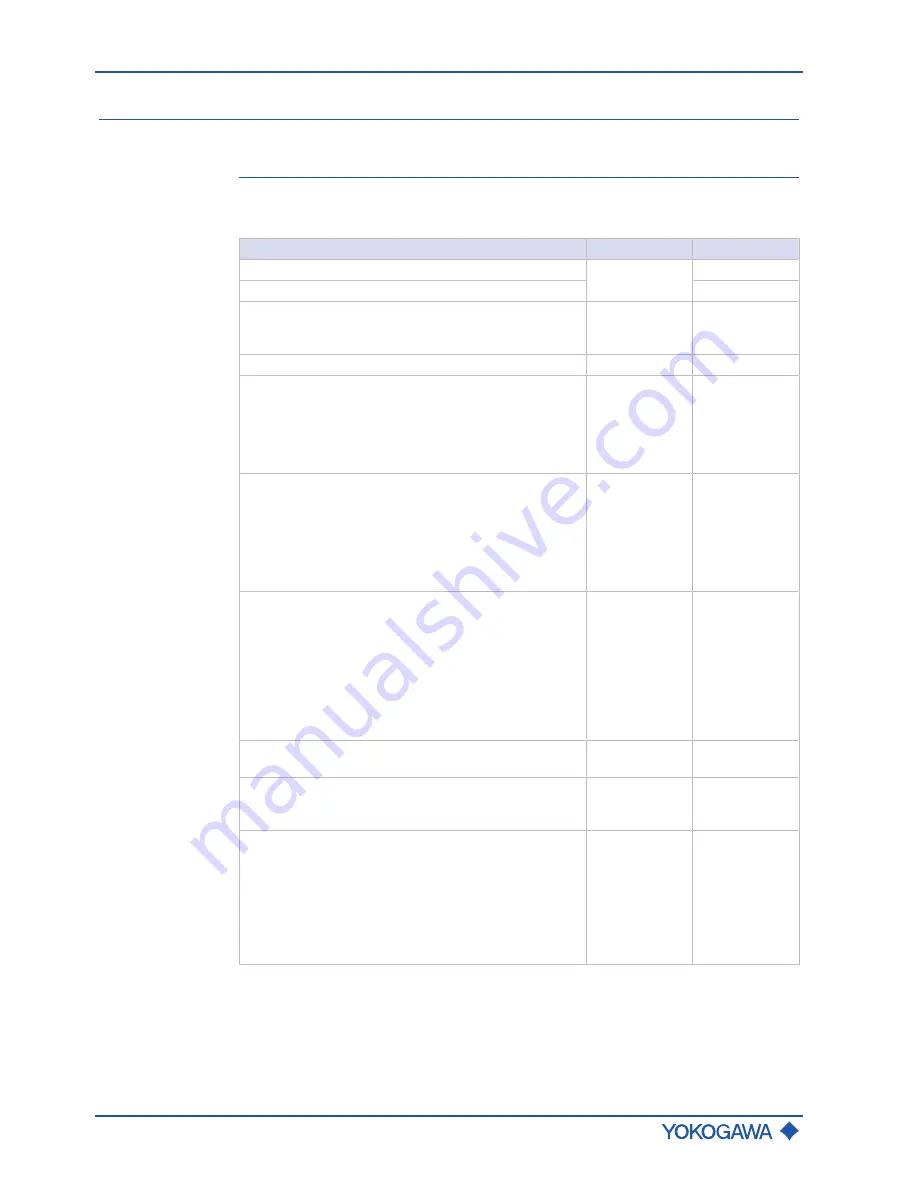
General Instruction Manual
Product specification
Scope of delivery
10 / 90
IM 01U10B00-00EN-R, 3rd edition, 2018-07-09
4 Product specification
4.1 Scope of delivery
The scope of delivery of the flow meter must be checked for completeness using the fol-
lowing list:
Integral type
Remote type
Sensor
1 unit
1 unit
Transmitter
1 unit
Connecting cable
-
Length accord-
ing to model
code
Operating tool for terminals
2 units
2 units
2-inch pipe mounting bracket set
▪ Sheet metal console (bracket)
▪ Mounting bracket (U-bracket)
▪ Fixing materials (2 nuts, 2 washers, 4 Allen
screws)
-
1 set
Pipe installation set for sensor (with device option PD)
▪ Sheet metal console (bracket)
▪ Mounting bracket (U-bracket)
▪ Fixing plate
▪ Fixing materials (14 nuts, 6 washers, 4 bolts, 8
notched washers, 4 rubber buffers)
-
1 set
Cable glands are included for a device with metric
cable entries and without Ex approval.
Please note:
▪ No cable glands are included for a device with
cable entries other than metric.
▪ For a device with Ex approval the inclusion of ca-
ble glands may vary. Please refer to the applicable
Explosion Proof Type Manual.
2 units
2 units
Cable glands for connecting cable between sensor
and transmitter, metal (pre-installed)
-
2 units
Termination kit for shortening the connecting cable
(not with option L000 or Y000), including instruction
booklet.)
-
1 set
Document folder with this content:
▪ Product CD/DVD (includes the complete product
documentation)
▪ Quick reference guide
▪ Safety Regulations Manual
▪ Further documents like certificates (depending on
model code)
1 folder
1 folder