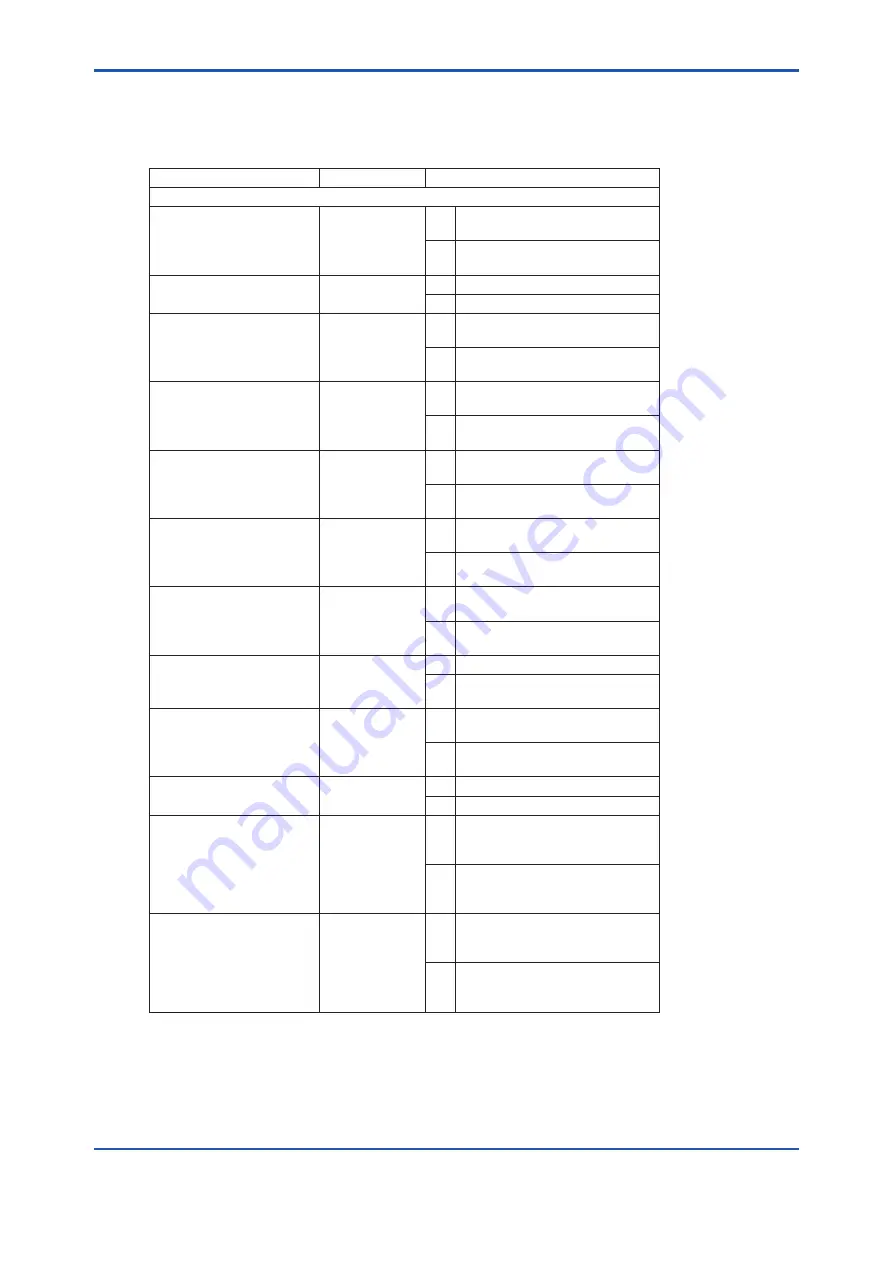
<8. Detailed Data Setting>
8-9
IM 11M13A01-04E
8.5.2 Setting Contact Output
Set the contact outputs following Table 8.10.
Table 8.10
Parameter Codes for Contact Output Setting
Set item
Parameter code
Set value
Contact output 1
Operation
E10
0 Operated in closed status.
(Normally de-energized)
1 Operated when open. (Normally
energized)
(Note 1)
Error
E20
0 Not operated if an error occurs.
1 Operated if an error occurs.
High-high alarm
E21
0 Not operated if a high-high alarm
occurs.
1 Operated if a high-high alarm
occurs.
(Note 2)
High alarm
E22
0 Not operated if a high alarm
occurs.
1 Operated if a high alarm occurs.
(Note 2)
Low alarm
E23
0 Not operated if a low alarm
occurs.
1 Operated if a low alarm occurs.
(Note 2)
Low-low alarm
E24
0 Not operated if a low-low alarm
occurs.
1 Operated if a low-low alarm
occurs.
(Note 2)
During maintenance
E25
0 Not operated during
maintenance.
1 Operated during maintenance
(see Subsection 8.3.1).
During calibration
E26
0 Not operated during calibration.
1 Operated during calibration (see
Subsection 8.3.1).
Output range change
E27
0 Not operated when changing
ranges.
1 Operated when changing
ranges.
(Note 3)
During warm-up
E28
0 Not operated during warming up.
1 Operated during warming up.
Calibration gas
pressure decrease
E29
0 Not operated while a calibration
gas pressure decrease, contact
is being closed.
1 Operated while a calibration gas
pressure decrease, contact is
being closed.
(Note 4)
Unburnt gas
detection
E32
0 Not operated while an unburnt
gas detection, contact is being
closed.
1 Operated while an unburnt
gas detection, contact is being
closed.
(Note 5)
Note 1: Contact output 2 remains closed.
Note 2: The oxygen concentration alarm must be preset (see Section 8.4).
Note 3: Range change answer-back signal. For this action, the range change must be preset during the setting of contact inputs
(see Section 8.5).
Note 4: Calibration gas pressure decrease answer-back signal. Calibration gas pressure decrease must be selected beforehand
during the setting of contact inputs.
Note 5: Non-combusted gas detection answer-back signals. “Non-combusted gas” detection must be selected during the setting of
contact inputs.
Содержание ZR202S
Страница 12: ...xi IM 11M13A01 04E Introduction ...
Страница 18: ...Blank Page ...
Страница 61: ...Blank Page ...
Страница 129: ...Blank Page ...
Страница 141: ...Blank Page ...
Страница 153: ......
Страница 155: ......
Страница 157: ......
Страница 159: ...Blank Page ...
Страница 160: ......
Страница 161: ......
Страница 162: ......
Страница 163: ......