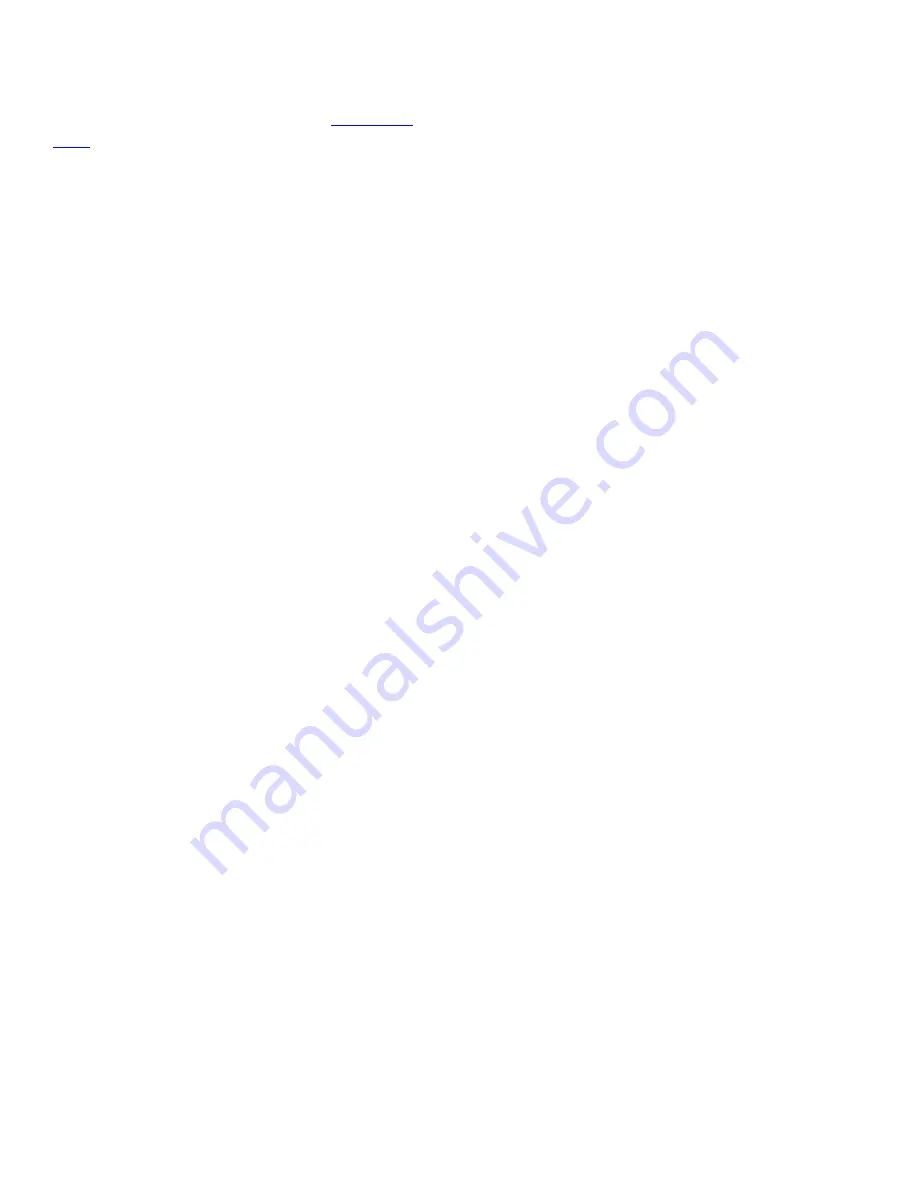
JOHNSON CONTROLS
120
FORM 161.01-OM1
ISSUE DATE: 6/8/2018
SECTION 5 - MAINTENANCE
RENEWAL PARTS
For any required Renewal Parts, refer to
.
OPERATING INSPECTIONS
By following a regular inspection using the display
readings of the OptiView Control Center, and mainte-
nance procedure, the operator will avoid serious oper-
ating difficulty. The following list of inspections and
procedures should be used as a guide.
Daily
1. Check OptiView Control Center displays.
2. Check entering and leaving condenser water tem-
peratures for comparison with job design con-
ditions. Condenser water temperatures can be
checked on the SYSTEM Screen.
3. Check the entering and leaving chilled liquid tem-
peratures and evaporator pressure for comparison
with job design conditions. Chilled liquid tem-
peratures can be checked on the SYSTEM Screen.
4. Check the condenser saturation temperature
(based upon condenser pressure sensed by the
condenser transducer) on the SYSTEM Screen.
5. Check the compressor discharge temperature on
the SYSTEM Screen. During normal operation
discharge temperature should not exceed 220°F
(104°C).
6. Check the compressor motor current on the SYS-
TEM Screen.
7. Check for any signs of dirty or fouled condenser
tubes. (The temperature difference between wa-
ter leaving condenser and saturated condensing
temperature should not exceed the difference re-
corded for a new unit by more than 4°F (2.2°C)).
Weekly
Check the refrigerant charge.
See
.
Semi-Annually (Or More Often As Required)
Check controls.
Annually (More Often If Necessary)
1. Evaporator and Condenser
a. Inspect and clean water strainers
b. Inspect and clean tubes as required
c. Inspect end sheet.
2. Compressor Drive Motor
a. Measure motor winding insulation resistance
3. Inspect and service electrical components as nec-
essary
4. Perform refrigerant analysis
CHECKING SYSTEM FOR LEAKS
Leak Testing During Operation
The refrigerant side of the system is carefully pressure
tested and evacuated at the factory.
After the system has been charged, the system should
be carefully leak tested with a refrigerant compatible
leak detector to be sure all joints are tight.
If any leaks are indicated, they must be repaired im-
mediately. At times, leaks can be stopped by ensuring
face seal nuts and flange bolts are properly torqued.
However, for any major repair, the refrigerant charge
must be removed.
See
mantling And Repairs on page 125
in this section.
CONDUCT PRESSURE TEST
With the refrigerant charge removed and all known
leaks repaired, charge the system with dry nitrogen to
30 psig to (206 kPa) detect any leaks using a liquid
soap solution test. The test can be enhanced with the
use of an ultrasonic leak detector.
Optional Trace Gas Pressure Test
1. With no pressure in the system and refrigerant re-
moved, charge a trace gas (helium may be used)
and dry nitrogen mixture into the chiller until
pressure is at least 30 psig (206 kPa).
2. One method is to charge 5 to 10 lbm of the en-
vironmentally-appropriate trace gas and then add
dry nitrogen into the system to a pressure of 30
psig (206 kPa).
3. To make sure that the concentration of tracer
reached all parts of the system, slightly open the
service valve and test for the presence of gas with
a leak detector.
Содержание YZ MODEL A
Страница 10: ...JOHNSON CONTROLS 10 FORM 161 01 OM1 ISSUE DATE 6 8 2018 THIS PAGE INTENTIONALLY LEFT BLANK...
Страница 118: ...JOHNSON CONTROLS 118 FORM 161 01 OM1 ISSUE DATE 6 8 2018 SECTION 4 VSD OPERATION THIS PAGE INTENTIONALLY LEFT BLANK...
Страница 138: ...JOHNSON CONTROLS 138 FORM 161 01 OM1 ISSUE DATE 6 8 2018 SECTION 6 PRINTING THIS PAGE INTENTIONALLY LEFT BLANK...
Страница 142: ...JOHNSON CONTROLS 142 FORM 161 01 OM1 ISSUE DATE 6 8 2018 Appendix Material Safety Data Sheets...
Страница 143: ...JOHNSON CONTROLS 143 Appendix Material Safety Data Sheets FORM 161 01 OM1 ISSUE DATE 6 8 2018...
Страница 144: ...JOHNSON CONTROLS 144 FORM 161 01 OM1 ISSUE DATE 6 8 2018 Appendix Material Safety Data Sheets...
Страница 145: ...JOHNSON CONTROLS 145 Appendix Material Safety Data Sheets FORM 161 01 OM1 ISSUE DATE 6 8 2018...
Страница 146: ...JOHNSON CONTROLS 146 FORM 161 01 OM1 ISSUE DATE 6 8 2018 Appendix Material Safety Data Sheets...
Страница 147: ...JOHNSON CONTROLS 147 Appendix Material Safety Data Sheets FORM 161 01 OM1 ISSUE DATE 6 8 2018...
Страница 148: ...JOHNSON CONTROLS 148 FORM 161 01 OM1 ISSUE DATE 6 8 2018 Appendix Material Safety Data Sheets...
Страница 149: ...JOHNSON CONTROLS 149 Appendix Material Safety Data Sheets FORM 161 01 OM1 ISSUE DATE 6 8 2018...
Страница 150: ...JOHNSON CONTROLS 150 FORM 161 01 OM1 ISSUE DATE 6 8 2018 Appendix Material Safety Data Sheets...
Страница 151: ...JOHNSON CONTROLS 151 Appendix Material Safety Data Sheets FORM 161 01 OM1 ISSUE DATE 6 8 2018...
Страница 152: ...JOHNSON CONTROLS 152 FORM 161 01 OM1 ISSUE DATE 6 8 2018 Appendix Material Safety Data Sheets...
Страница 153: ...JOHNSON CONTROLS 153 Appendix Material Safety Data Sheets FORM 161 01 OM1 ISSUE DATE 6 8 2018...
Страница 154: ...JOHNSON CONTROLS 154 FORM 161 01 OM1 ISSUE DATE 6 8 2018 Appendix Material Safety Data Sheets...