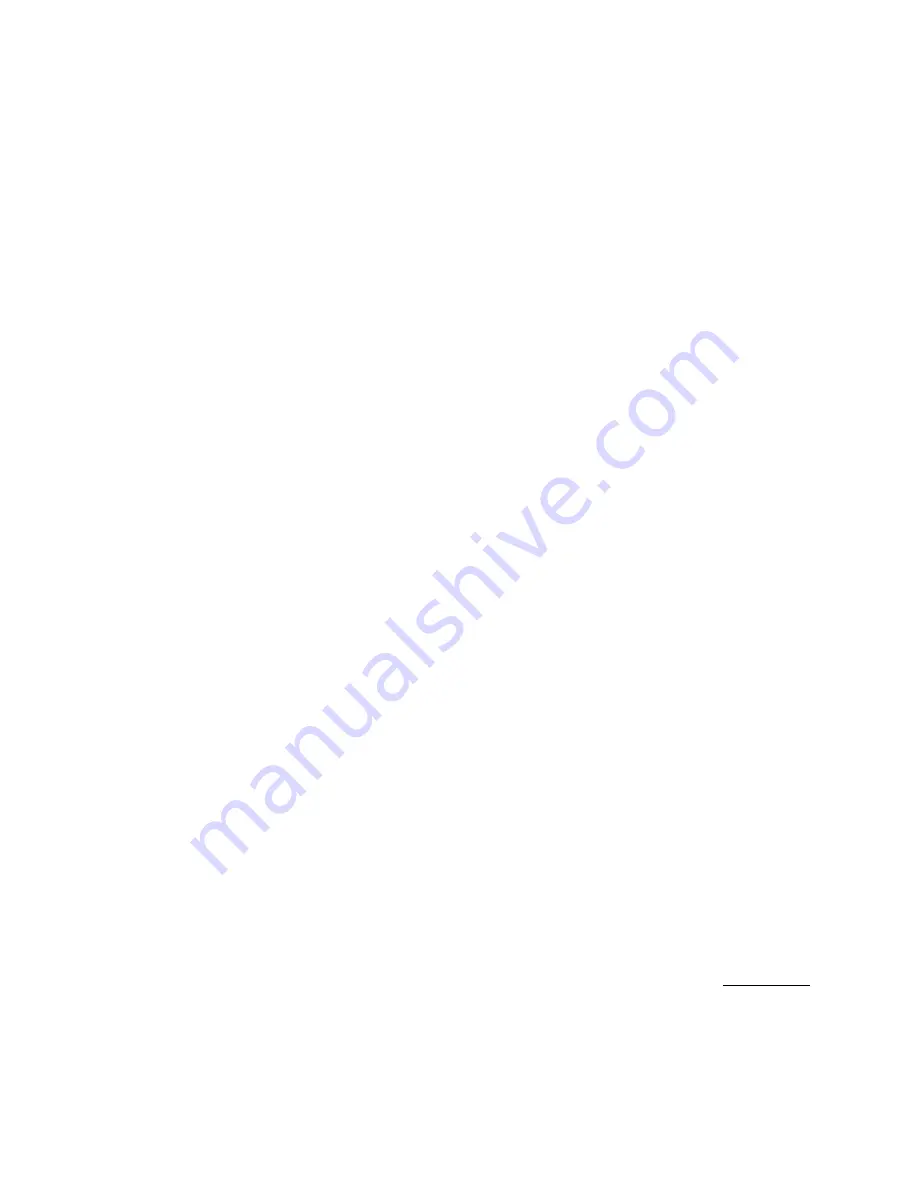
34
YORK INTERNATIONAL
SINGLE CIRCUIT UNITS
J. Verify that field wiring matches the 3-phase power
requirements of the compressor. See nameplate.*
K. Assure 115VAC Control Power to TB1 has 30A mini-
mum capacity.**
L. Be certain all control bulbs are inserted completely
in their respective wells and are coated with heat
conductive compound.
2. PANEL CHECKS (POWER ON SYSTEM SWITCH
“OFF”)
A. Apply 3-phase power and verify its value.*
B. Apply 115VAC and verify its value on the terminal
block in the lower left of the Power Panel. Make the
measurement between terminals 41 and 2. Should
be 115VAC
±
10%**.
C. Assure crankcase heater is on. Allow crankcase
heater to remain on a minimum of 24 hours before
start-up. This is important to assure no refrigerant
is in the oil at start-up!
INITIAL START-UP
After the operator has read the preceding pages, has
become familiar with the control panel and its functions,
and has performed the preceding unit checks and panel
checks, the unit can be put into operation. Proceed by
setting the switches as follows:
1. Panel Switches:
A. Set the Return or Leaving Chilled Water Temp. Set-
point to the desired temperature as discussed ear-
lier in the manual (pages 25 - 28).
B. Assure the Micro Logic Board jumpers/switches are
configured for the unit design and the system’s re-
quirement. See page 31 or 32.
C. Assure all user adjustable cut-outs are properly set.
See page 33 for a list of these cut-outs. Adjust them
as required.
2. Place the System Switch to the ON position. See the
OPERATING SEQUENCE for unit operation.
The compressor will start and a flow of liquid should be
noted in the liquid indicator. After several minutes of op-
eration, the bubbles will disappear and there will be a
solid column of liquid when the unit is operating nor-
mally. On start-up, foaming of the oil may be evident in
the compressor oil sight glass. After the water tempera-
ture has been pulled down to operating conditions, the
oil should be clear. Normal operation of the unit is evi-
denced by a hot discharge line 4 (discharge superheat
should not drop below 50°F (10°C), clear oil in the com-
* See Fig. 7
** See Fig. 9
pressor crankcase, solid liquid refrigerant in the liquid
indicator and usually no more than 2 PSIG (13.8 kPaG)
variation in suction pressure for any given set of operat-
ing conditions.
Allow the compressor to run for a short time, being ready
to stop it immediately if any unusual noise or other ad-
verse condition should develop. When starting the com-
pressor, always make sure the oil pump is functioning
properly. Compressor oil pressure must be as described
under F2 Fault-Low Oil Pressure (page 21).
Check the system operating parameters. Do this by se-
lecting various readouts such as pressure and tempera-
ture.
Compare these to test gauge readings.
CHECKING SUPERHEAT AND SUBCOOLING
The subcooling should always be checked when charg-
ing the system with refrigerant and/or before setting the
superheat.
When the refrigerant charge is correct, there will be no
bubbles in the liquid sightglass with the system operat-
ing under full load conditions, and there will be 10°F
(5.5°C) to 15°F (8.3°C) subcooled liquid refrigerant leav-
ing the condenser.
An overcharged system should be guarded against.
Evidences of overcharge are as follows:
a. If a system is overcharged, the discharge pressure
will be higher than normal. (Normal discharge/con-
densing pressure can be found in refrigerant tempera-
ture/pressure chart; use entering air temperature
+30°F (16.6°C) for normal condensing temperatures.
b. The temperature of the liquid refrigerant out of the
condenser should not be more than 15°F (8.33°C)
less than the condensing temperature. (The tempera-
ture corresponding to the condensing pressure from
refrigerant temperature/pressure chart.)
The subcooling temperature should be taken by record-
ing the temperature of the liquid line at the outlet of the
condenser and recording the compressor discharge
pressure and converting it to a temperature from tem-
perature/pressure chart.
Example:
Discharge Pressure 202 PSIG
(1391 kPa) converted to
102°F (38.9°C)
Minus Liquid Line Temperature 87°F (30.6°C)
Subcooling =
15°F (8.3°C)
After the subcooling is set at 10°-15°F (5.5°-8.3°C) the
superheat should be checked.
The superheat should be checked only after steady op-
eration of the chiller has been established, the leaving
chilled liquid has been pulled down to the required tem-
Содержание YCAG18
Страница 11: ...YORK INTERNATIONAL 11 FORM 150 40 NM25 SINGLE CIRCUIT UNITS LD01712 ELEMENTARY DIAGRAM FIG 4 CONTINUED...
Страница 12: ...12 YORK INTERNATIONAL SINGLE CIRCUIT UNITS FIG 4 CONTINUED LD01713 CONNECTION DIAGRAM ELECTRICAL BOX...
Страница 43: ...YORK INTERNATIONAL 43 FORM 150 40 NM25 DUAL CIRCUIT UNITS FIG 29 CONTINUED ELEMENTARY DIAGRAM LD01716...
Страница 44: ...44 YORK INTERNATIONAL DUAL CIRCUIT UNITS FIG 29 CONTINUED CONNECTION DIAGRAM ELECTRICAL BOX LD01717...
Страница 99: ...YORK INTERNATIONAL 99 FORM 150 40 NM25...