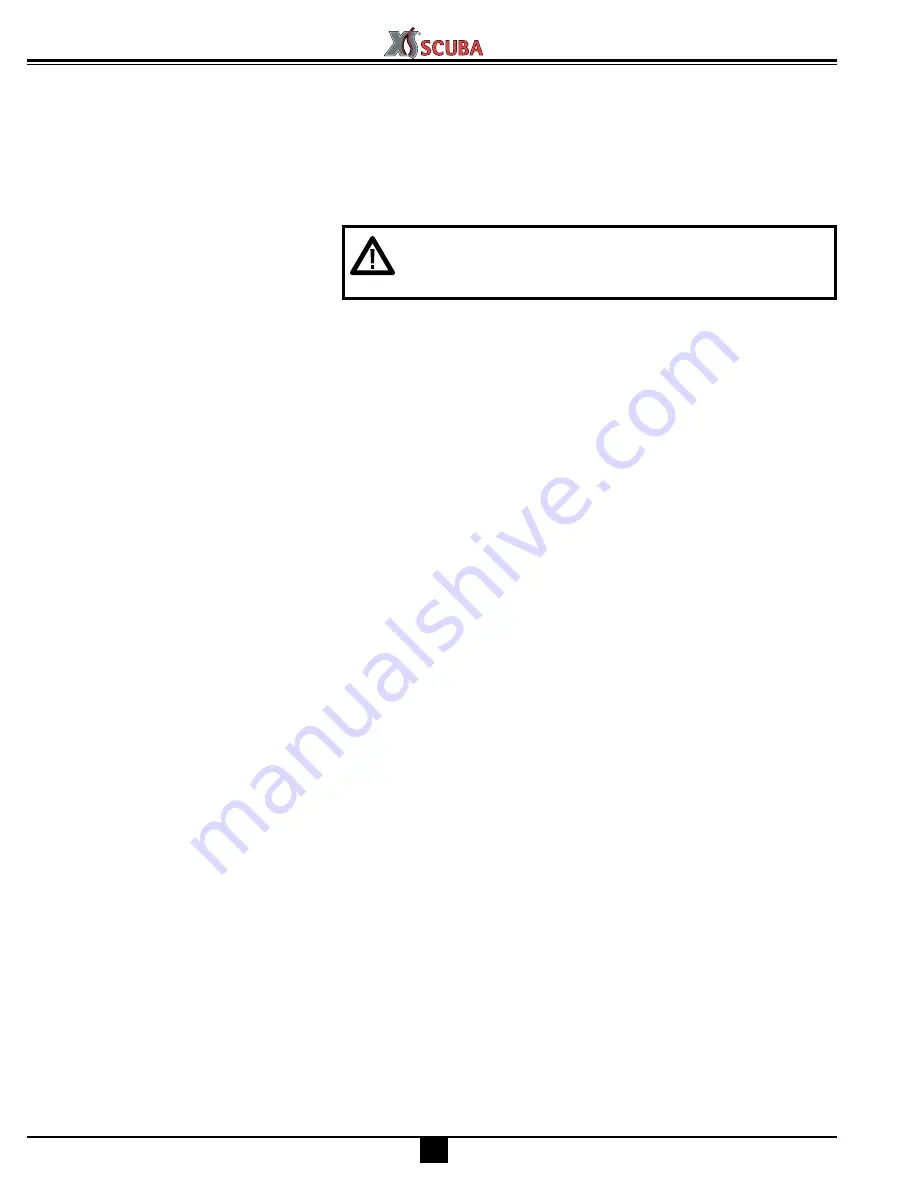
SeaAir Regulator
26
SeaAir Regulator Service and Repair Manual
each adjustment to listen, and be careful to avoid over-adjusting
beyond the point that the leak has stopped. When the leak has
stopped, purge the second stage again to ensure that it does not
return. Observe the IP Test Gauge while purging to verify that
it indicates a stable intermediate pressure after each cycle, with
no creep or fluctuation.
CAUTION
: Over-adjustment of the orifice can cause exces-
sive spring load in the second stage valve, and may impair
the regulator’s performance.
8. When the second stage is properly adjusted with no leaks or
lever slack, depressurize and purge the system to disconnect the
LP hose.
9. Reconnect the LP hose to the inlet coupling, and apply a torque
wrench with 17mm crow-foot to tighten the fitting to a torque
measurement of 55 inch-lbs (±5).
Subjective Breathing Test
1. While the regulator is connected to a cylinder containing 2,500
– 3,000 psi and pressurized, turn the second stage adjustment
knob completely out counterclockwise, and verify that a slight
leak of airflow is present.
2. Slowly turn the adjustment knob clockwise to verify that the
airflow stops between 2 -1 turn.
3. Turn the adjustment knob completely in clockwise to maximum
opening effort, and depress the purge to ensure that an adequate
volume of air flows through the mouthpiece, sufficient to clear
the second stage.
4. Turn the adjustment knob out counter-clockwise until a leak
can be heard, and then back just until the leak stops. Breathe
from the second stage.
• A properly serviced and adjusted regulator should deliver air
upon deep inhalation without excessive inhalation effort, free-
flow, or vibration. When exhaling, there should be no resistance
or sticking of the exhalation valve. If any of these problems oc-
cur, refer to the Troubleshooting Guide.
Flowbench Testing (optional)
The Subjective Breathing Test, combined with the Intermedi-
ate Pressure Test, will sufficiently verify the regulator's performance
in most circumstances. As an additional test, a Magnahelic flow-
bench can be used to verify the second stage opening effort, which
should not exceed 1.0 column inches H
2
O with the knob turned out
counter-clockwise, or 2.5 column inches H
2
O with the knob turned
completely in clockwise.
Содержание SEAAIR
Страница 1: ...Service Repair Manual SERVICE AND REPAIR MANUAL SEAAIR REGULATOR PN RG200 Revised 02 11...
Страница 30: ......
Страница 31: ......