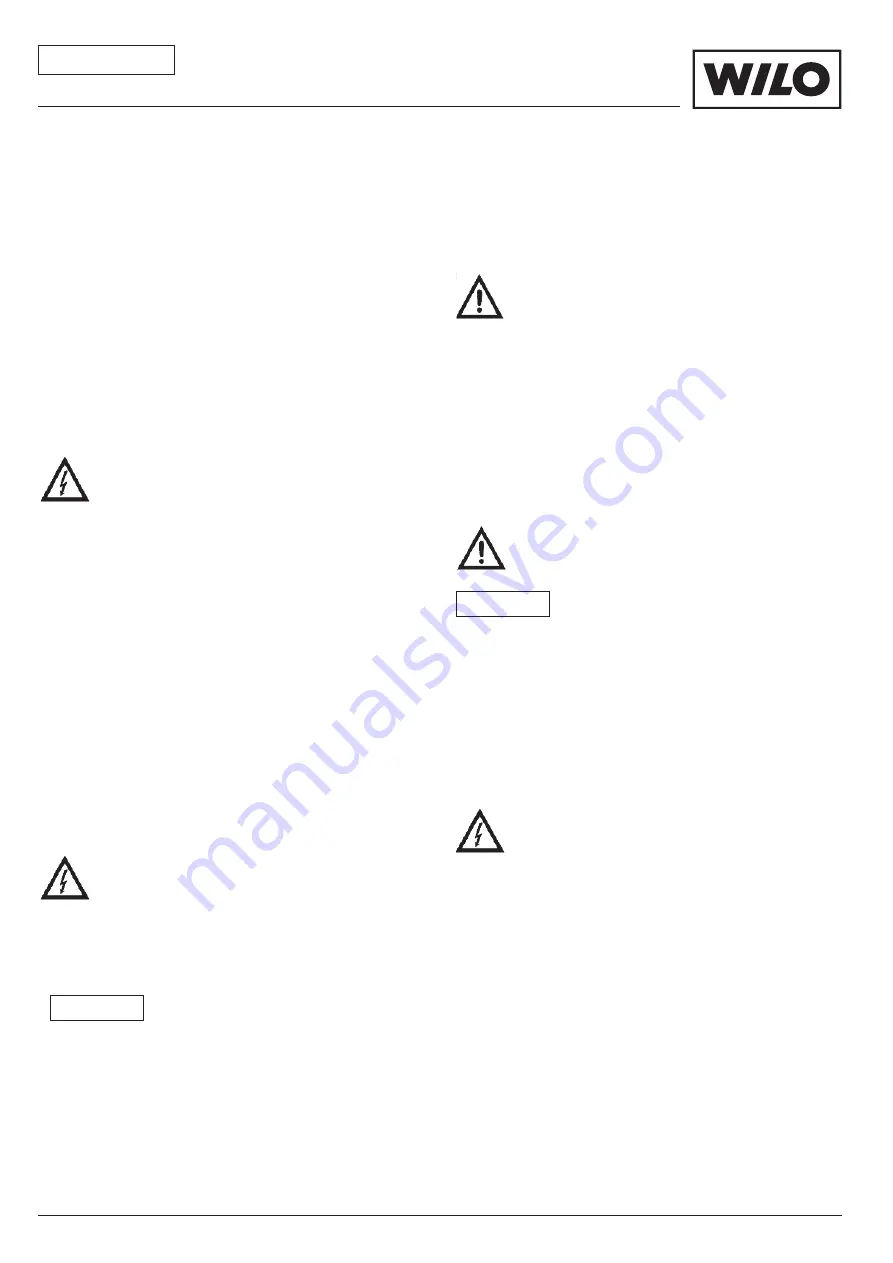
11
ENGLISH
suction port.
– Keep the delivery pipe in a vertical position on a height of at least 500
mm up to priming of the pump, when the suction head (SH) is higher
than 7 m.
– Isolating valves (1) should be installed in front of and behind the
pump, so that the pump can be easily changed and/or maintenance
work can be carried out more easily.
– A backflow preventer (2) should be installed immediately behind the
outlet pressure gland of the pump.
– The inlet and outlet pipes should be connected to the pump without
stress. Flexible lengths of pipe or bellow expansion joints of
restricted length can be used to ensure a low-vibration connection.
The weight of the pipework must be supported.
– The customer should take suitable measures to prevent low water
levels and hence guard against the pump running dry in order to
protect the axial face seal. The WILO range comprises various
accessories which can be used for this purpose.
– The customer should protect the pump at the inlet pipe with a
strainer (1 mm mesh) or filter connection (5) to avoid the pipe
being damaged by any dirt which may be sucked in.
5.2 Electrical installation
– Electrical work must be carried out by a qualified and
licensed electrician in strict compliance with local regu-
lations.
– The electricity supply must be connected via a rigid supply cable
fitted with a coupler or an all-pole switch with a contact gap of at least
3 mm in accordance with the local regulations in force (e.g. in
accordance with the latest edition of IEE wiring regulations).
– Check the mains current and voltage, against compliance with the
data on the pump rating plate.
– Pump/installation must be earthed in compliance with regulations.
– Mains fuse: 10A time-lag fuse.
– The customer should fit three phase current motors with a motor
safety switch which should be adjusted to the nominal current given
on the rating plate to prevent the motor from overheating.
Single phase motors are fitted with a thermal motor cut-out in the
factory. This cuts off the pump when the permissible temperature of
the motor coil is exceeded and switches it back on again
automatically once it has cooled down.
– A supply cable with an adequate ample external diameter (e.g. H 05
VV-F 3/4 G 1.5) should be used to protect against damp and to
secure the mains lead cleat of the PG-nut.
– Connection to the mains must be carried out in accordance with the
plan of terminal connections for three phase or single phase current
in the terminal box of the pump (see also Fig. 5).
– The supply cable must be laid in such a way that it never touches the
pipework and/or the pump and motor casing.
If necessary a fault current breaker (FI-switch) should be
provided.
6. Commissioning
– Check that there is a sufficient level of water in the reservoir and/or
check the inlet pressure.
The pump must not run dry, as this would destroy
the axial face seal.
– Only for three phase current motors: – Adjust the motor cut-out to
the nominal current given
on the rating plate.
– Checking direction of rota-
tion: Check that the pump
rotates in the direction indi-
cated by the arrow on the
pump casing by switching
on for a short time. If this is
not the case, interchange
2 phases in the pump
WARNING !
terminal box.
– If available, position float switches or electrodes for protection against
low water levels in such a way that the pump cuts out if the water
level is so low that air would begin to be sucked in.
Installation under pressure-operation (Fig. 2) :
– Close the discharge valve
– Unscrew the filling plug ( Pos. 3)
– Progressively open the suction valve to completely fill the pump untill
water flows out and complete aeration.
– Depending on the fluid temperature and the system pres-
sure, if the vent screw is completely loosened hot liquid or
gas can escape or even shoot out at high pressure.
Beware of scalding.
– Screw again the filling plug
– Open the discharge valve
– Switch on the pump.
Installation in suction-operation (Fig. 3) :
– Be sure that all accessories connected to the pump delivery are
opened (cocks, valves...).
– Open the discharge valve
– Open the suction valve
– Unscrew the draining plug (Pos. 3) on the pump casing
– Put a funnel into the port and completely fill the pump
– Screw the plug back in
– Switch on the pump.
– Depending on the operating conditions of the pump or
installation (fluid temperature), the entire pump may be-
come very hot.
Avoid touching the pipe owing to the risk of burning.
The pump must not run for longer than 10 minutes
with a flow rate of Q = 0 m
3
/h (clodes discharge
valve).
– To ensure a minimum flow of about or higher than 10 % of the
nominal flow of the pump to avoid the formation of a vapour lock at
the top of the pump.
– Check that the current input does not exceed the valve indicated on
the motor data plate.
7. Maintenance
– Before carrying out any maintenance work, switch off the
pump and ensure that it cannot be switched on again by
unauthorized people. Never carry out work on a running
pump.
– The pump is almost maintenance free.
The Life expactancy will differ dependent on the operating conditions.
We recommend a 1/2 yearly visual control for leakage and out of
ordanary vibration.
– During the running-in period, there may be some dripping from the
axial face seal. Should a more significant leak occur as a result of
substantial wear, have the axial face seal replaced by a specialist.
– Increased bearing noise and unusual vibrations indicate a worn
bearing. In this case, have the bearing replaced by a specialist.
– When the pump is exposed to frost or is out of service for a long
period, the pump and pipework must be emptied in the cold
season. Empty the pump by releasing the drain valve (Figs 1, 2, 3,
Pos. 4), the inlet pipe by releasing the vent screw, and the outlet pipe
by opening the bleeding point. Don’t forget to open the non-return
valve of the foot-valve.
WARNING !
Содержание MultiCargo MC
Страница 2: ...Fig 1 Fig 2 Fig 3 1 4 8 7 5 3 6 2 9 2 ...
Страница 3: ...3 Fig 4 Y HIGH VOLTAGE LOW 3 1 1 Fig 5 ...
Страница 25: ......
Страница 26: ......