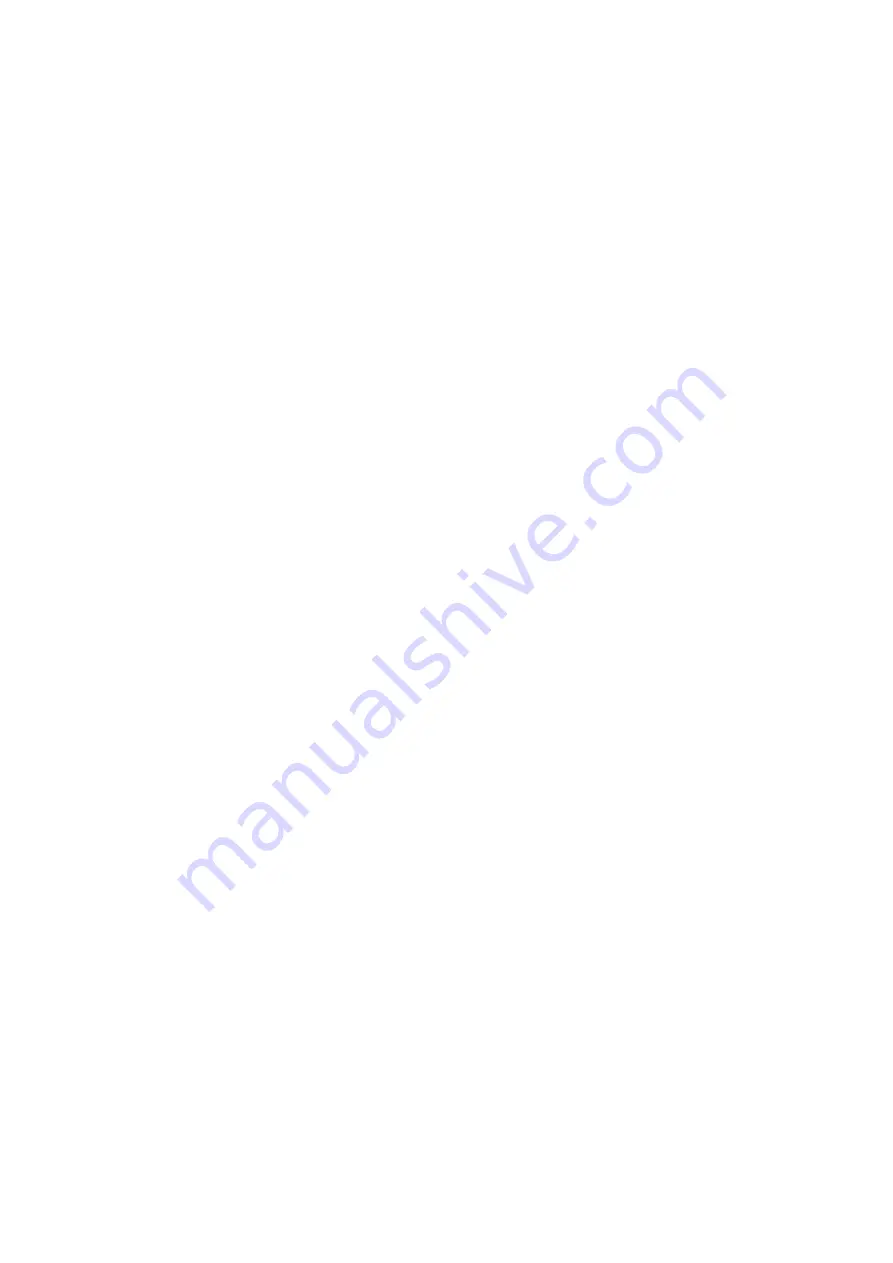
29
©
2019
Columbus McKinnon Industrial Products GmbH
Lifting/lowering the load
The load is lifted by pressing the
▲
-button, it is lowered by pressing the
▼
-button.
If the used unit is equipped with a gear limit switch (optional), then while assembling the electric rope winch, the different switching
points or lifting heights (the number depends on the model of the gear limit switch, at least two) are adjusted. Upon reaching them, the
lifting unit is switched off electrically. In this case, the lifting unit only responds when pressing the control button for movement in the
opposite direction.
If the gear limit switch is designed with more than two switching points, additional switching points may have been defined in the lifting
unit between the lowest and highest switching points. If one of these points is reached while coiling or uncoiling the wire rope on the
drum, the lifting unit is similarly deactivated electrically, but movement in the same direction is possible. For this, the corresponding
control button must be released and pressed again.
Response to release of a slack rope switch
The slack rope switch is activated in most cases when a load is being lowered. The load remains suspended on an obstacle, it is stuck
on an obstacle or is deposited on the floor. In all these cases, rope movement is possible only in the direction of the rope winch (control
key
↑
). If an obstacle blocks the way, it must be removed. The lowering operation can finally be continued.
Stop and EMERGENCY STOP
To stop the load movement, release the UP or DOWN push button. The winch must stop. If the winch does not stop, press the
EMERGENCY STOP switch and the crane switch!
ATTENTION: After pressing the EMERGENCY STOP switch, the device is not electrically dead.
If the unit does not respond to the release of the push button: Stop work immediately! Get the unit checked and repaired by a qualified
electrician.
I
NSPECTION
,
S
ERVICE
&
R
EPAIR
Service and inspections may only be carried out by a competent person.
The inspection must determine that all safety devices are present and fully operational and covers the condition of the hoist, lifting gear,
accessories and supporting constructions.
The service intervals and inspections noted are for normal working conditions. Adverse working conditions, e. g. heat or chemical
environments, can dictate shorter periods.
• The Yale RPE electric rope winch corresponds to the FEM Group 1Bm/M3 in accordance with FEM 9.511. This theoretically results in
a service life of 400 operating hours under full load.
This is equivalent to 10 years under normal operating conditions. After this period the hoist requires a general overhaul. More
information can be found in DGUV Vorschrift 54 or FEM 9.755.
Attention: Maintenance work requires subsequent function testing with nominal load.
• Visually check the pendant control switch and all cable for damage.
• Check the proper fastening of the rope winches to the supporting structure.
• Function check of the brakes (incl. triggering the EMERGENCY STOP button)
• Function check of the limit switches (optional)
• Function check of the overload circuit breaker (optional)
• Function check of the slack rope switch (optional)
• Function check of all installed safety devices
Regular Inspections, Service And Testing
According to the existing national/international accident prevention or safety specifications, lifting units must be checked
• At least once per year by a competent person
• According to the risk assessment of the operating company,
• Before the initial start-up,
• Before restart following a shutdown
• After basic alterations. The concerned use conditions (e.g. operation in galvanizing facilities) can dictate shorter inspection intervals.
Repair work may only be carried out by a specialist workshop that uses original Yale spare parts. The inspection (mainly consisting of a
visual inspection and a function check) must determine that all safety devices are complete and fully operational and cover the condition
of the unit, suspension, equipment and supporting structure with regard to damage, wear, corrosion or any other alterations.
Initial operation and recurring inspections must be documented (e.g. in the CMCO works certificate of compliance).
If required by the trade association, the results of inspections and appropriate repairs must be verified.
If the hoist (from 1 t lifting weight) is fitted on or in a trolley, or if the hoist is used to move a lifted load in one or several directions, the
installation is considered to be a crane and the further inspections must be carried out, in accordance with DGUV Vorschrift 54 Cranes.
Paint damage should be touched up in order to avoid corrosion. All joints and sliding surfaces should be slightly lubricated. In case of
heavy contamination, the unit must be cleaned.
ATTENTION! Power supply must be disconnected while inspecting the device, unless the type of the examination excludes
this!