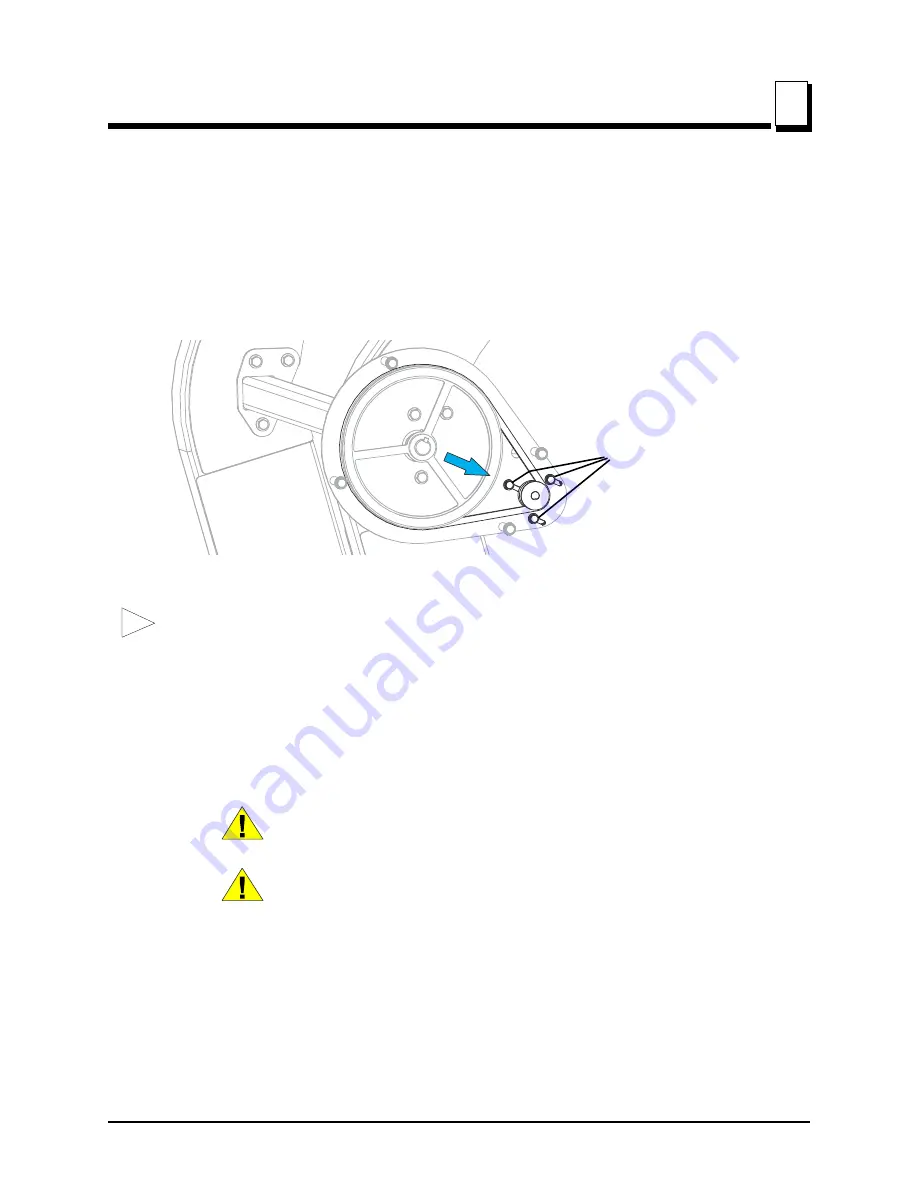
Maintenance
Power Feed
Maintenance
WMdoc072919
5-23
5
3.
Loosen the motor adjustment bolts.
4.
Tighten the belt to 1/8” (3 mm) deflection with a 7 lb. (3.2 Kg) deflection force.
5.
Retighten the motor bolts and replace the feed motor cover.
See Figure 5-18.
ADJUST THE POWER FEED CHAIN
1.
Move the saw head all the way toward the front (hitch end) of the mill.
2.
Use the two lock nuts at the rear of the mill to tighten or loosen the power feed chain.
3.
Check that the chains are evenly tensioned so that the sawhead moves square to the log
bed.
CAUTION!
Do not overtighten the feed chain. Damage to the power
feed motor may result.
CAUTION!
Do not tighten the chains unevenly. Damage to the sawmill
and uneven cutting may result.
FIG. 5-18
LX0001-05
Adjustment bolts
AR