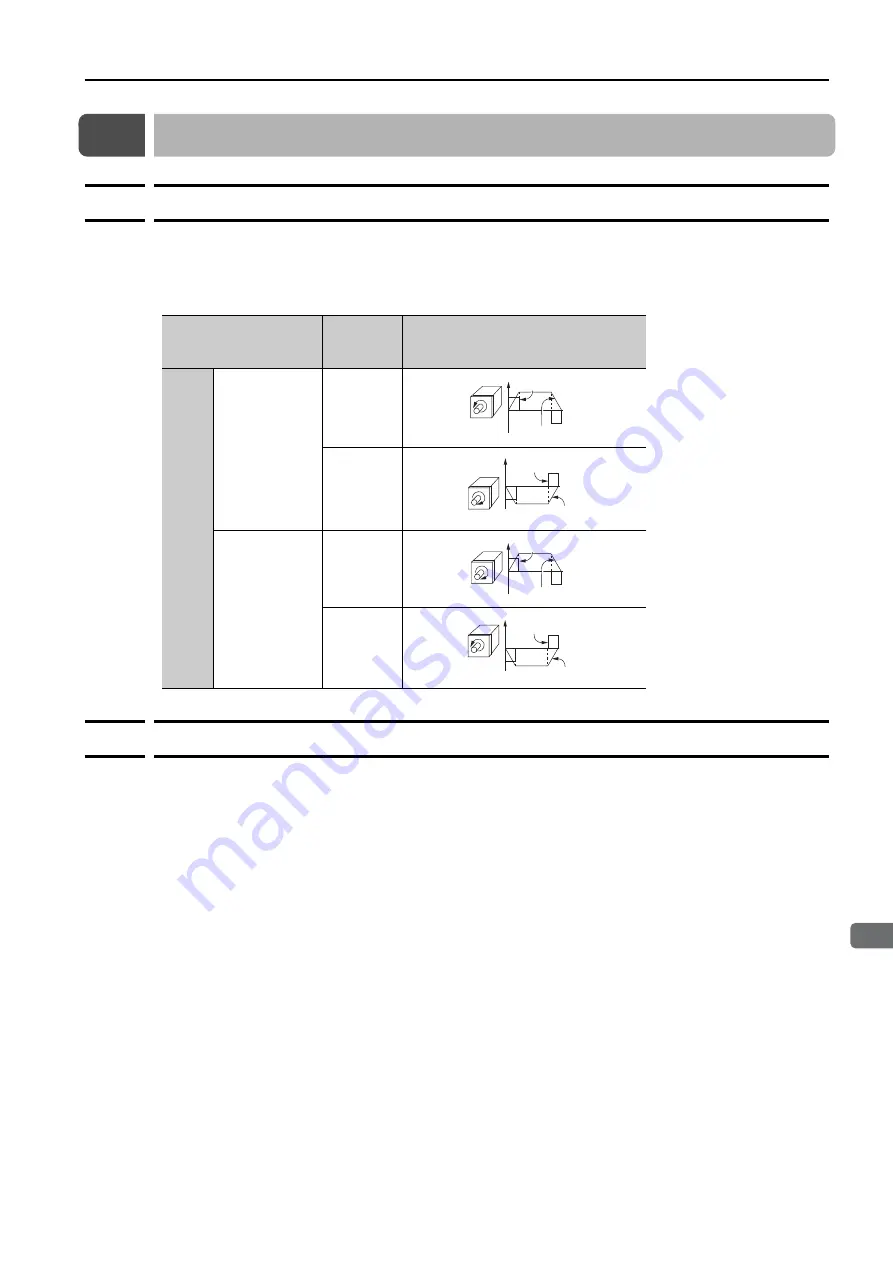
5.4 Settings That Must Be Adjusted to the System
5.4.1 Motor Direction Setting
5-23
5
Setup
5.4
Settings That Must Be Adjusted to the System
5.4.1
Motor Direction Setting
You can reverse the direction of Servomotor rotation by changing the setting of Pn000 =
n.
X (Direction Selection) without changing the polarity of the position reference.
The default setting for forward rotation is counterclockwise (CCW) as viewed from the load end
of the Servomotor.
5.4.2
Electronic Gear Settings
The minimum unit of the position data that is used to move a load is called the reference unit.
The reference unit is used to give travel amounts, not in pulses, but rather in distances or other
physical units (such as
μ
m or
°
) that are easier to understand.
The electronic gear is used to convert the travel distances that are specified in reference units
to pulses, which are required for actual movements.
With the electronic gear, one reference unit is equal to the workpiece travel distance per refer-
ence pulse input to the SERVOPACK. In other words, if you use the SERVOPACK’s electronic
gear, pulses can be read as reference units.
Note: If you set an electronic gear in the host controller, normally set the electronic gear ratio in the SERVOPACK to
1:1.
Parameter
Forward/
Reverse
Reference
Feedback Signal from SERVOPACK
Pn000
n.
0
Use CCW as
the forward
direction.
[default setting]
Forward
reference
Reverse
reference
n.
1
Use CW as the
forward
direction.
(Reverse
Rotation Mode)
Forward
reference
Reverse
reference
CCW
Time
+ Torque reference
Motor speed
CW
Motor speed
Torque reference
Time
+
CW
Torque referenc
Motor speed
Time
+
CCW
Motor speed
Torque reference
Time
+