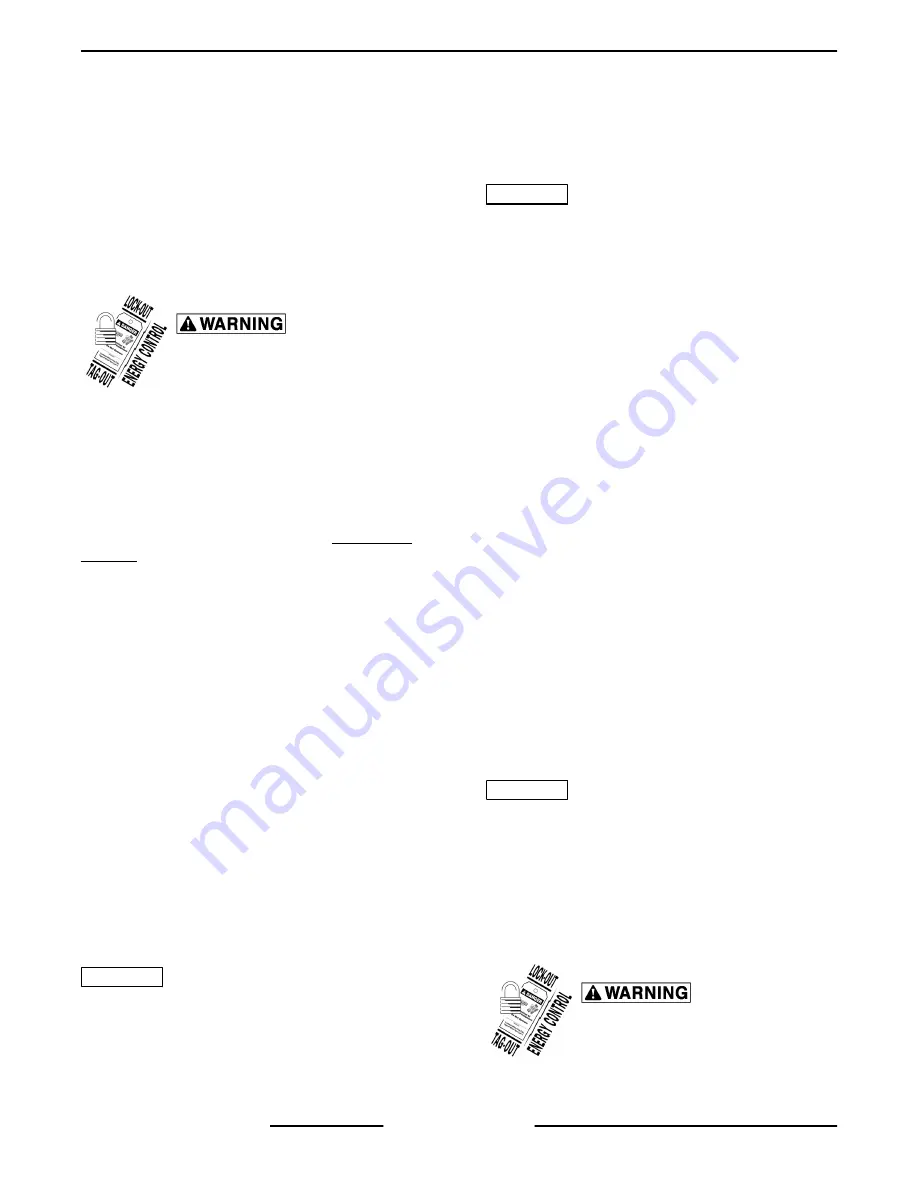
NOTE:
If water is in the boiler but is not being detected
by the water level probes, the probes may need
cleaned and/or boiler delimed.
4.
After checking the above items, if the water level
control board does not appear to be functioning
as outlined, then:
A.
Replace the water level control board.
B.
Check unit for proper operation.
Electro Mechanical Controls
Disconnect the
electrical power to the machine and
follow lockout / tagout procedures.
Loose electrical connections may prevent the heat
from coming on or may cause the boiler to overfill.
Accumulation of boiler scale on or near the sensing
probes may cause them to retain water on the
insulator surface. This may prevent the boiler from
filling or cause dry firing. Dry firing will result in damage
to heating elements or to the boiler. Verify the water
level controls operation as outlined in Water Level
Controls.
With the individual probe lead wire removed, check
the probes and contactors as outlined below:
1.
With an ohmmeter, check the probe between the
wire connection and shell. An open circuit should
be present when the boiler is empty. If resistance
is present, remove and clean the probes. Also
check for a cracked insulator, then reinstall
probes and check. When the boiler is full of water,
a resistance reading should be measurable
between the probes and shell only.
NOTE:
Actual resistance reading will depend on
water quality and probe condition.
2.
Check low level and differential water level
controls. With the power switch ON, use a
voltmeter to check the input voltage across
terminals 1 and 2. Meter should read 115V. With
the boiler empty, across terminals 9 and 10,
meter should read 300 to 350V. If these voltages
are not present, the coil is bad and the contactor
should be replaced.
CAUTION
Be careful to note the location of each
probe and the number of the wire connected to it.
Incorrectly connected wires will cause the controls to
malfunction.
3.
Remove the sensing probe as follows:
A.
Remove the bolted cover over the sensor
cluster.
B.
Disconnect the wire from the probe.
C.
Use a wrench to unthread the probe.
CAUTION
Do not use an abrasive on the insulator
or damage may occur.
4.
Clean probe thoroughly with a soft cloth. Make
sure to remove ALL deposits from the insulator.
5.
Inspect through the probe socket for the
presence of water. Water must drain from the
probe housing. If in doubt, pour water into the
housing and observe that it drains quickly. If the
housing fails to drain, remove the housing or
housing cover and clean the interior
mechanically.
WATER LEVEL GAUGE ASSEMBLY
1.
Remove the water level gauge assembly glass
tube as follow:
A.
Close the valves at the top and at the bottom
of the gauge assembly.
B.
Unscrew the packing nuts at the top and
bottom of the glass tube.
C.
Slide the glass tube upwards, until the
bottom of the tube is clear of the fitting.
D.
Lift the glass tube out of the fitting.
2.
Install the water level gauge assembly glass tube
as follow:
A.
Place new sealing washers on both ends of
the glass tube.
B.
Place the glass tube in the lower fitting and
slide up into the upper fitting.
CAUTION
Do not over tighten the packing nuts; it
could break the gauge glass.
C.
Tighten the packing nuts hand tight.
D.
Open the valves at the top and at the bottom
of the gauge assembly.
PRESSURE SWITCHES
Gas and electric models incorporate pressure
switches to control steamer operation.
Disconnect the
electrical power to the machine and
follow lockout / tagout procedures.
NOTE:
The pressure switch on the left is the cycling
or primary control; the one on the right is the high limit
VSX BOILER BASE SERIES CONVECTION STEAMERS - SERVICE PROCEDURES
F24627 (0916)
Page 16 of 82
Содержание ML-52163
Страница 46: ...Sheet 2 VSX BOILER BASE SERIES CONVECTION STEAMERS ELECTRICAL OPERATION F24627 0916 Page 46 of 82...
Страница 48: ...Sheet 2 VSX BOILER BASE SERIES CONVECTION STEAMERS ELECTRICAL OPERATION F24627 0916 Page 48 of 82...
Страница 50: ...Sheet 2 VSX BOILER BASE SERIES CONVECTION STEAMERS ELECTRICAL OPERATION F24627 0916 Page 50 of 82...
Страница 52: ...Sheet 2 VSX BOILER BASE SERIES CONVECTION STEAMERS ELECTRICAL OPERATION F24627 0916 Page 52 of 82...
Страница 54: ...Sheet 2 VSX BOILER BASE SERIES CONVECTION STEAMERS ELECTRICAL OPERATION F24627 0916 Page 54 of 82...
Страница 60: ...Sheet 2 VSX BOILER BASE SERIES CONVECTION STEAMERS ELECTRICAL OPERATION F24627 0916 Page 60 of 82...
Страница 62: ...Sheet 2 VSX BOILER BASE SERIES CONVECTION STEAMERS ELECTRICAL OPERATION F24627 0916 Page 62 of 82...
Страница 64: ...Sheet 2 VSX BOILER BASE SERIES CONVECTION STEAMERS ELECTRICAL OPERATION F24627 0916 Page 64 of 82...
Страница 66: ...Sheet 2 VSX BOILER BASE SERIES CONVECTION STEAMERS ELECTRICAL OPERATION F24627 0916 Page 66 of 82...
Страница 68: ...Sheet 2 VSX BOILER BASE SERIES CONVECTION STEAMERS ELECTRICAL OPERATION F24627 0916 Page 68 of 82...
Страница 70: ...Sheet 2 VSX BOILER BASE SERIES CONVECTION STEAMERS ELECTRICAL OPERATION F24627 0916 Page 70 of 82...
Страница 76: ...AUTO BLOWDOWN Fig 62 VSX BOILER BASE SERIES CONVECTION STEAMERS ELECTRICAL OPERATION F24627 0916 Page 76 of 82...