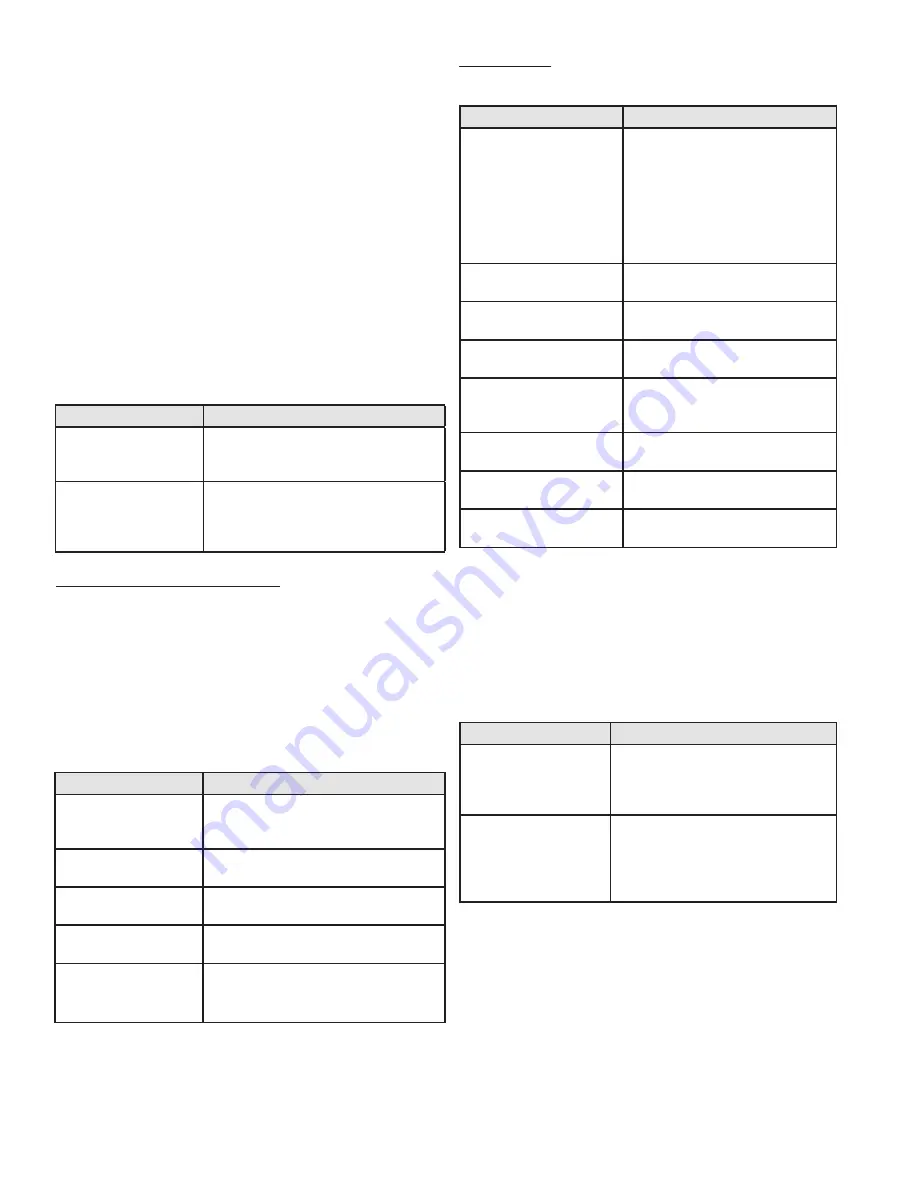
WHL-038 Rev. 1.29.16
44
3. Next, check the boiler settings. Adjustment and factory
defaults are outlined within this section. If a cascade system is
used, it is important that all the boilers have the same boiler
settings.
4. Next, check the system settings. Adjustments and factory
defaults are outlined within this section. If a cascade system is
used, it is important that the Master Boiler is programmed with
the correct system settings.
5. Create a demand on the boiler or boilers if a cascade system
is used. The user can monitor system functions when the boilers
are operational.
6. If the boilers fail to start, refer to the troubleshooting section
in the back of this manual.
D. Programming Boiler Settings
Boiler Setting Program Access
Note: Programming the boiler control is not possible when the
boiler is firing. Make sure any input which can create a demand
on the boiler, such as the tank thermostat, is turned off, so the
boiler will remain idle to allow programming.
Screen
Description
ENTER MENU CODE
000
To access the boiler setting program,
press and hold
ENTER
for 4 seconds until
the display shows the screen at left.
ENTER MENU CODE
600
Use the arrow keys to log in the
Boiler
Menu Access Code - 600
. Press
ENTER
to confirm the code and access the
Boiler
Setting Program
navigation menu.
Table 12 - Boiler Setting Access
Boiler Setting Program Navigation
Once the code is confirmed, the user can start to set the
Boiler
Settings
. Use the arrow keys on the display to navigate through
the
Boiler Settings
. A blinking setting indicates the setting can
be changed. To change a setting, press
ENTER
. Boiler settings
can be increased by pressing
^
and decreased by pressing
v
on
the display. When done, press
ENTER
. The setting will stop
blinking and the user can move on to next setting by pressing
the
<
or
>
arrow keys. Press
RESET
to exit programming and
store settings. Listed below are the boiler settings that can be
programmed into the control.
Screen
Description
CENTRAL HEAT
180
o
F
Allows the user to adjust the boiler set
point from 50F to 190
o
F (Factory Default
180
o
F).
CENTRAL DIFF SET
30
o
F
Adjusts the boiler differential set point
from 5
o
F to 30
o
F (Factory Default 30
o
F).
DHW SETPOINT
119
o
F
Adjusts the indirect tank set point from
70
o
F to 185
o
F (Factory Default 119
o
F).
DHW DIFF SETPOINT
7
o
F
Adjusts the DHW differential set point
from 1
o
F to 30
o
F (Factory Default 7
o
F).
TEMP DISPLAY C OR F
o
F
Adjusts
the
temperature
measurement in F = Fahrenheit to C =
Celsius (Default is Fahrenheit).
Table 15 - Boiler Setting Program Navigation
Clock Settings
(
NOTE:
The clock will reset if the boiler is powered off for
more than a week.)
Screen
Description
CLOCK MODE (12/24)
08/28/2009 Fr 9:42A
Changes the clock from 12 hour
mode (8:45 PM) to 24 hour mode
(20:45). To change to 24 hour mode,
press
ENTER
. The letter (A or P)
after the time will blink. Press the
up or down arrow key once and the
letter will disappear. Press
ENTER
to
save the new setting.
CLOCK HOUR
08/28/2009 Fr 10:01A
Allows the user to adjust the hour
setting.
CLOCK MINUTE
08/28/2009 Fr 10:01A
Adjusts the minute setting.
CLOCK DAY OF WEEK
08/28/2009 Fr 10:01A
Adjusts the day of the week.
CLOCK DATE MODE
08/28/2009 Fr 10:01A
Allows the user to switch to
European date format (2009/08/28)
from US format (08/28/2009).
CLOCK YEAR
08/28/2009 Fr 10:01A
Adjusts the year setting.
CLOCK MONTH
08/28/2009 Fr 10:01A
Adjusts the month setting.
CLOCK DATE
08/28/2009 Fr 10:01A
The clock is set.
Table 13 - Clock Setting Screens
NOTE:
The internal clock does not adjust for daylight savings
time and requires manual adjustment.
E. Programming the System Setting
System Setting Program Access
Note: Programming the boiler control is not possible when
the boiler is firing. Make sure any input which can create a
demand on the boiler, such as the tank thermostat, is turned
off, so the boiler will remain idle to allow programming.
Screen
Description
ENTER MENU CODE
000
To access the boiler setting program,
press and hold
ENTER
for 4 seconds
until the display shows the screen at
left.
ENTER MENU CODE
925
Use the arrow keys to log in the
Boiler
Menu Access Code - 925
. Press
ENTER
to confirm the code and access the
System Setting Program
navigation
menu.
Table 14 - System Setting Access
F. System Setting Program Navigation
Once the
System Menu Access Code
is confirmed, the user
can begin to set the system setting menu. Use the
< >
keys
on the display to navigate through the System Settings.
To change a setting, press
ENTER
. System settings can be
increased
by pressing
^
and
decreased
by pressing
v
on
the display. When done, press
ENTER
. The setting will stop
blinking and you can move on to next setting. Press
RESET
to exit programming and store settings. Listed below are the
boiler settings that can be programmed into the control.
Содержание WBCETNG1000
Страница 14: ...WHL 038 Rev 1 29 16 14 Figure 6 Specifications and Dimensions NOTE All Dimensions Are Approximate ...
Страница 35: ...WHL 038 Rev 1 29 16 35 Figure 24 CascadeTermination Plug Detail Figure 25 Cascade Master and FollowerWiring ...
Страница 36: ...WHL 038 Rev 1 29 16 36 Figure 26 Internal Connection Diagram ...
Страница 65: ...WHL 038 Rev 1 29 16 65 Figure 44 Exterior Replacement Parts ...
Страница 66: ...WHL 038 Rev 1 29 16 66 Table 27 Optional Jacket Replacement Parts Part 15 Installing the Optional Jacket ...
Страница 73: ...WHL 038 Rev 1 29 16 73 Maintenance Notes ...