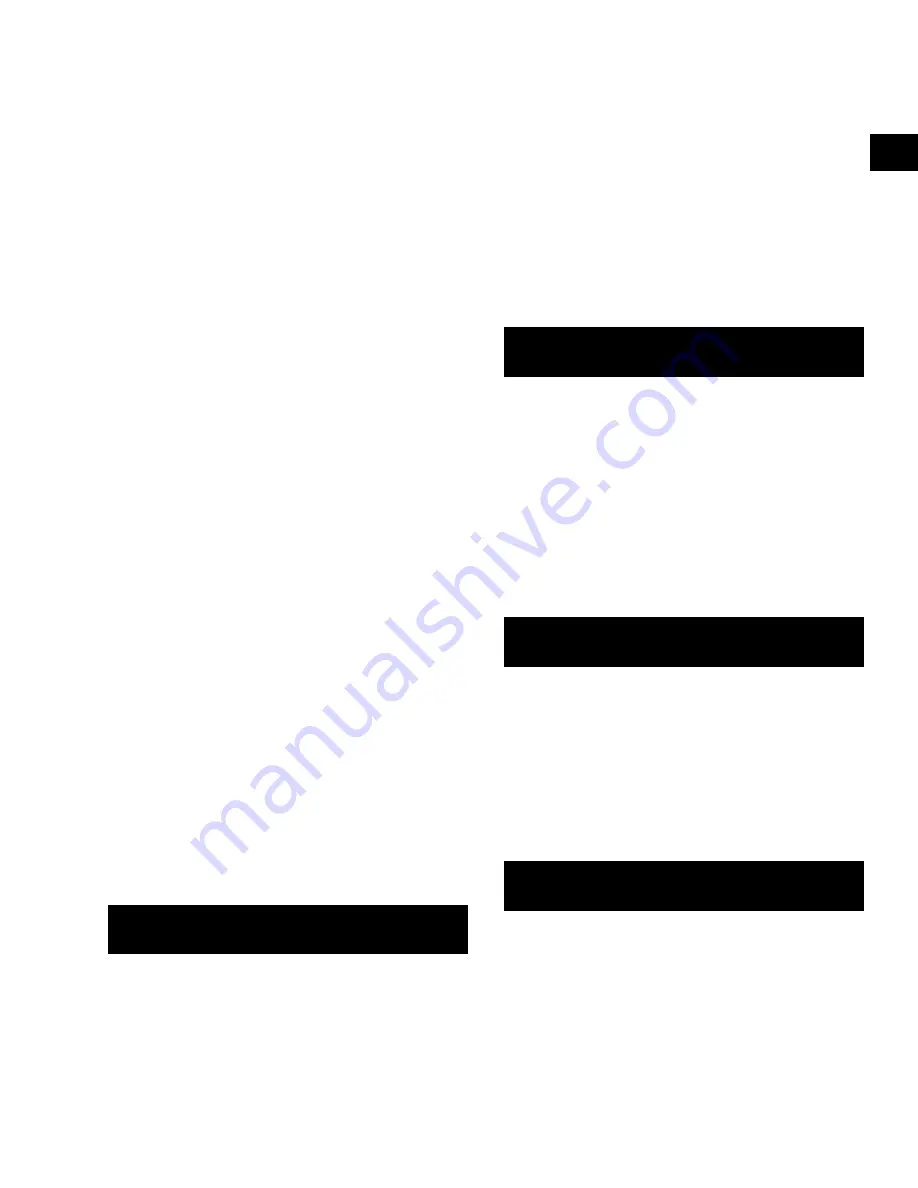
165
JOHNSON CONTROLS
FORM 201.18-NM7
the longest period acceptable in each application will
reduce cycling and maximize motor life.
600 seconds
is recommended.
The micro will accept a range of programmable values
between 300 - 600 seconds.
To program the Anti-Recycle Time, key in the required
setting and press the Enter key to store the value into
memory and scroll to the next display.
Local/Remote Communications
The panel can be programmed for “Local” or “Remote”
communications. “Local” mode allows monitoring
through the RS-485 port only. “Remote,” allows an ex-
ternal device such as an ISN or Remote Control Center
to change setpoints and programming points.
The
keys are used to change from Local to Remote.
The ENTER Key must be pressed to save the selection
in memory.
Imperial/SI Units Display
This allows the operator to select the display messages
to display Imperial Units (PSIG, F, etc.) or SI (Scientific
International, Bars, C, etc.).
The
keys are used to change from Imperial to SI
units. The ENTER Key must be pressed to save the
selection in memory.
Automatic/Manual “Lead/Lag”
The chiller may be selected for manual lead/lag or auto-
matic lead/lag. In some cases the operator may want to
manually select the system that is desired to be the lead
system. In most cases, automatic lead/lag is selected to
allow the micro to attempt to balance run time between
the system. Details of manual and automatic lead / lag
operation are outlined in Section 1.21.
The
keys are used to change from Automatic to
Manual lead/lag. The ENTER key must be pressed to
save the selection in memory.
limit cutout value. The chiller can then continue to run
automatically at reduced capacity until the cause of the
excessive current is attended to.
The micro will accept between 30 - 105% for the unload
point. The motor current safety will shut the compressor
down whenever current exceeds 115%.
If the programmable limit is set between 100% and
105% of full load current, this safety will protect against
excessive current causing compressor shutdown due to
extremely high ambient, high chilled liquid tempera-
ture, and condenser malfunction caused by dirt or fan
problems.
If the programmable limit is set below 100% of full load
current, this feature can be used for “demand limiting”.
This is important when demand limiting is critical due
to power requirements or limitations in the building (See
also Section 1.10).
For the first 60 seconds of operation, the unloading safety
is disabled. After this time, if motor current exceeds
the programmed limit, the SYS x CRNT LIMITING
message will appear on the display and a 1 second un-
load pulse will be sent to the slide valve of the affected
compressor every 5 seconds, until the motor current
drops below the programmed limit. The message will
be removed and additional loading will take place when
motor current drops below 90% of the programmed
threshold.
Typically, this setpoint should be set at 100% for
maximum motor protection. Programming for 100%
is recommended.
When programming values below
100% use of a leading “0” is required, e.g. 085%.
To program the High Motor Current Unload, key in the
required setting and press the Enter key to store the value
into memory and scroll to the next display.
Anti-Recycle Time
The Anti-Recycle Timer controls the minimum time
between starts for each compressor. This is the time
available for the heat build up caused by inrush current
at start to be dissipated before the next start. Insufficient
cooling time between starts can cause heat build up
and motor damage. A fast compressor start response
is needed in some applications and not in others. Al-
though the minimum setting allowed on this timer will
avoid excessive heat build up, adjusting the timer for
A N T I R E C Y C L E T I M E R
= 6 0 0 S E C S
L O C A L / R E M O T E M O D E
L O
C
A L
D I S P L A Y U N I T S
I M
P E R I A L
L E A D / L A G C O N T R O L
A U T O
M
A T I C
8
Содержание YCAS0098EB
Страница 36: ...36 JOHNSON CONTROLS POWER AND CONTROL PANEL LAYOUTS WYE DELTA TYPICAL FIG 8 POWER PANEL SECTION 00263VIP 4...
Страница 50: ...50 JOHNSON CONTROLS This page intentionally left blank...
Страница 61: ...61 JOHNSON CONTROLS FORM 201 18 NM7 This page intentionally left blank 7...
Страница 64: ...64 JOHNSON CONTROLS Technical Data ELEMENTARY DIAGRAM FIG 18 ELEMENTARY DIAGRAM ACROSS THE LINE START...
Страница 68: ...68 JOHNSON CONTROLS Technical Data ELEMENTARY DIAGRAM FIG 21 ELEMENTARY DIAGRAM WYE DELTA START...
Страница 70: ...70 JOHNSON CONTROLS Technical Data FIG 22A CONTROL PANEL COMPONENT LOCATIONS...
Страница 71: ...71 JOHNSON CONTROLS FORM 201 18 NM7 LD03280 FIG 22B POWER PANEL COMPONENT LOCATION 7...
Страница 72: ...72 JOHNSON CONTROLS Technical Data LEGEND LD03281...
Страница 73: ...73 JOHNSON CONTROLS FORM 201 18 NM7 LD03282 LD03283 LD03284 7...
Страница 74: ...74 JOHNSON CONTROLS Technical Data CONNECTION DIAGRAM SYSTEM WIRING LD06256 LD03231 LD03232...
Страница 75: ...75 JOHNSON CONTROLS FORM 201 18 NM7 COMPRESSOR TERMINAL BOX LD03233 7...
Страница 76: ...76 JOHNSON CONTROLS LD03285 Technical Data...
Страница 77: ...77 JOHNSON CONTROLS FORM 201 18 NM7 3 4 5 6 3 4 5 6 7 8 5 6 3 4 7 8 9 10 LD06840A 7...
Страница 113: ...113 JOHNSON CONTROLS FORM 201 18 NM7 COMPRESSOR COMPONENTS CONT D FIG 40 COMPRESSOR COMPONENTS LD03669 7...
Страница 114: ...114 JOHNSON CONTROLS COMPRESSOR COMPONENTS CONT D FIG 41 COMPRESSOR COMPONENTS LD03670 Technical Data...
Страница 181: ...181 JOHNSON CONTROLS FORM 201 18 NM7 NOTES...
Страница 182: ...182 JOHNSON CONTROLS This page intentionally left blank...
Страница 183: ...183 JOHNSON CONTROLS FORM 201 18 NM7 This page intentionally left blank...