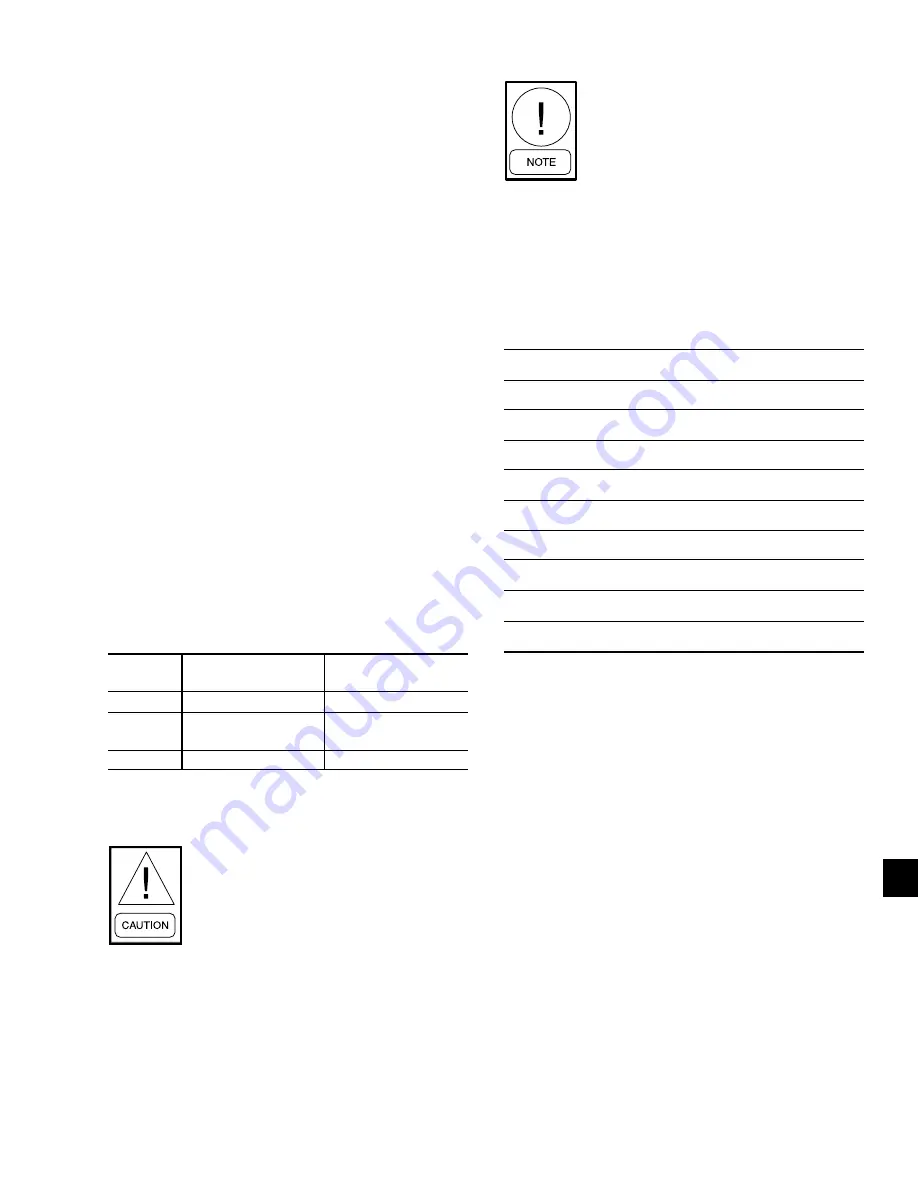
125
YORK INTERNATIONAL
FORM 201.18-NM4
Dip switches 4 through 8 are spares
and have no function.
$
5. Program the required operating values into the
micro for cut-outs, safeties, etc. and record them
in the chart below. See Page 168 for details.
If Default Values are desired for programming
convenience, press the PROGRAM key, 6140,
and ENTER. This loads default values. Record
these values in the chart below.
PROGRAMMED VALUES
Refrigerant Type = _________________________
Dischg Press Cut-out = ____________ kPa (PSIG)
Disch Press Unld = ________________ kPa (PSIG)
Suction Press Cut-out = ____________ kPa (PSIG)
High Amb Cut-Out = ___________________ °C (°F)
Low Amb Cut-Out = ___________________ °C (°F)
Leaving Chilled Liquid Temp Cut-Out = _____ °C (°F)
High Motor Current Unload = ____________ % FLA
Anti-Recycle Time = ____________________ Secs
$
6. Program the Chilled Liquid Setpoint/Range and
record:
Setpoint = __________________ °C (°F)
Range = ________ to ________ °C (°F)
Keep in mind that the Target temperature dis-
played by the micro should equal the desired
leaving water temperature.
$
7. Assure that the CLK jumper J18 on the Micro-
processor Board is in the ON position (Top 2
pins).
$
8. Set the Time and Date.
$
9. Program the Daily Schedule start and stop times.
Panel Checks
(Power ON – Both System Switches “OFF”)
$
1. Apply 3-phase power and verify its value (See
Fig. 8, page 35).
$
2. Apply 115VAC and verify its value on the ter-
minal block in the lower left of the Power Panel.
Make the measurement between terminals 5 and
2 (See Fig. 12, page 40). The voltage should be
/- 10%.
$
3. Assure the heaters on each compressor are on.
Allow the compressor heaters to remain on a
minimum of 24 hours before startup. This is im-
portant to assure that no refrigerant is in the com-
pressor oil at start-up!
$
4. Program the dip switches on the microproces-
sor board for the desired operating requirements.
See Page 152. OPEN = Left side of switch
pushed down. CLOSED = Right side of switch
pushed down.
Verify the selections by pressing the OPTIONS
Key on the control panel. Check them off.
Damage to the chiller could result if
switches are improperly programmed.
$
14. Assure that evaporator TXV bulbs are strapped
onto the suction lines at 4 or 8 o’clock posi-
tions.
$
15. Assure that the 15 ton economizer TXV bulbs
are strapped onto the compressor economizer
supply lines at 4 or 8 o’clock positions.
SWITCH
SWITCH “OPEN”
SWITCH “CLOSED”
SETTING
SETTING
1
Water Cooling
Brine Cooling
2
Standard Ambient
Low Ambient
Control
Control
3
Refrigerant R-407C
Refrigerant R-22
7
Содержание Millennium YCAS Series
Страница 36: ...36 YORK INTERNATIONAL FIG 8 POWER PANEL SECTION CONT D OPTIONS PANEL LAYOUT TYPICAL 00246VIP Installation ...
Страница 49: ...49 YORK INTERNATIONAL FORM 201 18 NM4 7 This page intentionally left blank ...
Страница 65: ...65 YORK INTERNATIONAL FORM 201 18 NM4 LD04179 7 ...
Страница 79: ...79 YORK INTERNATIONAL FORM 201 18 NM4 This page intentionally left blank 7 ...
Страница 83: ...83 YORK INTERNATIONAL FORM 201 18 NM4 This page intentionally left blank 7 ...
Страница 87: ...87 YORK INTERNATIONAL FORM 201 18 NM4 LD04268 7 ...
Страница 119: ...119 YORK INTERNATIONAL FORM 201 18 NM4 COMPRESSOR COMPONENTS CONT D FIG 57 COMPRESSOR COMPONENTS LD03669 7 ...
Страница 120: ...120 YORK INTERNATIONAL COMPRESSOR COMPONENTS CONT D FIG 58 COMPRESSOR COMPONENTS LD03670 Technical Data ...
Страница 121: ...121 YORK INTERNATIONAL FORM 201 18 NM4 COMPRESSOR COMPONENTS CONT D FIG 59 COMPRESSOR COMPONENTS LD03671 7 ...