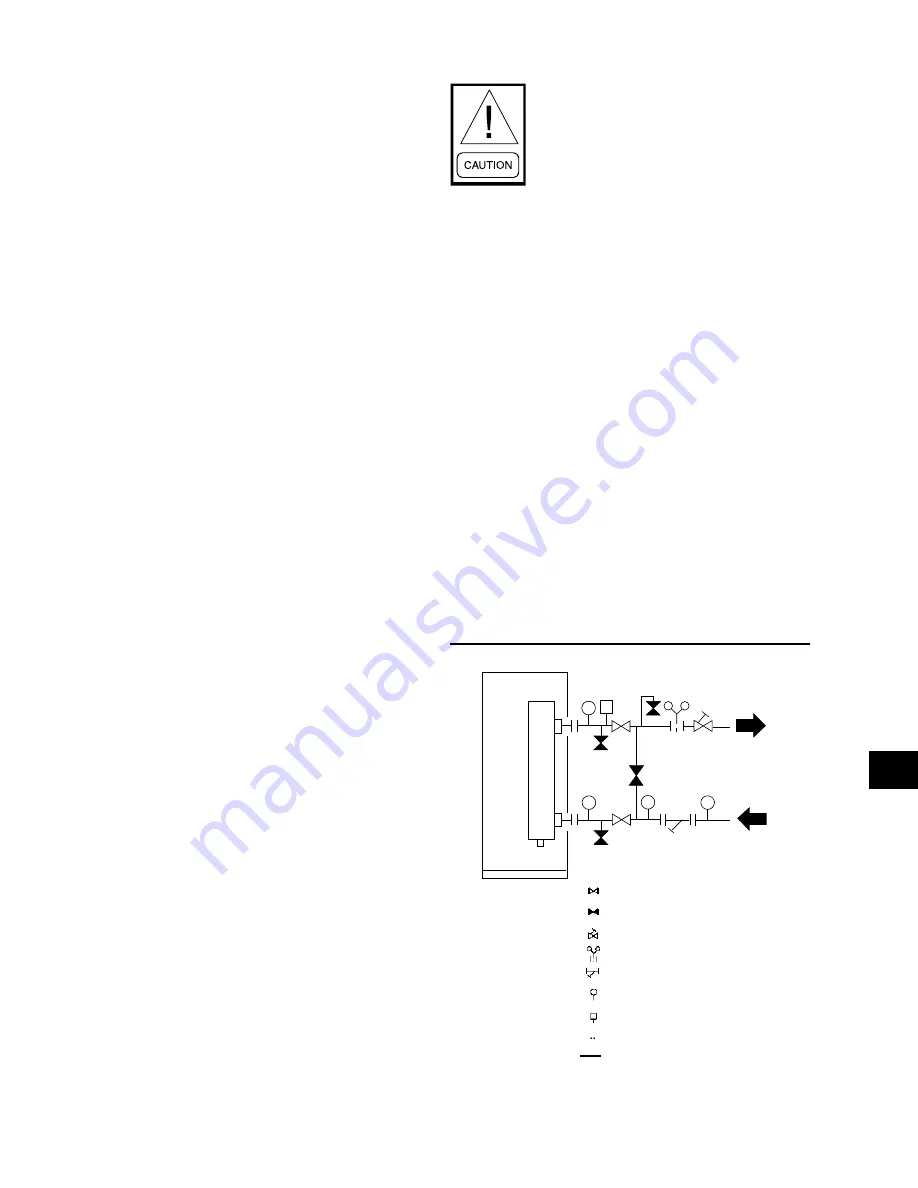
32
JOHNSON CONTROLS
FIG. 5 –
PIPEWORK ARRANGEMENT
Pipework and fittings must be separately supported to
prevent any loading on the cooler. Flexible connections
are recommended which will also minimize transmis-
sion of vibrations to the building. Flexible connections
must be used if the unit is mounted on anti-vibration
mounts as some movement of the unit can be expected
in normal operation.
Pipework and fittings immediately next to the cooler
should be readily de-mountable to enable cleaning be-
fore operation, and to facilitate visual inspection of the
exchanger nozzles.
The cooler must be protected by a strainer, preferably
of 30 mesh, fitted as close as possible to the liquid
inlet connection, and provided with a means of local
isolation.
The cooler must not be exposed to flushing velocities
or debris released during flushing. It is recommended
that a suitably sized by-pass and valve arrangement is
installed to allow flushing of the pipework system. The
by-pass can be used during maintenance to isolate the
heat exchanger without disrupting flow to other units.
Thermometer and pressure gauge connections should
be provided on the inlet and outlet connections of each
cooler.
Drain and air vent connections should be provided at all
low and high points in the pipework to permit drainage
of the system and to vent any air in the pipes.
Liquid systems at risk of freezing, due to low ambient
temperatures, should be protected using insulation and
heater tape and/or a suitable glycol solution. The liquid
pump(s) must also be used to ensure liquid is circulat-
ed when the ambient temperature approaches freezing
point. Insulation should also be installed around the
cooler nozzles. Heater tape of 21 watts per meter under
the insulation is recommended, supplied independently
and controlled by an ambient temperature thermostat
set to switch on at 37°F (21°C) above the freezing tem-
perature of the liquid.
The liquid circulation pump must be controlled by the
unit. This will ensure that when the liquid temperature
falls within 3° or 5°F (2° or 3°C) of freezing the pump
will start.
The cooler is protected by heater mats under the insu-
lation which are supplied from the unit control system
power supply. During risk of freezing the control sys-
tem should be left switched on to provide the freeze
protection function unless the liquid systems have been
drained.
Any debris left in the water pipework
between the strainer and cooler could
cause serious damage to the tubes in
the cooler and must be avoided. The
installer/user must also ensure that
thequality of the water in circulation
is adequate, without any dissolved
gases which can cause oxidation of
steel parts within the cooler.
WATER TREATMENT
The unit performance given in the Design Guide is based
on a fouling factor of 0.00025 ft
2
hr°F/Btu (0.044m2/hr
°C/kW). Dirt, scale, grease and certain types of water
treatment will adversely affect the heat exchanger sur
-
faces and therefore unit performance. Foreign matter
in the water system(s) can increase the heat exchanger
pressure drop, reducing the flow rate and causing po
-
tential damage to the heat exchanger tubes.
Aerated, brackish or salt water is not recommended for
use in the water system(s). YORK recommends that
a water treatment specialist is consulted to determine
that the proposed water composition will not affect the
evaporator materials of carbon steel and copper. The pH
value of the water flowing through the cooler must be
kept between 7 and 8.5.
LD04739
Pipework
Isolating Valve - Normally Open
Isolating Valve - Normally Closed
Flow Regulating Valve
Flow Measurement Device
Strainer
Pressure Tapping
Flanged Connection
Flow Switch
4
Содержание YCAS0098EB
Страница 36: ...36 JOHNSON CONTROLS POWER AND CONTROL PANEL LAYOUTS WYE DELTA TYPICAL FIG 8 POWER PANEL SECTION 00263VIP 4...
Страница 50: ...50 JOHNSON CONTROLS This page intentionally left blank...
Страница 61: ...61 JOHNSON CONTROLS FORM 201 18 NM7 This page intentionally left blank 7...
Страница 64: ...64 JOHNSON CONTROLS Technical Data ELEMENTARY DIAGRAM FIG 18 ELEMENTARY DIAGRAM ACROSS THE LINE START...
Страница 68: ...68 JOHNSON CONTROLS Technical Data ELEMENTARY DIAGRAM FIG 21 ELEMENTARY DIAGRAM WYE DELTA START...
Страница 70: ...70 JOHNSON CONTROLS Technical Data FIG 22A CONTROL PANEL COMPONENT LOCATIONS...
Страница 71: ...71 JOHNSON CONTROLS FORM 201 18 NM7 LD03280 FIG 22B POWER PANEL COMPONENT LOCATION 7...
Страница 72: ...72 JOHNSON CONTROLS Technical Data LEGEND LD03281...
Страница 73: ...73 JOHNSON CONTROLS FORM 201 18 NM7 LD03282 LD03283 LD03284 7...
Страница 74: ...74 JOHNSON CONTROLS Technical Data CONNECTION DIAGRAM SYSTEM WIRING LD06256 LD03231 LD03232...
Страница 75: ...75 JOHNSON CONTROLS FORM 201 18 NM7 COMPRESSOR TERMINAL BOX LD03233 7...
Страница 76: ...76 JOHNSON CONTROLS LD03285 Technical Data...
Страница 77: ...77 JOHNSON CONTROLS FORM 201 18 NM7 3 4 5 6 3 4 5 6 7 8 5 6 3 4 7 8 9 10 LD06840A 7...
Страница 113: ...113 JOHNSON CONTROLS FORM 201 18 NM7 COMPRESSOR COMPONENTS CONT D FIG 40 COMPRESSOR COMPONENTS LD03669 7...
Страница 114: ...114 JOHNSON CONTROLS COMPRESSOR COMPONENTS CONT D FIG 41 COMPRESSOR COMPONENTS LD03670 Technical Data...
Страница 181: ...181 JOHNSON CONTROLS FORM 201 18 NM7 NOTES...
Страница 182: ...182 JOHNSON CONTROLS This page intentionally left blank...
Страница 183: ...183 JOHNSON CONTROLS FORM 201 18 NM7 This page intentionally left blank...