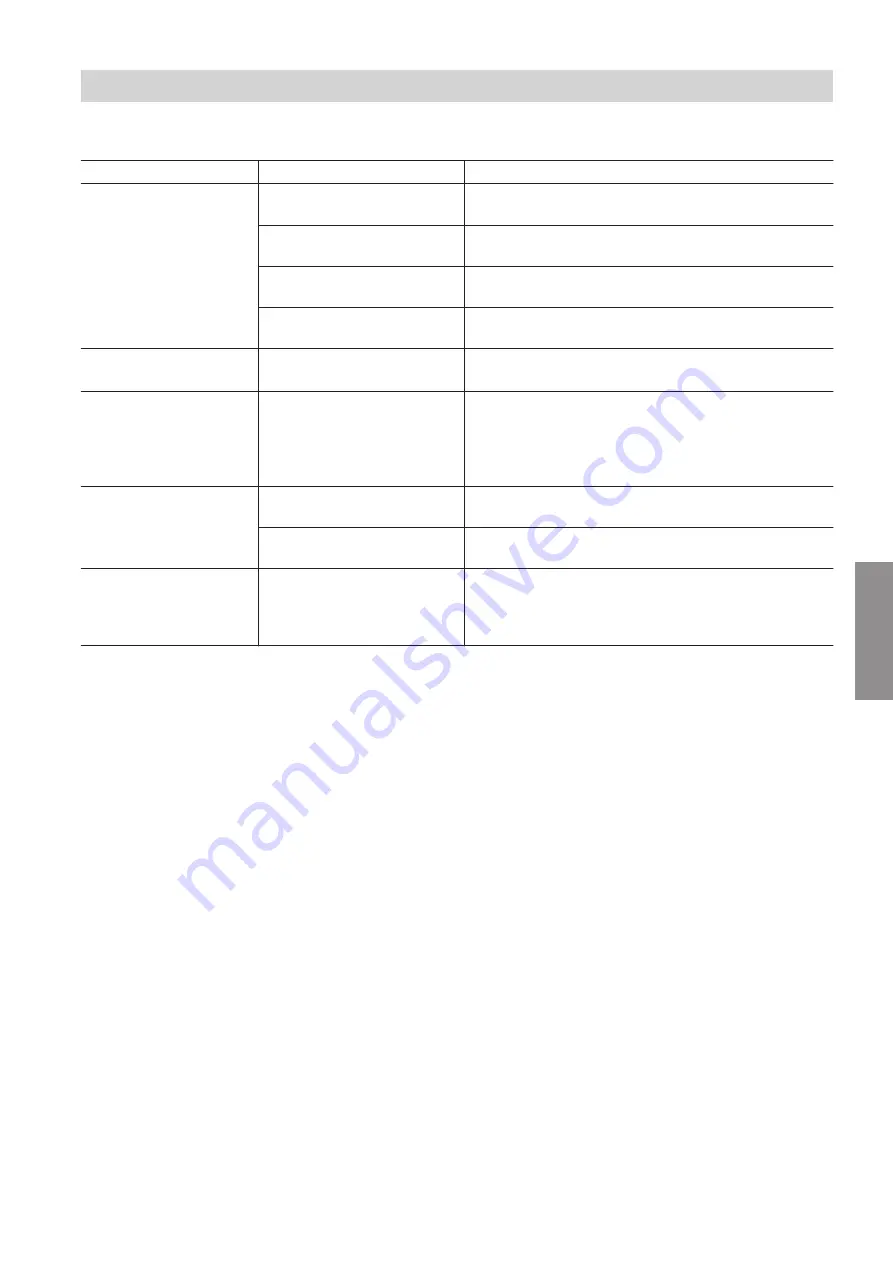
37
Faults without fault display
Fault
Cause of fault
Measure
Combustion faults due to
pulsation
Excessive gas throughput
Adjust gas throughput in accordance with the rated
boiler heating output.
Insufficient or excessive air
Adjust gas throughput in accordance with the rated
boiler heating output.
Condensate backed up in
flue system
Check condensate drain.
Flue outlet not installed cor-
rectly
Check flue outlet.
Whining noises
Incorrect CO
2
settings; insuf-
ficient or excessive air
Adjust burner in accordance with the details on
page 12 onwards.
CO
2
content too low
Incorrect setting
Check whether the burner has been adjusted to the
correct gas type; change gas restrictor if required (see
page 10 onwards).
Adjust burner in accordance with the details on
page 12 onwards.
CO formation or burner is
very sooty.
Insufficient or excessive air
Correct the settings. Check ventilation in installation
room.
Insufficient draught in flue
system
Check flue system.
Excessive flue gas tem-
perature
Excessive gas throughput
Adjust gas throughput in accordance with rated boiler
heating output (see connection values, page 56).
Check condition of secondary heating surfaces of the
boiler and clean if required.
Troubleshooting
Diagnosis
(cont.)
5783 337 GB
Diagnosis
Содержание CT3U
Страница 40: ...40 Burner control unit flow chart Burner control unit flow chart cont 5783 337 GB Diagnosis ...
Страница 61: ...61 5783 337 GB ...
Страница 62: ...62 5783 337 GB ...
Страница 63: ...63 5783 337 GB ...