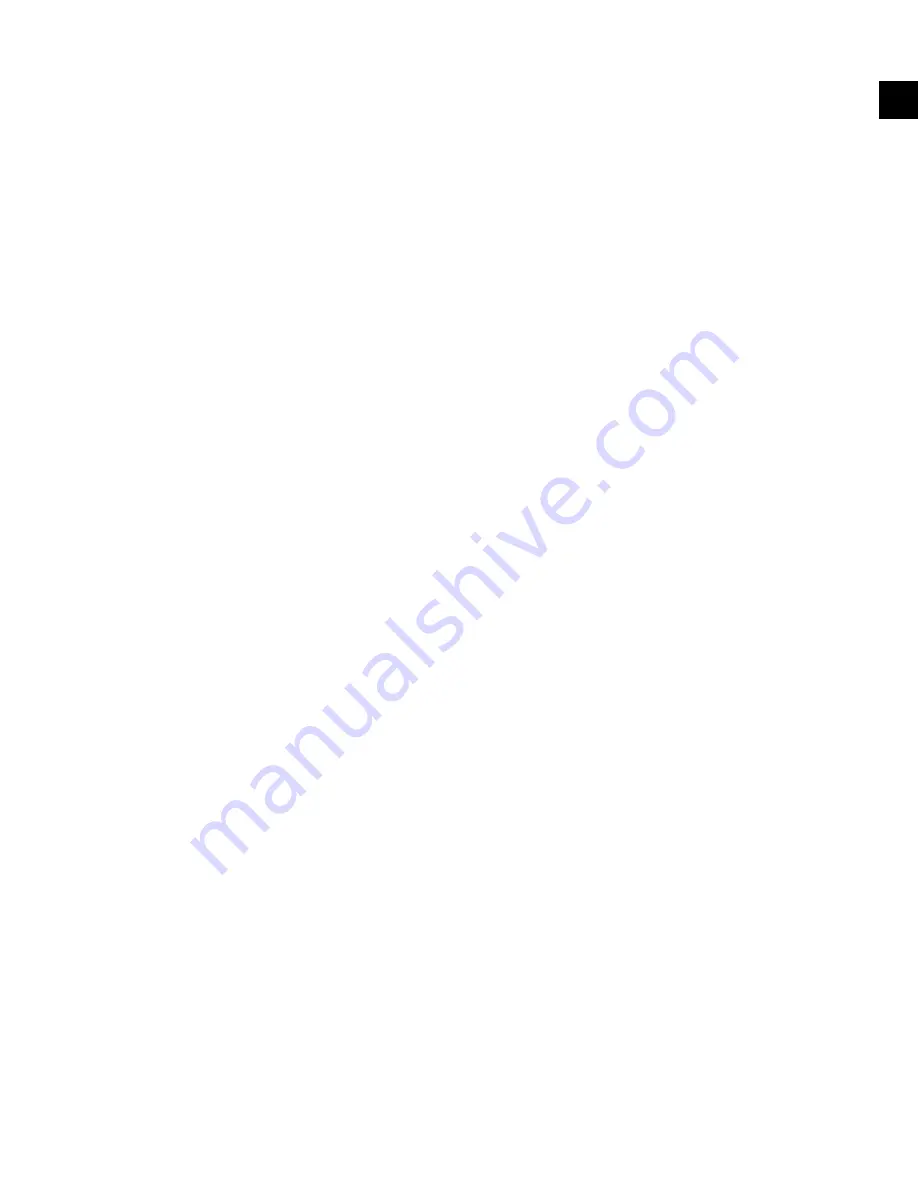
JOHNSON CONTROLS
11
FORM 161.01-OM1
ISSUE DATE: 6/8/2018
1
SECTION 1 - SYSTEM FUNDAMENTALS
SYSTEM COMPONENTS
The YORK Model YZ Centrifugal Chiller is complete-
ly factory-packaged. The package includes the evapo-
rator, condenser, compressor, motor, variable speed
drive (VSD), OptiView
TM
Control Center and all inter-
connecting unit piping and wiring (
see Figure 1 and
).
Compressor
The compressor is a single-stage centrifugal type. It is
powered by a high speed hermetic induction motor, on
a common shaft with a cast aluminum, fully shrouded,
impeller. The compressor assembly includes a variable
geometry diffuser.
Motor
The compressor motor is a high speed hermetic induc-
tion motor design with magnetic bearings. The com-
pressor impeller is overhung from the end of the motor
shaft and has no bearings of its own.
The motor includes angular contact ball bearings. The
bearings engage with the rotor shaft during shutdown
and after the rotation is stopped.
Heat Exchangers
The evaporator and condenser shells are fabricated
from rolled carbon steel plates with fusion welded
seams. Heat exchanger tubes are internally and exter-
nally enhanced type.
Evaporator
The evaporator is a shell and tube, hybrid falling film
and flooded type heat exchanger. A spray header pro-
vides uniform distribution of refrigerant over tubes in
the falling film section. Residual refrigerant floods the
tubes in the lower section. Mesh eliminators are locat-
ed above the tube bundle to prevent liquid refrigerant
carryover into the compressor.
A 2 inch liquid level sight glass is located on the side
of the shell. The evaporator shell may contain single or
dual refrigerant relief valves, unless the optional con-
denser isolation valve is installed.
Condenser
The condenser is a shell and tube type heat exchanger.
It has a discharge gas baffle to prevent direct high ve-
locity impingement on the tubes. A separate subcooler
is located in the condenser to enhance performance.
Single or dual refrigerant relief valves are located on
the condenser shell, unless the optional refrigerant iso-
lation valves are installed.
Water Boxes
The removable compact water boxes are made of steel.
The design working pressure is 150 PSIG (1034 kPa).
The boxes are tested at 225 PSIG (1551 kPa). Integral
steel water baffles provide the required pass arrange-
ments. Stub-out water nozzle connections with Victau-
lic grooves are welded to the water boxes. These nozzle
connections are suitable for Victaulic couplings, weld-
ing or flanges. They are capped for shipment. Plugged
3/4 inch drain and vent connections are provided on
each water box. Optional marine water boxes and high-
er working pressure ratings are available.
Refrigerant Flow Control
Refrigerant flow to the evaporator is controlled by the
liquid level control valve. While the chiller is running,
the refrigerant level is normally controlled to the level
setpoint.
A level sensor senses the refrigerant level in the con-
denser. The sensor outputs an analog voltage to the
control panel to indicate the level, with 0% indicating
empty and 100% indicating full.
Under program control, the control panel modulates
the liquid level control valve to maintain the condens-
er refrigerant level at a programmed setpoint. Other
setpoints affect the control sensitivity and response.
Only a qualified service technician may modify these
settings. The level setpoint must be entered at chiller
commissioning by a qualified service technician.
While the chiller is shut down, the level control valve
is pre-positioned to anticipate run. When the chiller
starts, if the actual level is less than the level setpoint, a
linearly increasing ramp is applied to the level setpoint.
This ramp causes the setpoint to go from the initial re-
frigerant level to the programmed setpoint over a spe-
cific period of time. If the actual level is greater than
the setpoint upon run, it immediately begins to control
to the programmed setpoint.
1
Содержание YZ MODEL A
Страница 10: ...JOHNSON CONTROLS 10 FORM 161 01 OM1 ISSUE DATE 6 8 2018 THIS PAGE INTENTIONALLY LEFT BLANK...
Страница 118: ...JOHNSON CONTROLS 118 FORM 161 01 OM1 ISSUE DATE 6 8 2018 SECTION 4 VSD OPERATION THIS PAGE INTENTIONALLY LEFT BLANK...
Страница 138: ...JOHNSON CONTROLS 138 FORM 161 01 OM1 ISSUE DATE 6 8 2018 SECTION 6 PRINTING THIS PAGE INTENTIONALLY LEFT BLANK...
Страница 142: ...JOHNSON CONTROLS 142 FORM 161 01 OM1 ISSUE DATE 6 8 2018 Appendix Material Safety Data Sheets...
Страница 143: ...JOHNSON CONTROLS 143 Appendix Material Safety Data Sheets FORM 161 01 OM1 ISSUE DATE 6 8 2018...
Страница 144: ...JOHNSON CONTROLS 144 FORM 161 01 OM1 ISSUE DATE 6 8 2018 Appendix Material Safety Data Sheets...
Страница 145: ...JOHNSON CONTROLS 145 Appendix Material Safety Data Sheets FORM 161 01 OM1 ISSUE DATE 6 8 2018...
Страница 146: ...JOHNSON CONTROLS 146 FORM 161 01 OM1 ISSUE DATE 6 8 2018 Appendix Material Safety Data Sheets...
Страница 147: ...JOHNSON CONTROLS 147 Appendix Material Safety Data Sheets FORM 161 01 OM1 ISSUE DATE 6 8 2018...
Страница 148: ...JOHNSON CONTROLS 148 FORM 161 01 OM1 ISSUE DATE 6 8 2018 Appendix Material Safety Data Sheets...
Страница 149: ...JOHNSON CONTROLS 149 Appendix Material Safety Data Sheets FORM 161 01 OM1 ISSUE DATE 6 8 2018...
Страница 150: ...JOHNSON CONTROLS 150 FORM 161 01 OM1 ISSUE DATE 6 8 2018 Appendix Material Safety Data Sheets...
Страница 151: ...JOHNSON CONTROLS 151 Appendix Material Safety Data Sheets FORM 161 01 OM1 ISSUE DATE 6 8 2018...
Страница 152: ...JOHNSON CONTROLS 152 FORM 161 01 OM1 ISSUE DATE 6 8 2018 Appendix Material Safety Data Sheets...
Страница 153: ...JOHNSON CONTROLS 153 Appendix Material Safety Data Sheets FORM 161 01 OM1 ISSUE DATE 6 8 2018...
Страница 154: ...JOHNSON CONTROLS 154 FORM 161 01 OM1 ISSUE DATE 6 8 2018 Appendix Material Safety Data Sheets...