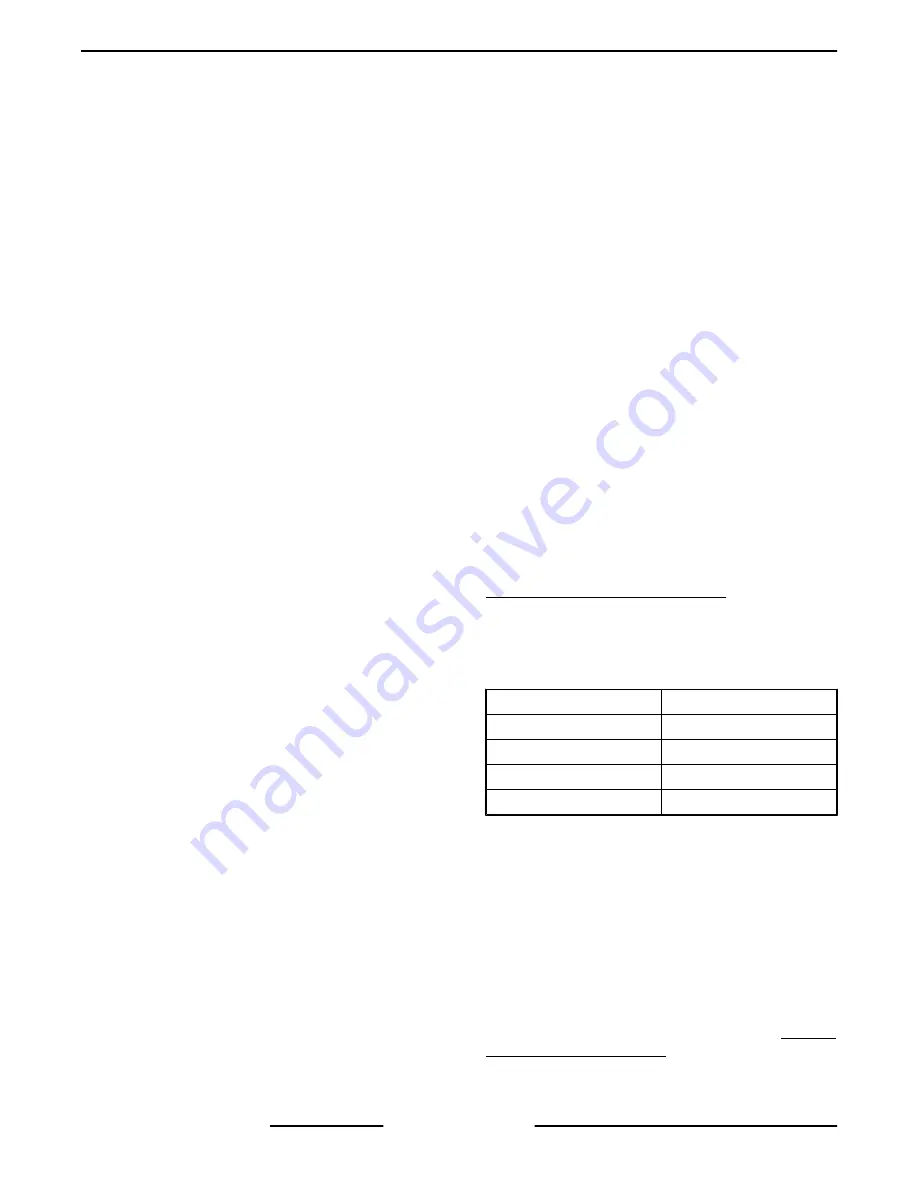
•
They will shut off the heat source to the boiler if
the water level drops too low.
NOTE:
Controls may not function and serious
clogging will occur if a daily blowdown procedure is
not followed.
The water level control works by using three different
probe lengths to monitor the water level. The probes
are:
•
High Level (HL)
•
Low Level (LL)
•
Low Level Cut Off (LLCO)
The level sensing probes may easily be removed to
inspect for lime build up. As a rule, the condition of
these devices will indicate the overall water condition
of the boiler. Clean the probes if needed.
Boiler Fill Solenoid Valve.
The valve admits water to
the boiler when demanded by the water level control
to maintain the correct water level in the boiler.
Cold Water Condenser Solenoid Valve.
The valve
allows cold water flow into the boiler blowdown drain
box to condense steam and cool the hot water before
its discharge into the drain.
Cycling Pressure Switch.
The switch controls boiler
pressure between prescribed limits by turning the heat
source on and off.
High Limit Pressure Switch.
The switch is physically
identical to the cycling pressure switch but is used as
a high limit. The pressure settings are at higher and
lower limits than the cycling pressure switch in order
to turn off the heat source before the boiler pressure
reaches its limit and automatically resets after the
pressure drops below the lower limit set point.
Blowdown/Drain Solenoid Valve.
The valve is
plumbed into the drain pipe of the boiler.
•
Newer steamer models will automatically
blowdown when power is turned off by using a
normally open solenoid valve.
•
Older models can have a solenoid valve that is
activated by depressing a separate blowdown
timer button or have a manual “ball” type valve.
Daily boiler blowdown is essential to proper operation
and component life by removing sediment and
scalants that may be lodged in the chamber of the
boiler.
NOTE:
On models using a direct steam supply, a
strainer is used in the pressure regulating valve.
Strainers.
A strainer is used in the water inlet line to
prevent foreign matter from becoming lodged in the fill
or cold water condenser solenoid valves and to keep
unwanted particles out of the system. A "Y" strainer
should be inserted upstream of the fill solenoid valve.
Power Switch.
When the switch is turned ON, power
is supplied to the controls and the steam generating
process is started in the boiler. The power switch is
located on the front of the boiler control box.
Water Inlet Valve.
The valve is used to stop water flow
to the steamer when the steamer is being serviced.
This valve should remain open during normal
operation.
•
Newer models will have a small Petcock type
valve.
•
Older models will be a “ball” type valve.
High Limit Thermostat.
This is a protective device
that shuts off the heat source if the boiler temperature
exceeds a specified limit. All standard models are
equipped with a surface high limit thermostat.
Descaler.
The descaler hangs submerged in water
inside the boiler and is used to help control boiler
surface scaling. Two descalers are used in each
boiler.
Handhole Cover Assembly.
This cover, when
unbolted and removed, allows internal examination /
cleaning of boiler shell and its components.See
BOILER INSPECTION / CLEANING for additional
information.
Pressure Gauge.
This gauge indicates boiler steam
pressure. Normal operating pressures are listed
below.
Steamer Type
PSI
Gas
8-10
Electric
11-13
Direct
10-12
Regenerated
10-12
Drain.
This component drains steam condensate and
water from cooking compartments and boiler.
Check Valve.
On models with the delime piping
assembly option, the check valve prevents the
ejection of hot water and steam out of the delime
funnel if the manual delime fill valve were to be
opened.
Delime Port Assembly.
On models with the delime
piping assembly option, this assemly allows the boiler
and other internal components to easily be delimed to
remove calcium, lime and rust build up. See BOILER
INSPECTION / CLEANING for additional information.
Standing Pilot (Gas Boilers).
The pilot should
always remain lit to light the main burners upon a call
VSX BOILER BASE SERIES CONVECTION STEAMERS - COMPONENT FUNCTION AND LOCATION
F24627 (0916)
Page 12 of 82
Содержание ML-52163
Страница 46: ...Sheet 2 VSX BOILER BASE SERIES CONVECTION STEAMERS ELECTRICAL OPERATION F24627 0916 Page 46 of 82...
Страница 48: ...Sheet 2 VSX BOILER BASE SERIES CONVECTION STEAMERS ELECTRICAL OPERATION F24627 0916 Page 48 of 82...
Страница 50: ...Sheet 2 VSX BOILER BASE SERIES CONVECTION STEAMERS ELECTRICAL OPERATION F24627 0916 Page 50 of 82...
Страница 52: ...Sheet 2 VSX BOILER BASE SERIES CONVECTION STEAMERS ELECTRICAL OPERATION F24627 0916 Page 52 of 82...
Страница 54: ...Sheet 2 VSX BOILER BASE SERIES CONVECTION STEAMERS ELECTRICAL OPERATION F24627 0916 Page 54 of 82...
Страница 60: ...Sheet 2 VSX BOILER BASE SERIES CONVECTION STEAMERS ELECTRICAL OPERATION F24627 0916 Page 60 of 82...
Страница 62: ...Sheet 2 VSX BOILER BASE SERIES CONVECTION STEAMERS ELECTRICAL OPERATION F24627 0916 Page 62 of 82...
Страница 64: ...Sheet 2 VSX BOILER BASE SERIES CONVECTION STEAMERS ELECTRICAL OPERATION F24627 0916 Page 64 of 82...
Страница 66: ...Sheet 2 VSX BOILER BASE SERIES CONVECTION STEAMERS ELECTRICAL OPERATION F24627 0916 Page 66 of 82...
Страница 68: ...Sheet 2 VSX BOILER BASE SERIES CONVECTION STEAMERS ELECTRICAL OPERATION F24627 0916 Page 68 of 82...
Страница 70: ...Sheet 2 VSX BOILER BASE SERIES CONVECTION STEAMERS ELECTRICAL OPERATION F24627 0916 Page 70 of 82...
Страница 76: ...AUTO BLOWDOWN Fig 62 VSX BOILER BASE SERIES CONVECTION STEAMERS ELECTRICAL OPERATION F24627 0916 Page 76 of 82...