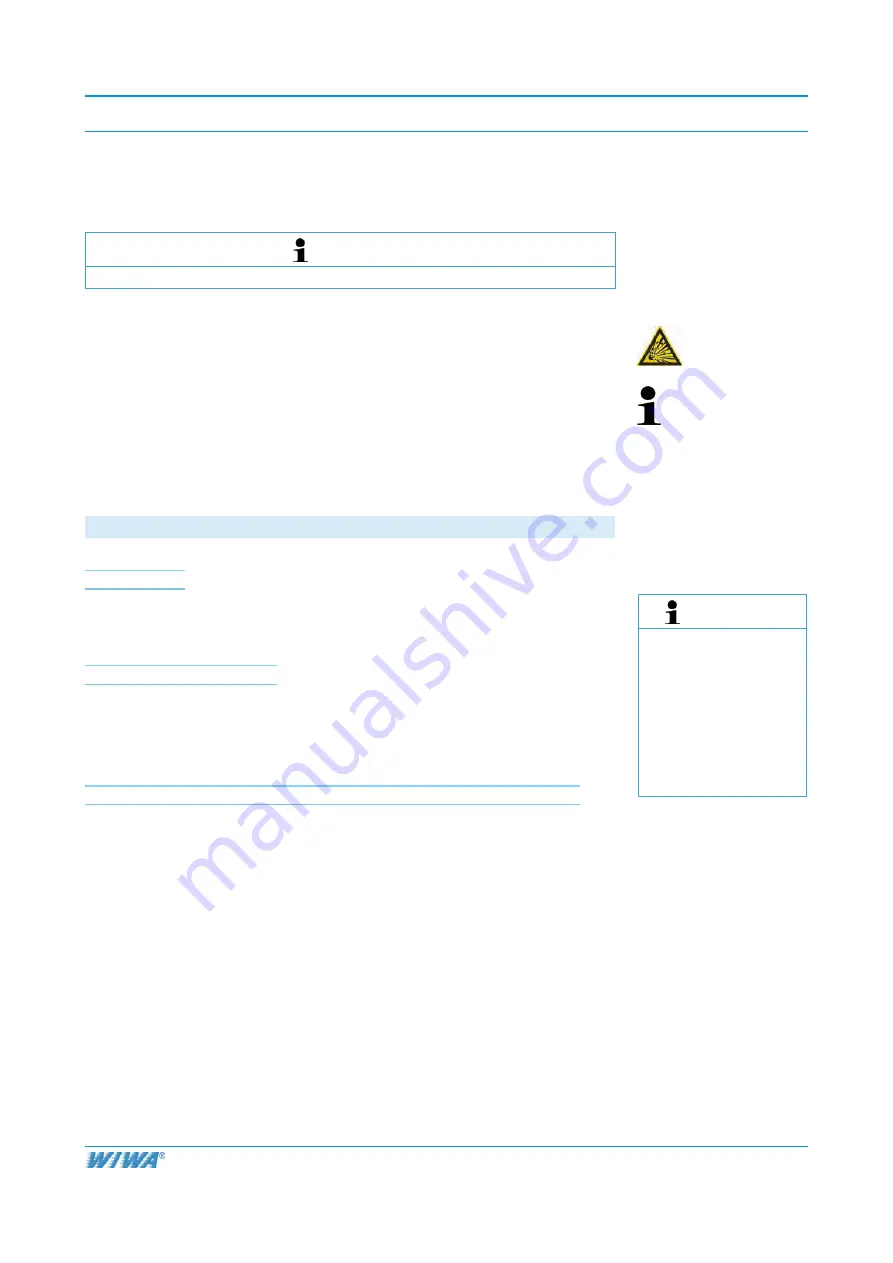
Operation
6
Translation of the original operation manual
33
33
•303_208176_1004_en•ski
6.2
Job commencement
CAUTION!
Apply the spray gun* safety catch if stopping work even for a few minutes.
Static charges can cause sparks which can itself cause fire and explosions.
Due to possible electrostatic charge, DO NOT use narrow neck cans or drums with bung-
holes. With metallic containers, take care that the spray gun* is constantly in contact with
the container wall.
Pressure values listed in this chapter are only
guideline values
and eventually have to
be adjusted according to the
viscosity of the material
or the
hose length being used
.
While working, observe if you have to adapt the pressure to get the desired result.
All position numbers found in this chapter apply to the specification in the chapter 3.6
“Component description”.
Task: Preparation for the spraying
Initial situation:
The unit is already set up and the job is restarted after a work interruption. The system is
filled with material up to the mixer (refer to chapter “Initial operation”).
Preparation of the flush pump
➤
Place the suction assembly of the flush pump into the thinner which belongs to the
material and set the air regulator (pos. 6.1) of the flush pump to 3 to 6 bar, depending
on the length of the material hoses.
Starting the equipment for material processing when not already in operation
➤
Fluid heaters (pos. 11):
➤
Restore the power connection.
➤
Set the designated temperature on the adjusting knob.
➤
Immension heater (pos. 12):
➤
Restore the power connection.
➤
Set the designated temperature on the adjusting knob.
➤
Agitator (pos. 8):
➤
Turn on the agitator.
➤
Adjust the desired speed on the regulator (pos. 8.1.
CAUTION!
The flush pump has to
be ready at all times
during the working
process.
At all times it must be
possible to flush com-
ponents, which were
contaminated by mixed
material, within
the
given pot life
!