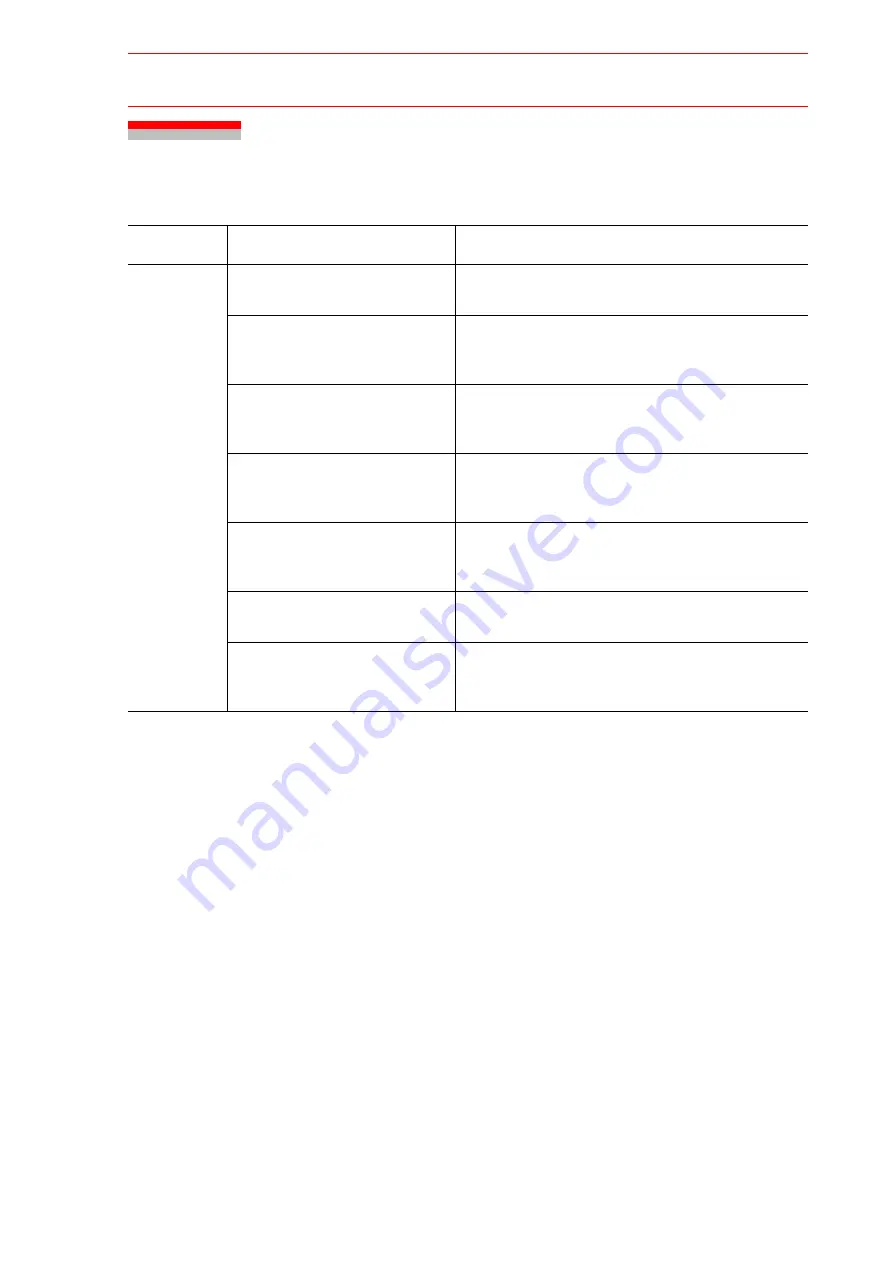
9.2 Cause and Remedy of Welding Section Failure
9-3
HW0480311
HW0480311
9.2
Cause and Remedy of Welding Section Failure
Table. 12 Failure Analyses for Welding Section
Fault
Cause
Remedy
Blowholes
and pits
occur.
Excessive oil, rust, or paint
adheres to the base metal.
Carefully remove the adherent substances to
clean the base metal.
Oil adheres to the welding wire.
Or rust occurs.
Carefully store and handle the welding wire.
Remove the oil or rust from the feeding roller or
conduit.
Sufficient shielding gas does
not flow.
Check for gas leakage. Also check that the gas
regulator has been correctly adjusted and the gas
cylinder is not empty.
Gas shielding in the welding
section does not properly work
due to wind, etc.
When the wind blows hard, stop the operation or
use a screen, etc. to help block the wind.
Spatters adhere to the nozzle
and the gas does not flow out
smoothly.
Often remove the spatters from the nozzle and
apply spatter preventive agent to the interior of the
nozzle.
The quality of the shielding gas
is poor.
Replace the shielding gas with one of better qual-
ity.
The nozzle is too far from the
arc point.
Keep the proper length of the wire stickout (10 mm
to 25 mm) to perform welding. Increase the gas
flow amount.
75/129