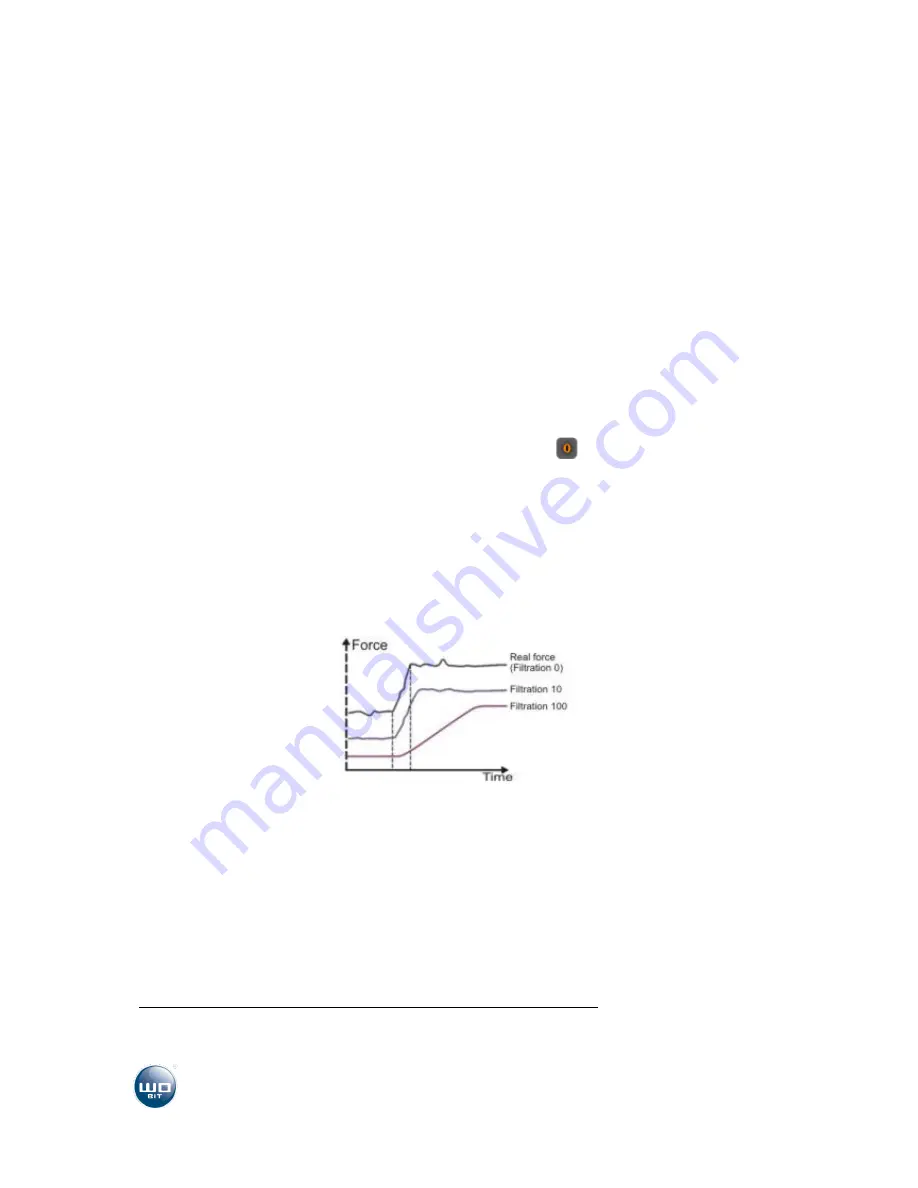
www.wobit.com.pl
User manual -ADT42 – 23.06.2015 – v.1.3
page 9
precision of measurement values (number of
decimals).
6)
Reading and recording of introduced parameters to
module, factory settings recall.
Input configuration for force sensors boils down to determine number of used channels (
1
) and
setting of parameters used for force sensors (
3
).
Parameters setting of connected force sensors
For force sensor should be introduced parameters as below:
Sensor range [N]
– rated load of used sensor in N, usually present on sensor’s housing.
Bridge constant [mV/V]
– sensitivity of used sensor in mV/V, usually present on sensor’s housing or
in its documentation. As a rule it is value from a range 1…2 mV/V.
Additionally for each input channel you can reverse measured signal (change sign from + for -) using
option „
Reverse the sign
” and zeroing channel by pressing „
Zero
”
.
Filtration of measurement
ADT42 has constant averaging filter set in range 0…99 samples and measurement mode „
Fast
” and
„
Slow
” (
2
).
Bigger value of filtration increases stability of measurements, but also causes slower response for
change of signals from sensor. Additionally setting of „slow” mode decreases measurement
frequency 8 times, but it improve its stability.
Picture. 5 Filtration influence on value of measurement.
Units of measurements
Units of measurements (
5
) determines in which units the module will present measurements (N –
Newton’s, g- gram, kg – kilogram, T – ton, F- pound). Also values available by MODBUS interface are
stored in set units. „
Precision
” tab set quantity of decimals indicated values in ADT42-PC program
and doesn’t influence on real accuracy of measurement.
3.2.1
Example of configuration
Example:
Two force sensors 1,5mV/V, with measuring range up to 500N.
1)
Setting of active inputs on „1 + 2” (
1
)