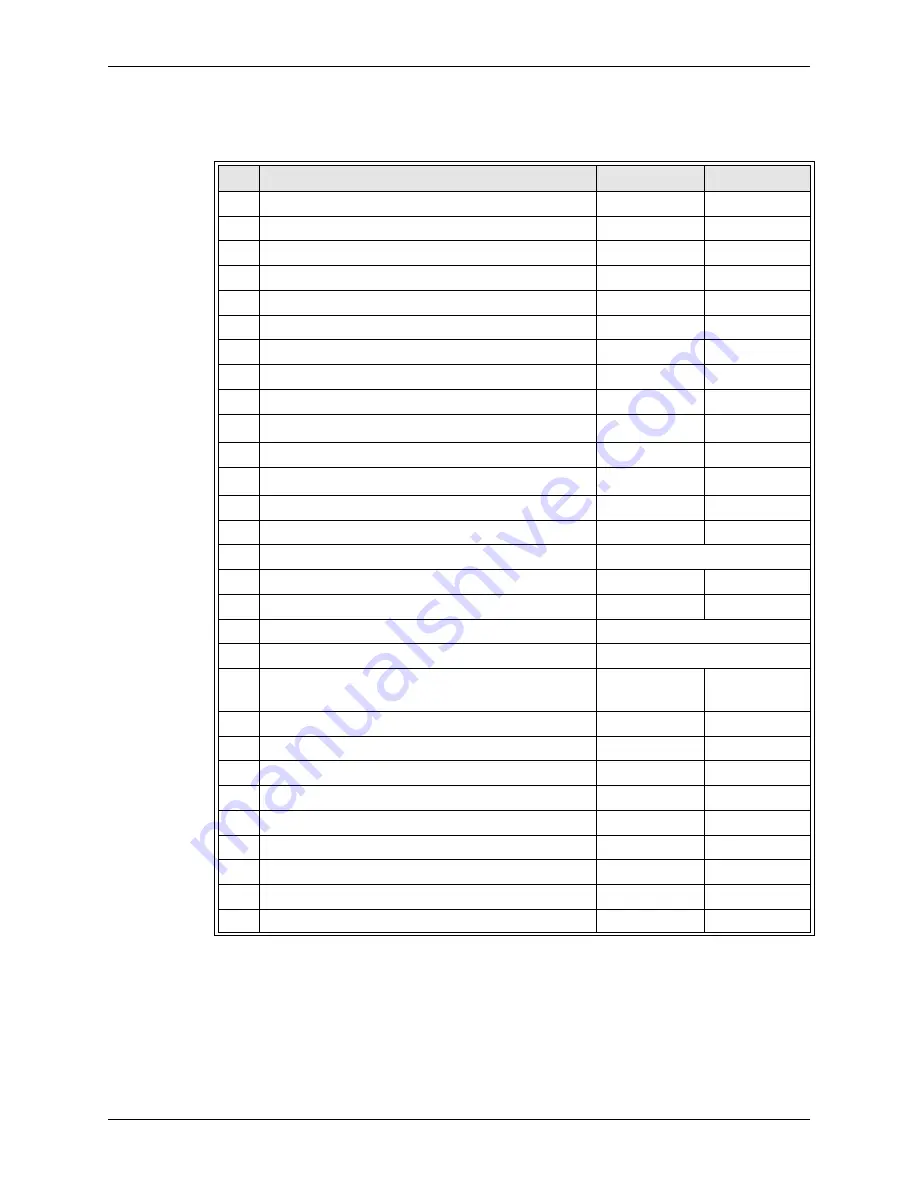
EQUIPMENT DESCRIPTION
MH-Series Positioner Manual with MotoMount
3-4
MOTO
MAN
3.2.1
Type II Specifications
See Table 3-2 for MH-series Type II drive assembly specifications.
*
External axis default settings
**
Weld capacity is at 100% duty cycle.
*** The In-position Maximum Motion is the maximum motion expected if the
cycle start command is given while the safety zone is violated. This assumes
utilizing the position switches in the safety circuit, and includes the motion
required to clear the switch actuators and implement an E-Stop.
See Appendix A for drive assembly performance charts.
See Section 4.3 for installation instructions.
Table 3-2 MH-series Type II Specifications
Series Component
MH1000
MH3000
Motoman P/N
146356-3
146356-4
*
Axis Type
Rotation
Rotation
Rated Load – kgf
1000
3000
Rated MHT Load @ CG Off Center – kgf @ mm
6300 @ 23
6300 @ 69
Headstock Speed – rpm
20.2
6.7
180-degree Sweep Time – sec
1.98
4.95
Rated CG Off Center – mm
152
152
Rated CG Overhang – mm
750
70
Load @ 500 mm CG Overhang – kgf
1400
1400
Rated Inertia – kg*m
2
173
2475
Rated Holding Torque – Nm
1491
4473
**
Rated Weld Current – Amps
1200
1200
Allowable Thrust – kgf
3000
3000
Motor Power – kW
4.5
4.5
*
Motor P/N, YEC
SGMDH-45A2B-YR14
*
Motor Speed – rpm
2000
2000
*
Rated Acceleration Time – sec
0.3
0.3
Motor P/N, Motoman
142142-1
Reducer
RV-320C
*
Total Reduction Ratio – R
11575/117
(98.932 est.)
11575/39
(296.795 est.)
Repeatability – mm/mm
TBD
.00003
Repeatability w/MotoMount – mm/mm
TBD
.000055
E-Stop Response – sec
TBD
.3
E-Stop Response – deg
TBD
6
***
In-position Maximum Motion – deg
10
Face Plate Through Hole – mm
110
110
Tail Stock Through Hole – mm
45
45
Drive Assy Weight – kgf/lbs
1180/2600
1180/2600
Standard Tool Radius – mm
1000
1000