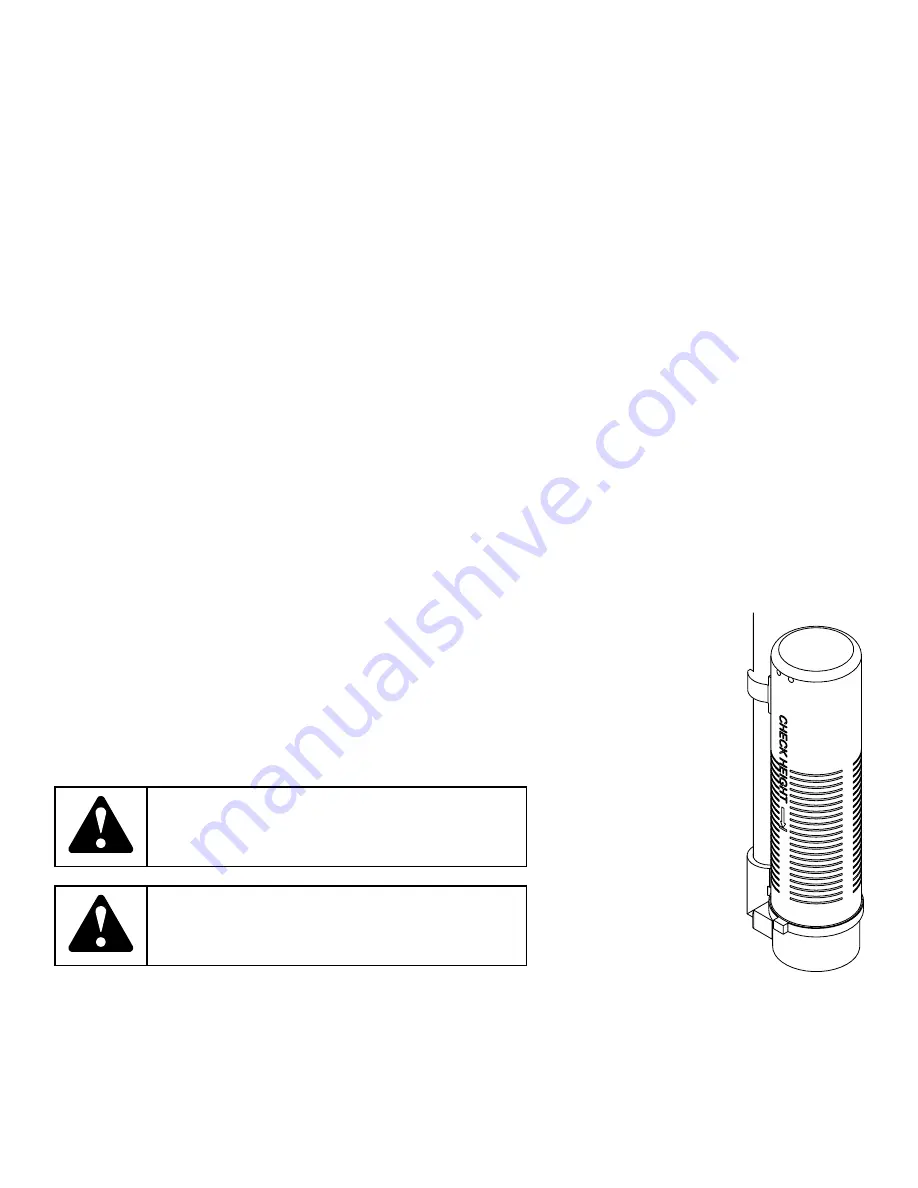
4
Installation Instructions 6200SXT Upflow
WATER PRESSURE:
A minimum of 20 psi (1.4 bar) of water pressure is required for regeneration valve to operate effectively.
ELECTRICAL FACILITIES:
An uninterrupted alternating current (A/C) supply is required. Note: Other voltages are available.
Please make sure your voltage supply is compatible with your unit before installation.
EXISTING PLUMBING:
Condition of existing plumbing should be free from lime and iron buildup. Piping that is built up heavily
with lime and/or iron should be replaced. If piping is clogged with iron, a separate iron filter unit should be installed ahead
of the water softener.
LOCATION OF SOFTENER AND DRAIN:
The softener should be located close to a drain to prevent air breaks and back flow.
BY-PASS VALVES: Always provide for the installation of a by-pass valve if unit is not equipped with one.
CAUTION:
Water pressure is not to exceed 125 psi (8.6 bar), water temperature is not to exceed 110°F (43°C), and the unit
cannot be subjected to freezing conditions.
Installation Instructions
1. Place the softener tank where you want to install the unit making sure the unit is level and on a firm base.
2. During cold weather, the installer should warm the valve to room temperature before operating.
3. All plumbing should be done in accordance with local plumbing codes. The pipe size for residential drain line should be
a minimum of 1/2” (13 mm). Backwash flow rates in excess of 7 gpm (26.5 Lpm) or length in excess of 20’ (6 m) require
3/4” (19 mm) drain line. Commercial drain lines should be the same size as the drain line flow control.
4. Cut the distributor tube 1.88” (4.7 cm) below the top of the tank.
5. Lubricate the distributor O-ring seal and tank O-ring seal. Place the main control valve on tank. Note: Only use silicone
lubricant.
6. Solder joints near the drain must be done prior to connecting the Drain Line Flow Control fitting (DLFC). Leave at least
6” (15 cm) between the DLFC and solder joints when soldering pipes that are connected on the DLFC. Failure to do this
could cause interior damage to the DLFC.
7. Teflon tape is the only sealant to be used on the drain fitting. The drain from twin tank units may be run through a
common line.
8. Make sure that the floor is clean beneath the salt storage tank and that it is level.
9. Place approximately 1” (25 mm) of water above the grid plate. If a grid is not utilized, fill to the top of the air check
(Figure 1) in the salt tank. Do not add salt to the brine tank at this time.
10. On units with a by-pass, place in by-pass position. Turn on the main water supply. Open a cold soft
water tap nearby and let run a few minutes or until the system is free from foreign material (usually
solder) that may have resulted from the installation. Once clean, close the water tap.
11. Slowly place the by-pass in service position and let water flow into the mineral tank. When water
flow stops, slowly open a cold water tap nearby and let run until the air is purged from the unit.
12. Plug unit into an electrical outlet. Note: All electrical connections must be connected according
to local codes. Be certain the outlet is uninterrupted.
CAUTION
• Do not exceed 125 psi water pressure
• Do not exceed 110°F (43°C) water temperature
• Do not subject unit to freezing conditions
WARNING
The system MUST be depressurized before removing any
connections for servicing.
Содержание 6200 SXT
Страница 1: ...6200 SXT Upflow Control Valve for Water Conditioning and Treatment Purposes Service Manual...
Страница 21: ...Wiring Diagram 21...
Страница 22: ...6200SXT Upflow Brining Rates 22 6200SXT Upflow Brining Rates with Water 20 PSI Regulated Cap...
Страница 29: ...29 6200 SXT Valve Dimensional Drawings All dimensions are in Inches mm...
Страница 35: ...35...