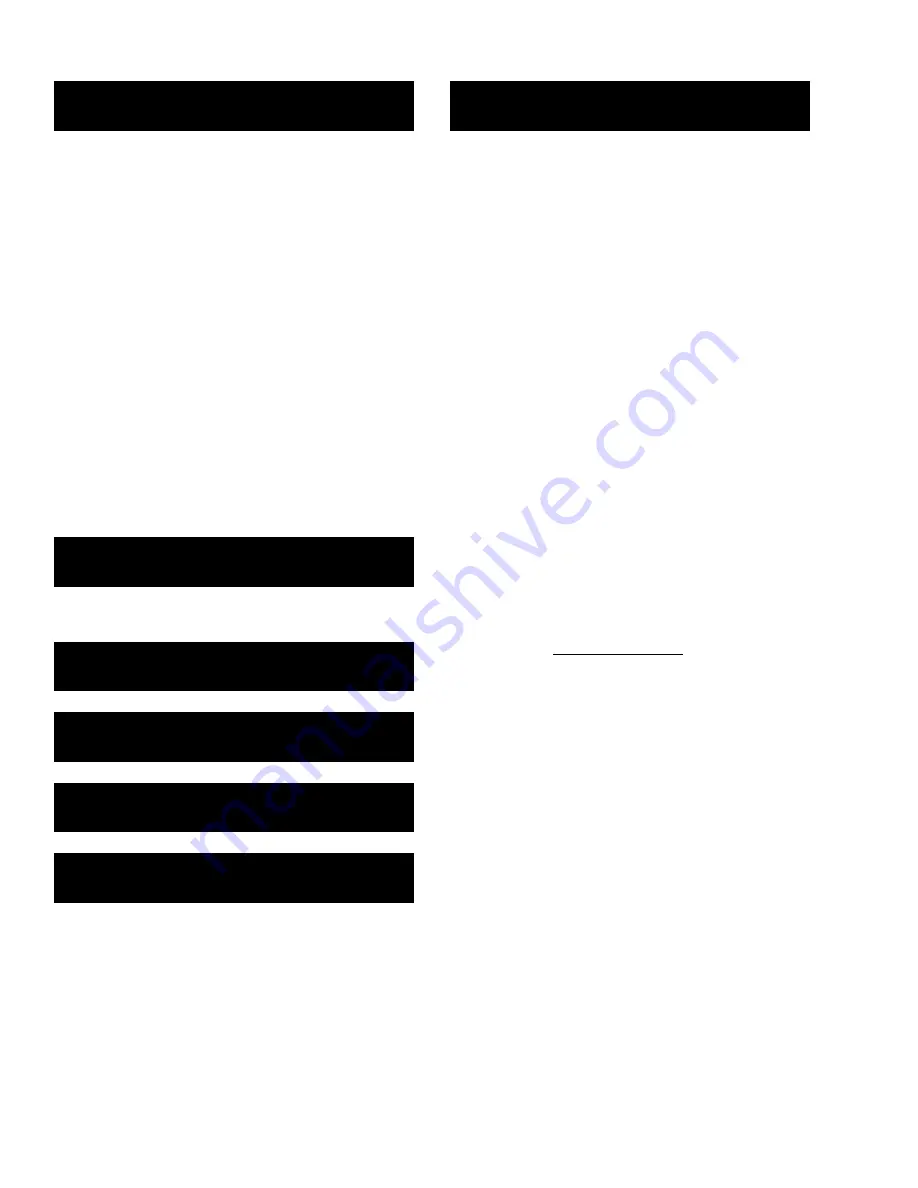
JOHNSON CONTROLS
104
FORM 150.73-NM2
ISSUE DATE: 09/07/2020
SECTION 7 – UNIT CONTROLS
A C T I V E R E M O T E C T R L
N
O
N E
There are several types of remote systems that can be
used to control or monitor the unit. The following mes-
sages indicate the type of remote control mode active:
NONE – no remote control active. Remote monitoring
may be via ISN.
ISN – YORK Talk via ISN allows remote load
limiting and temperature reset through an ISN
system.
*LOAD LIM – load limiting enabled. Can be either
stage 1 or stage 2 of limiting.
*PWM TEMP – EMS-PWM temperature reset
*Refer to the section on OPERATING CON-
TROLS.
If the micro is programmed for CURRENT FEED-
BACK ONE PER UNIT under the OPTIONS Key,
the display will show up as the first display prior to
the SYS 1 displays. Total unit current is displayed as
shown below:
U N I T A M P S = 5 4 . 0
V O L T S = 1 . 2
If the micro is programmed for CURRENT FEED-
BACK NONE, no current display will appear.
S Y S X C O M P S T A T U S
1 = X X X 2 = X X X 3 = X X X
S Y S X R U N T I M E
X X - X X - X X - X X D - H - M - S
S Y S X L L S V I S O N
H O T G A S S O L I S O F F
S Y S X F A N S T A G E 3
S Y S X A M P S = 3 6 . 0
V O L T S = 0 . 8
The preceding five messages will appear sequentially,
first for system 1, then for system 2.
The first message indicates the system and the associ-
ated compressors which are running.
The second message indicates the system run time in
days – hours – minutes – seconds. Please note that this
is not accumulated run time but pertains only to the
current system cycle.
The third message indicates the system, and whether
the liquid line solenoid or EEV pilot solenoid and hot
gas solenoid are being turned on by the microboard.
Please note that hot gas is not available for system 2, so
there is no message pertaining to the hot gas solenoid
when system 2 message is displayed.
The fourth message indicates which stage of condenser
fan operation is active.
See the section on Condenser Fan Control in the UNIT
OPERATION section for more information.
The fifth message displays current as sensed by the op-
tional current feedback circuitry. The display reads out
in amps along with the DC feedback voltage from the
module. Current is calculated by:
225A • Actual Volts
5 Volts
Individual displays will be present for each system, if
CURRENT FEEDBACK ONE PER SYSTEM is pro-
grammed under the OPTIONS Key. Combined com-
pressor current for each system is displayed.
Содержание YLUA0248 Series
Страница 4: ...JOHNSON CONTROLS 4 FORM 150 73 NM2 ISSUE DATE 09 07 2020 THIS PAGE INTENTIONALLY LEFT BLANK ...
Страница 10: ...JOHNSON CONTROLS 10 FORM 150 73 NM2 ISSUE DATE 09 07 2020 THIS PAGE INTENTIONALLY LEFT BLANK ...
Страница 14: ...JOHNSON CONTROLS 14 FORM 150 73 NM2 ISSUE DATE 09 07 2020 THIS PAGE INTENTIONALLY LEFT BLANK ...
Страница 30: ...JOHNSON CONTROLS 30 FORM 150 73 NM2 ISSUE DATE 09 07 2020 THIS PAGE INTENTIONALLY LEFT BLANK ...
Страница 44: ...JOHNSON CONTROLS 44 FORM 150 73 NM2 ISSUE DATE 09 07 2020 THIS PAGE INTENTIONALLY LEFT BLANK ...
Страница 55: ...JOHNSON CONTROLS 55 SECTION 5 TECHNICAL DATA FORM 150 73 NM2 ISSUE DATE 09 07 2020 5 5 ...
Страница 57: ...JOHNSON CONTROLS 57 SECTION 5 TECHNICAL DATA FORM 150 73 NM2 ISSUE DATE 09 07 2020 5 5 ...
Страница 59: ...JOHNSON CONTROLS 59 SECTION 5 TECHNICAL DATA FORM 150 73 NM2 ISSUE DATE 09 07 2020 5 5 ...
Страница 61: ...JOHNSON CONTROLS 61 SECTION 5 TECHNICAL DATA FORM 150 73 NM2 ISSUE DATE 09 07 2020 5 5 ...
Страница 63: ...JOHNSON CONTROLS 63 SECTION 5 TECHNICAL DATA FORM 150 73 NM2 ISSUE DATE 09 07 2020 5 5 ...
Страница 65: ...JOHNSON CONTROLS 65 SECTION 5 TECHNICAL DATA FORM 150 73 NM2 ISSUE DATE 09 07 2020 5 5 LD13901 ...
Страница 67: ...JOHNSON CONTROLS 67 SECTION 5 TECHNICAL DATA FORM 150 73 NM2 ISSUE DATE 09 07 2020 5 5 ...
Страница 71: ...JOHNSON CONTROLS 71 SECTION 5 TECHNICAL DATA FORM 150 73 NM2 ISSUE DATE 09 07 2020 5 5 LD13239 ...
Страница 73: ...JOHNSON CONTROLS 73 SECTION 5 TECHNICAL DATA FORM 150 73 NM2 ISSUE DATE 09 07 2020 5 5 ...
Страница 75: ...JOHNSON CONTROLS 75 SECTION 5 TECHNICAL DATA FORM 150 73 NM2 ISSUE DATE 09 07 2020 5 5 LD13993A 1 ...
Страница 77: ...JOHNSON CONTROLS 77 SECTION 5 TECHNICAL DATA FORM 150 73 NM2 ISSUE DATE 09 07 2020 5 5 ...
Страница 94: ...JOHNSON CONTROLS 94 FORM 150 73 NM2 ISSUE DATE 09 07 2020 THIS PAGE INTENTIONALLY LEFT BLANK ...
Страница 124: ...JOHNSON CONTROLS 124 FORM 150 73 NM2 ISSUE DATE 09 07 2020 THIS PAGE INTENTIONALLY LEFT BLANK ...