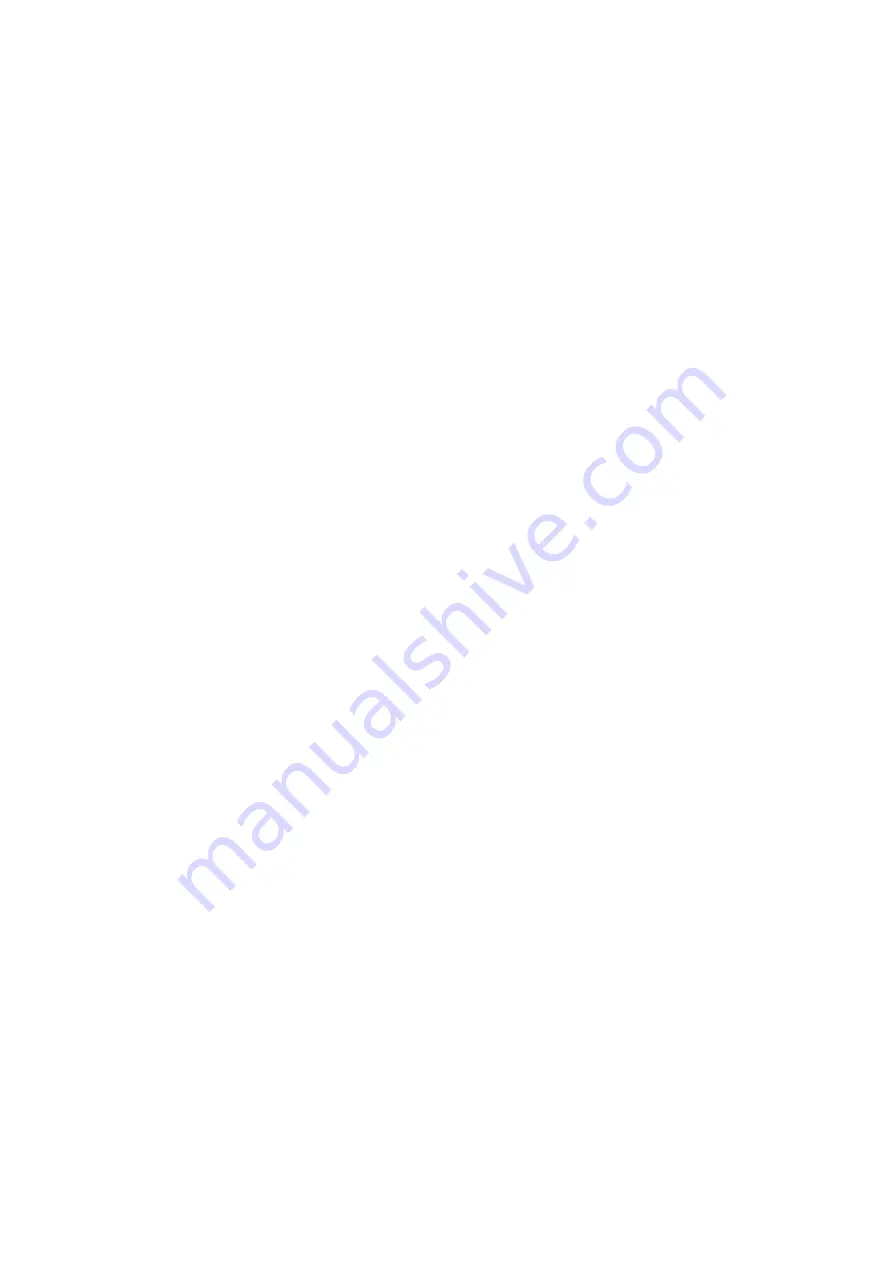
36
ENGINE POUNDS
An engine pound is a decided knock or thump usually caused by a loose or worn part. Do not confuse the
terms "vibration" and "pound." An engine can pound and still pull smoothly, or an engine can vibrate when all its
moving parts are properly adjusted and well lubricated.
A loose or worn main bearing pound is usually a heavy thump and the best way to determine which bearing
it is to make an examination. Sometimes if it is the low-pressure main bearing the pound is heavier when engine is
pulling simple. Often times it can be remedied by inserting over-sized balls. The bolts, which hold he main bearing
caps, may become loose allowing the whole main bearing to move up and down. When looking for a main bearing
pound these bolts should all be tested.
A loose connecting rod is one where the bolts have become loose or the bearing surface has become worn. A
connecting rod pound is a double pound most noticeable when the pulling is slow and heavy. Running along at a
steady rate of speed, it is usually decreased or sometimes eliminated by hooking up the reverse lever.
If a piston head is loose on the piston rod the result is a heavy double pound. If the piston rod is loose where
it screws into the crosshead the pound will be much lighter and sharper. It is a double pound and is heaviest at slow
speed. The later condition may be easily determined by trying piston rod lock nuts with a wrench. A double pound is
one, which thumps at each end of the piston stroke.
If the lock nuts, which hold the pumps on the bracket, are not tightened sufficiently or should become loose
the result will be a pound which should be looked after immediately. If allowed to continue the motion of the pumps
may strip the threads necessitating the replacement of a casting. To diagnose this pound notice that it occurs only
when the pressure is below the bypass point and when the pumps are pumping against the pressure of the generator.
Above by-pass point it ceases. An easy way is to raise the hood and take a look at the pumps. Any movement up and
down can easily be seen,
In the Models G and K it happens sometimes that in starting the engine too quickly the condenser pump
rocker arm is bent. This is due to the fact that the condenser is overloaded, with water from cylinder condensation,
and the pump is doing full work. As the air pump plunger is a part of the condenser pump plunger any shifting
upward of the rocker arm will raise the air pump plunger enough to cause it to strike the top of the air pump cylinder.
This pound is a single pound and is very dull and heavy. Sometimes it can be felt by placing the fingers on top of the
air pump. Also it may decrease or be eliminated when the air pump is pumping air to the tank, as also might a low
pressure main bearing pound. If the arm is not bent too much it can be remedied by putting a gasket under the air
pump head of such a thickness as to raise it enough that the plunger will not strike it.
In the Models E, F, H, and L the condenser pump may become loose in the crankcase. Any movement of the
condenser pump can be detected by the eye. It might be well to test the pin to see if it is tight in the crosshead.
If the engine frame bolts are loose enough the result might cause the engine to pound, as it lifts up and down
on the frame. While this was mentioned under vibration an extreme case might be classed as an engine pound.
Sometimes this can be detected by watching the joints where the engine arm seats on the frame when the engine is
running idle, or by feeling it with the end of the finger.
BROKEN CRANK SHAFT
This condition is more apt to happen on the engines, which have the foot brake on the flywheel. It is usually
brought about by applying the brake too fiercely, or without closing the throttle. It can be detected sometimes by the
fact that the flywheel wobbles and does not run true. The surest way is to remove the crankcase and test by holding
the flywheel and moving the crank.
ENGINE KICKS UPON CLOSING THROTTLE
Should the engine jerk the drive shaft for a few revolutions after closing the throttle and car is coasting it is
caused by the throttle seat leaking steam and thereby not completely shutting it off. This steam is not sufficient to
keep the engine running faster than the car. First the car over-takes the engine and then the engine over-takes the car
alternately, taking up the slack on the drive shaft and loosening it again. Remove the throttle and grind seat with
pumice stone or powdered glass. To test for leaky throttle allow engine to remain stationary a few moments, then