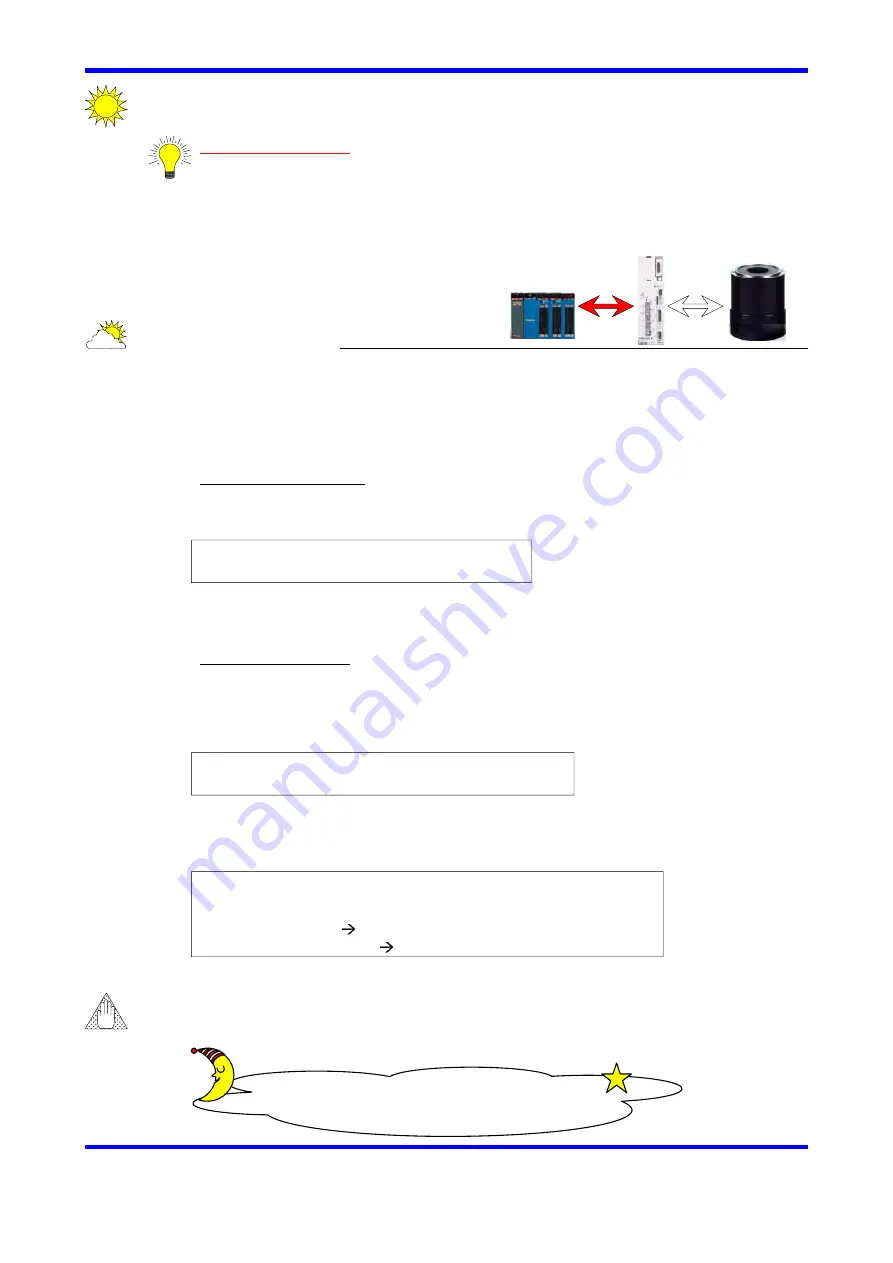
《目次》 《索引》
TI 71M01D03-03
1st Edition : 2007.03.12-00
STEP 4.
Scaling
Very important item!
Set appropriate scaling for optimized operation commands.
What’s “scaling”:
This is the function to set the amount of command pulses from PLC for 1 turn
(DYNASERV) or 1m (LINEARSERV)to a any value. This function allows users to set
move command without complicated computation.
Note: Described as [axis command pulses] hereinafter
4.1 Recommended scaling value
Scaling value can be set freely, however, it is recommended to set it a value,
which makes you easier to calculate for move distance, such as below examples.
Rotation (DYNASERV):
For angular command...
Multiple number of 360 [deg] simplifies to calculate move distance [deg] since
it is number of pulses for 1 turn.
Recommendation:360000
(1/1000 [deg] for 1 [axis command pulses])
・Rotate 90 degrees ⇒
Command pulse 90000
・Rotate 206.32°degrees ⇒
Command pulse 206320
For index command...
If total number of indexing points can not be divided by 360
°, it helps to simplify
computation for axis command pulses against move distance [deg] if a multiplied number of such
total number of indexing points.
・For positioning 7 indexing points per revolution
Recommendation:700000
(Amount of command pulses per revolution: 100000)
Linear (LINEARSEV):
Computation can be simplified by setting as move distance per pulse since it is
number of pulses per 1m.
Recommendation:1000000
(1 [μm] per 1 [axis command pulse)
・For 20 [mm] move
Amount of command pluses: 20000
・For 1008.2 [mm] move
Amount of command pluses: 1008200
Setup method will be explained in the next page!
See also “6.1.7 Coordinate Systems” in the TI
Notice
Recommended scaling value is over 100000.
If a lower scaling value is set, motor may moves unstably, such as overshoot,
because the command becomes rough.
PLC
DRIVE
MOTOR
4-1