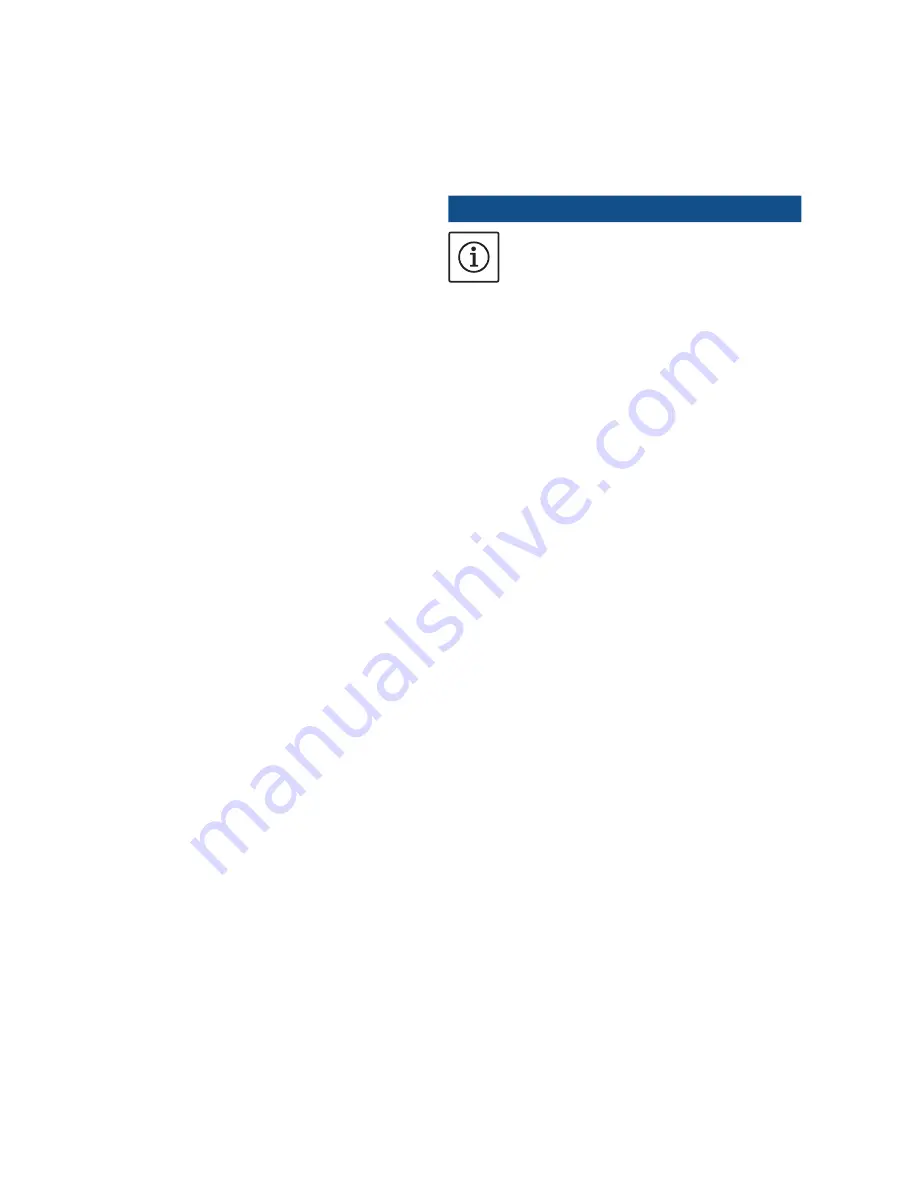
28
WILO SE 2015-07 V05 Letter
US English
MAINTENANCE AND REPAIR
smooth work on the pump. After working on the
pump, remove any used cleaning materials and tools
from the pump. Store all materials and tools in their
proper place.
• Operating materials should be collected in suitable
containers and disposed of properly. Always wear
appropriate protective clothing when performing
maintenance and repair work. This must also be
disposed of properly.
8.1. Operating materials
8.1.1. Overview of white oil
The sealing chamber is filled with white oil that is
potentially biodegradable.
When changing the oil, we recommend the follow-
ing oil types:
• Aral Autin PL*
• Shell ONDINA 919
• Esso MARCOL 52* or 82*
• BP WHITEMORE WOM 14*
• Texaco Pharmaceutical 30* or 40*
All oil types marked with “*” are approved for use
with foods in accordance with USDA-H1.
Filling quantities
The filling quantities depend on the motor:
•
Single-channel hydraulic systems (PRO C…):
•
P 13.1: 37 fl oz (1100 ml)
•
P 13.2: 37 fl oz (1100 ml)
•
P 17.1: 61 fl oz (1800 ml)
•
Vortex hydraulic systems (PRO V…):
•
P 13.1: 30 fl oz (900 ml)
•
P 13.2: 50 fl oz (1500 ml)
•
P 17.1: 61 fl oz (1800 ml)
8.1.2. Overview of grease
The following lubricating grease can be used in ac-
cordance with DIN 51818/NLGl Class 3:
• Esso Unirex N3
8.2. Maintenance intervals
To ensure reliable operation, various maintenance
tasks must be carried out regularly.
The maintenance intervals must be specified ac
-
cording to the load on the pump. Regardless of the
specified maintenance intervals, the pump or instal
-
lation must be checked if strong vibrations occur
during operation.
When used in sewage lifting units inside build-
ings or on areas of land, the maintenance inter-
vals and tasks should be in accordance with the
requirements of local directives. Please check the
requirements in your area!
8.2.1. Intervals for normal operating conditions
2 years
• Visual inspection of the power supply cable
• Visual inspection of accessories
• Visual inspection of the coating and housing for
wear
• Functional inspection of all safety and monitoring
devices
• Inspection of the switchgear/relays used
• Oil change
NOTE
If sealing chamber control is installed, the oil is
changed according to the indicator!
15000 operating hours or after 10 years at the
latest
• General overhaul
8.2.2. Intervals for harsh operating conditions
Under harsh operating conditions, the specified
maintenance intervals must be shortened accord-
ingly. In this case, please contact Wilo customer ser-
vice. If using the pump under harsh conditions, we
also recommend signing a maintenance contract.
Harsh operating conditions include:
•
A large proportion of fibrous material or sand in the
fluid
• Turbulent intake (e.g. due to air entry, cavitation)
•
Strongly corrosive fluids
•
Strongly gassing fluids
• Unfavorable duty points
• Operating states subject to water hammer
8.2.3. Recommended maintenance measures to ensure
smooth operation
We recommend regular inspections of the cur-
rent consumption and the operating voltage in all
3 phases. In normal operation, these values remain
constant. Slight fluctuations may occur depending
on the characteristics of the fluid. The current con
-
sumption can provide an early indication of damage
and/or malfunctions in the impeller, bearings, and/
or motor, which can be rectified. Large voltage
fluctuations strain the motor winding and can cause
the pump to break down. Regular inspections can
therefore largely prevent major secondary damage
and reduce the risk of total breakdown. We recom-
mend the use of remote monitoring for regular
inspections. Please contact Wilo customer service.
8.3. Maintenance work
Before carrying out maintenance work:
• Disconnect the pump from the power supply and
secure it against being switched on inadvertently.
• Allow the pump to cool down and clean it thor-
oughly.
• Make sure that all the operationally relevant parts
are in good condition.
Содержание Rexa PRO Series
Страница 5: ...Fig 9 1...