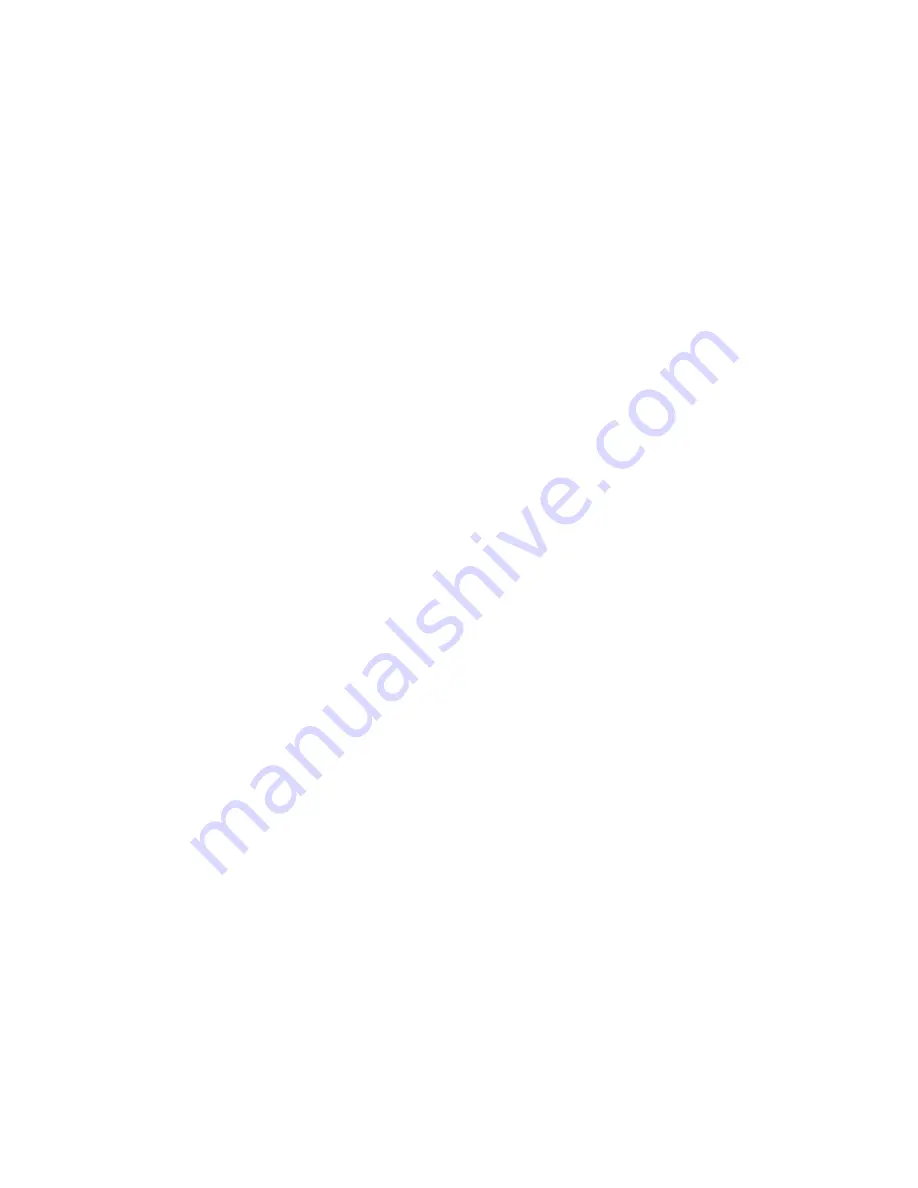
7
INSTALLING TECHNICIAN/CONTRACTOR'S RESPONSIBILITIES
1.
Discuss with the customer detailed information about the structure to be conditioned, local weather (typical design, extreme
temperature/humidity conditions, cooling and heating hours), previous and existing HVAC equipment (if any), usage and dependence
on new HVAC equipment or YMGI products.
2.
Performing a cooling/heating load calculation by using commercially available professional programs/methods such as Right-J
(Manual J) for residential HVAC applications and Right-CommLoad (ASHRAE RTS/CLTD) for light commercial and commercial
HVAC applications.
3.
Contact your YMGI distributor/sales department or contact YMGI directly to obtain additional information to fully understand your
YMGI products, including but not limited to product features, cooling/heating performance at standard ratings/conditions and extreme
conditions, allowed indoor and outdoor temperature and humidity ranges, installation, operation, maintenance, service, warranty,
parts and any other issues pertaining to YMGI products.
4.
Select the correct (most suitable) YMGI product unit models and accessories necessary for your HVAC applications and list them in
the proposal/quote, in writing, on company's quotation form or letter head, based upon the information you collected from 1, 2 and 3
listed above.
5.
List your currently valid HVAC license number and EPA number in your proposal/quote.
6.
Make sure you are the only party to perform the entire installation and you will not sub-contract any part of the installation to any non-
licensed parties or persons. You will be solely responsible for the entire installation that you have been contracted.
7.
Make sure you have all the materials you need to properly, completely and correctly finish the installation. The YMGI units and
accessories may be just a portion of what you will need for the project. When support issues arise, remember YMGI employees and
YMGI distributors/sales, dealers and agents are not installers and may only provide suggestions. You are the only one qualified to
determine what other materials you need to complete the installation.
8.
When connecting electrical wires, follow all NEC, state and local codes and ensure the installation of all YMGI units and accessories
meet these requirements.
9.
Connect the unit to a correctly sized electrical power source. If the unit is installed in an area where lightning or storms occur
frequently, a correctly sized and type of power surge protector must be installed between the outdoor unit and the power source.
10. Select the correct types and sizes of HVAC circuit breakers, disconnect switch boxes, wires and conduit from circuit breaker to
disconnect box and then from disconnect box to outdoor unit.
11. Select the proper location for installing indoor units and outdoor units with all factory requirements being followed (cooling/heating
air inlets and outlets are not blocked, or restricted, mounting structure is secure, installation for convenience is considered, allow
adequate clearance for maintenance/service and all applicable codes are met).
12. Cap/tape the two ends of every copper line before running them through any structure to keep any foreign substances from entering
the copper line causing contamination. Label the copper lines A-A, B-B, C-C, D-D, or any other identifying marks on each pair of
copper lines and wiring cable sets to keep from cross-piping or cross-wiring in multiple zone installations or where pipes for different
single zone systems are close to one another.
13. Secure the wiring cables that connect between the indoor unit and outdoor unit, following all applicable NEC, state and local codes
for your installation. If there are no special NEC, state or local codes to govern how these wires are to be installed, you can tape/cable
tie them along with insulated copper line.
14. Tighten all pipe and wire connections ensuring there is no leakage or false/loose connections.
15. Conduct a positive pressure leakage test, checking each of the inter-connecting copper lines between each indoor unit and outdoor
unit by charging with dry-
nitrogen at the outdoor unit’s service port (
NOTE:
do not back-seat stopping valve
). A liquid soap solution
shall be applied at all pipe connections to check for leakage. A 1/4” - 5/16” hose/valve adaptor may be needed if you have a 1/4”
traditional manifold hose connection.
16. If there is no positive leaking, then conduct a negative pressure leakage test, checking all inter-connecting copper lines between
each indoor unit and outdoor unit by pulling vacuum at th
e outdoor unit’s service port (
NOTE: do not back-seat stopping valve
)
and checking that a vacuum level of 500 Microns can be held for at least 20 minutes.
17.
If there is no leakage found at any of the refrigeration pipe connections, flip up the indoor unit’s face panel and remove its filter,
carefully pour some clear water onto the up-right aluminum coil surface to test if the water can drain freely out of each of the indoor
unit’s without finding any leakage.
18. If there is water leakage found, locate the source of the leak and correct it. Only after everything is clear and all the necessary
inspections made, engage the correct electrical power to the system.
19. Then back-seat stopping valves of the outdoor unit to release refrigerant from the outdoor unit into the inter-connecting pipes and
the indoor unit.
20. Make sure both the indoor unit and outdoor unit are powered on correctly, operating the indoor unit in fan mode first. Then move on
to test cooling, dehumidifying/drying, heating and other modes.
21. Read refrigerant pressures and pipe/valve temperatures only after the system is stabilized (normally 10 minutes after cooling/heating
mode is started successfully). Record this data into the technician checklist in the lower half section of the Limited Product Warranty
Registration Card/Form.
22. Adjust refrigerant charging level (remove refrigerant if pipe is shorter, the temperature is colder; add refrigerant if pipe is longer the
temperature is warmer), following the manufacturer's instructions. If the average pipe length is shorter or longer than 25' and
pressure/temperature readings at the outdoor unit service valves are not falling into normal ranges.
23. Explain to the user/owner about proper unit operation and maintenance. Leave your contact information to allow them to reach you.
If the customer finds the unit does not work properly and cannot resolve the issue themselves, check the customer's
units/parts/accessories and correct the issue if there is one. Communicate with YMGI-technical support line at (866)833-3138 x 703,
if further help is necessary.
Following these requirements will aid in ensuring that the units to be installed meet general HVAC practicing standards and necessary
factory requirements. Finding any possible problems early and preventing any further damage to the unit will help to ensure a properly
working unit for many years.
Содержание VRFI-07EL-D2B(55)5
Страница 13: ...13 Location for securing the installation pane Schematic drawing of hooks...
Страница 30: ...30...