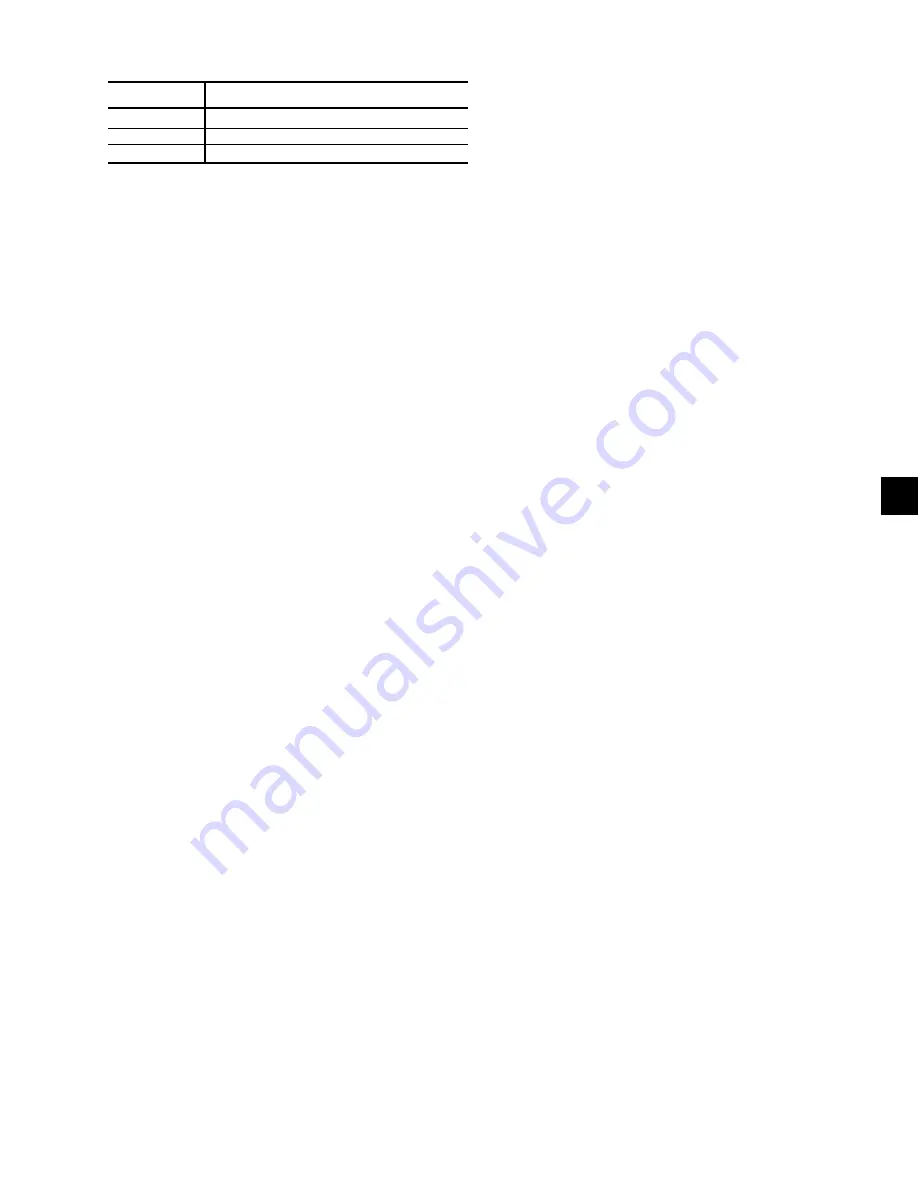
FORM 160.55-O1 (604)
133
YORK INTERNATIONAL
Application #CT’s Furnished in Motor Ter mi nal Box
E-M Starter 3
SS Starter 0
VS Drive 0
COMPRESSOR LUBRICATION SYSTEM
The chiller lubrication system consists of the oil pump,
oil
Þ
l ter, oil cooler and all interconnecting oil pip ing
and passages. (See Fig. 59) There are seven main points
with in the motor-compressor which must be sup plied
with forced lubrication as follows:
1. Compressor Drive Shaft (Low Speed)
a. Shaft seal.
b. Front and rear journal bearings - one on each
side
of driving gear.
c. Low speed thrust bearing (for ward and re verse).
2. Compressor Driven Shaft (High Speed)
a. Forward and reverse high speed thrust bear ing.
b. Three jour nal bearings (YDTJ67 through 95 and
YDTL108 through 126). Two journal bearings
(YDTL131 and 144).
3. Speed Increasing Gears
a. Meshing sur fac es of drive and pinion gear teeth.
To pro vide the re quired amount of oil under the nec-
es sary pressure to properly lu bri cate these parts, a motor
driv en sub mers ible oil pump is lo cat ed in a re mote oil
sump.
Upon press ing of the “
COM PRES SOR START
”
switch on the con trol cen ter, the oil pump is im me -
di ate ly en er gized. After a 30 sec ond delay to allow the
system oil pressure to sta bi lize, the compressor motor
will start. The oil pump will continue to run during the
entire op er a tion of the compressor, and for 150 sec onds
during compressor coastdown.
The sub merged oil pump takes suction from the sur-
round ing oil and dis charg es it to the oil cooler where heat
is rejected. The oil
ß
ows from the oil cooler to the oil
Þ
lter. The oil leaves the
Þ
lter and
ß
ows to the emer gen cy
oil res er voir where it is dis trib ut ed to the com pres sor
bear ings. The oil lu bri cates the com pres sor ro tat ing
com po nents and is re turned to the oil sump.
Since the emer gen cy oil res er voir is at the high est point
in the lu bri ca tion sys tem, it provides an oil supply to
the var i ous bear ings and gears in the event of a sys tem
shutdown due to power failure. The reservoir, lo cat ed on
the top of the compressor, al lows the oil to be dis trib ut ed
through the pas sag es by grav i ty
ß
ow, thus pro vid ing nec-
essary lu bri ca tion dur ing the com pres sor coastdown.
OIL PUMP
For normal operation the oil pump should operate at
all times dur ing the chiller operation. Man u al pump
op er a tion may be used to es tab lish sta ble oil pres-
sure be fore start ing. When de pressed and re leased,
the “
MAN U AL OIL PUMP
” key will operate the oil
pump for 10 min utes and then au to mat i cal ly shut off.
To stop the oil pump sooner, de press the “
MAN U AL
OIL PUMP
” key again.
On shutdown of the sys tem for any reason, the oil pump
op er ates and con tin ues to run for 150 sec onds. The sys-
tem can not restart during that time in ter val.
OIL HEAT ER
During long idle pe ri ods, the oil in the com pres sor oil
res er voir tends to absorb as much re frig er ant as it can
hold, de pend ing upon the tem per a ture of the oil and
the pressure in the reservoir. As the oil tem per a ture is
low ered, the amount of re frig er ant ab sorbed will be in-
creased. If the quantity of re frig er ant in the oil be comes
excessive, vi o lent oil foaming will result as the pressure
within the sys tem is low ered on start ing. This foaming is
caused by re frig er ant boil ing out of the oil as the pres sure
is lowered. If this foam reaches the oil pump suc tion,
the bearing oil pres sure will
ß
uc tu ate with pos si ble
tem po rary loss of lu bri ca tion, caus ing the oil pres sure
safe ty cutout to actuate and stop the system.
SHELLS
- The cooler and con dens er shells are rolled
carbon steel plate with fu sion welded seams. A thick tube
sheet is welded to each end of the shell and is drilled
and reamed to ac com mo date the tubes. All shells have
a design work ing pres sure of 15 PSIG and are pres sure-
tested at 30 PSIG.
TUBES
- In di vid u al ly-re place able, 3/4" O.D., in te gral-
Þ
nned copper heat ex chang er tubes are used in the cool er
and con dens er. The tubes are roller-ex pand ed into the
tube sheets, pro vid ing a leak-proof seal.
COMPACT WATER BOXES
- Re mov able water
box es are fabricated of steel. The stan dard design
work ing pres sure is 150 PSIG and the box es are tested
at 225 PSIG. Integral steel water baf
ß
es are lo cat ed and
weld ed with in the water box to provide re quired 1, 2,
or 3-pass arrangements. Water nozzle con nec tions with
5
Содержание R123
Страница 2: ...YORK INTERNATIONAL 2 FORM 160 55 O1 604...
Страница 11: ...FORM 160 55 O1 604 11 YORK INTERNATIONAL THIS PAGE INTENTIONALLY LEFT BLANK TO MAINTAIN FORMAT...
Страница 35: ...FORM 160 55 O1 604 35 YORK INTERNATIONAL THIS PAGE INTENTIONALLY LEFT BLANK TO MAINTAIN FORMAT 2...
Страница 37: ...FORM 160 55 O1 604 37 YORK INTERNATIONAL THIS PAGE INTENTIONALLY LEFT BLANK TO MAINTAIN FORMAT 2...
Страница 63: ...FORM 160 55 O1 604 63 YORK INTERNATIONAL THIS PAGE INTENTIONALLY LEFT BLANK TO MAINTAIN FORMAT 2...
Страница 67: ...FORM 160 55 O1 604 67 YORK INTERNATIONAL 2 THIS PAGE INTENTIONALLY LEFT BLANK TO MAINTAIN FORMAT...
Страница 73: ...FORM 160 55 O1 604 73 YORK INTERNATIONAL THIS PAGE INTENTIONALLY LEFT BLANK TO MAINTAIN FORMAT 2...
Страница 111: ...FORM 160 55 O1 604 111 YORK INTERNATIONAL THIS PAGE INTENTIONALLY LEFT BLANK TO MAINTAIN FORMAT 2...
Страница 136: ...YORK INTERNATIONAL 136 FORM 160 55 O1 604 Operational Maintenance LD00470 FIG 61 ASSEMBLY OF DEHYDRATOR...
Страница 155: ...FORM 160 55 O1 604 155 YORK INTERNATIONAL NOTES...