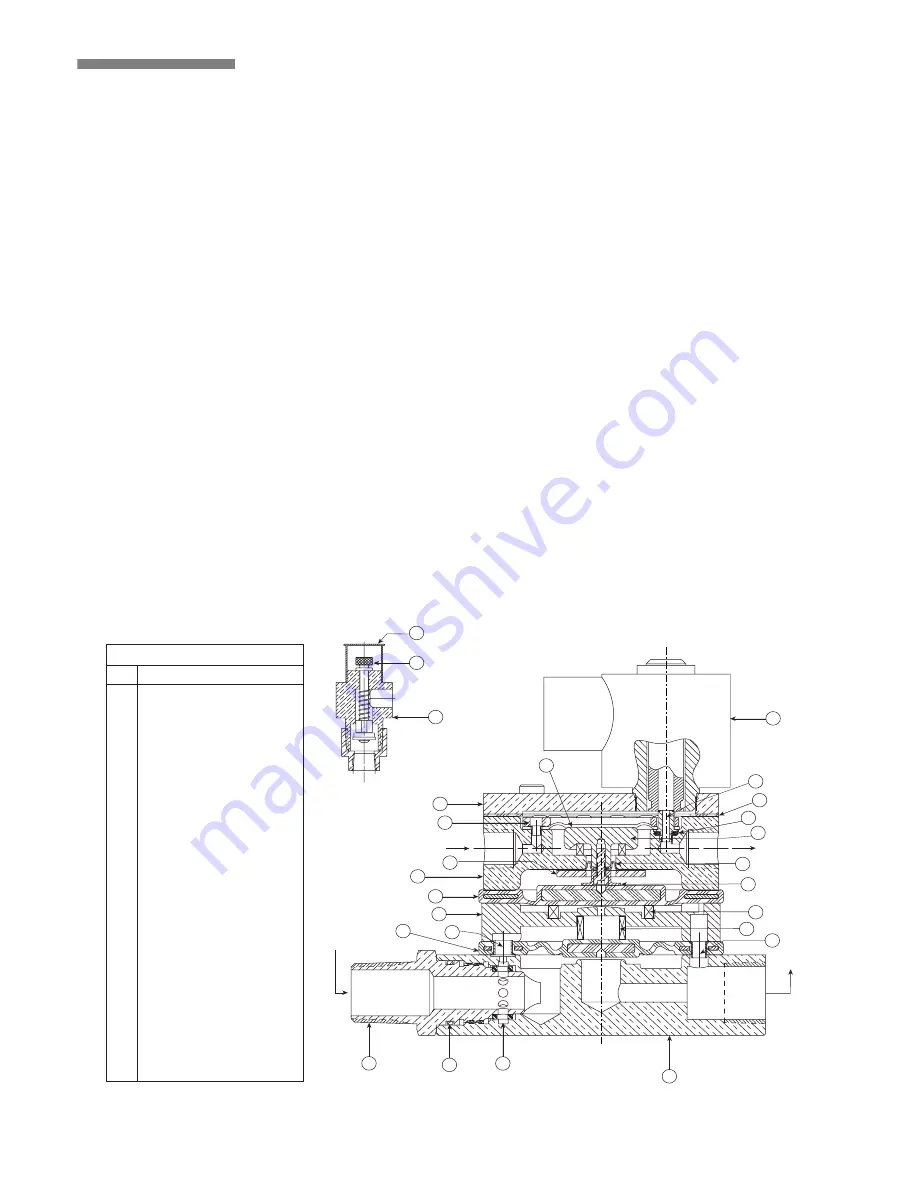
6
SECTION VIEW DRAWING AND DESCRIPTION –
SERIES 79N ELECTRIC/PNEUMATIC ACTUATOR
The Series 79N Electric/Pneumatic Actuator is a single-
unit device used in the actuation of Series 758 Preaction
Valves with double-interlock electric/pneumatic trim.
Diaphragms separate the Series 79N into four chambers.
The upper and upper-middle chambers control the
actuation, while the lower and lower-middle chambers
act as the water control valve.
During system charging, air pressure enters the upper-
middle chamber of the Series 79N. Pulling up on the auto
vent, which is located on the Series 79N trim, sets the air
pressure in this upper-middle chamber. Water supply
pressure from the piston charge line enters the upper
chamber, and the normally closed solenoid, which is built
into the Series 79N, sets this water pressure.
There is no
need to activate the solenoid in order to set the
system.
The system air pressure in the upper-middle chamber
exerts a closing force on the middle chamber of the Series
79N. Additionally, the water supply pressure from the
piston charge line exerts a closing force on the middle
diaphragm through a piston that connects the upper and
middle diaphragms. These pressures close the water path
of the lower-middle chamber.
When the piston charge line is open, water enters the
lower chamber of the Series 79N; this water flows to the
lower-middle chamber through the inlet. The middle
diaphragm traps water in the lower-middle chamber.
Supply water pressure in the upper chamber and system
air pressure in the upper-middle chamber hold the lower-
middle diaphragm assembly closed.
Since the area of the lower diaphragm is greater than the
area of the lower chamber, the lower chamber seals;
therefore, no water flows to the actuator’s outlet, and the
water pressure creates a seal.
When system air pressure decays to 6.5 psi (45 kPa), the
auto vent’s compression spring exerts a force greater than
the air pressure in the upper-middle chamber. The auto
vent opens, and all air pressure in the upper-middle
chamber evacuates. During this condition, the Series 79N
will not actuate, since the water pressure in the upper
chamber maintains a closing force on the water seal of
the lower-middle chamber.
Likewise, if there is an electrical detection event, the
solenoid on the upper chamber will activate and cause
the upper chamber’s water pressure to release. The Series
79N will not actuate, since the upper-middle chamber’s
air pressure exerts a closing force on the lower-middle
chamber’s water seal.
The Series 79N will actuate only when an electrical
detection and loss of system air pressure occur. During
this condition, the closing force on the lower-middle
diaphragm’s water seal is removed, and the lower-middle
chamber’s water pressure releases. This allows the lower
diaphragm to lift and water to flow from the Series 79N’s
inlet to the outlet. This water flow releases water pressure
from the preaction valve’s piston and allows the piston to
retract. The preaction valve’s clapper opens, and water
flows into the sprinkler system.
WATER IN
WATER IN
Located in the
trim of the
upper-middle chamber
TO DRAIN
TO DRAIN
1
16
26
14
12
13
11
3
25
21
19
18
17
20
4
24
23
22
15
5
7
8
9
10
6
2
1
Upper Chamber
2
Upper Diaphragm
3
Upper-Middle Chamber
4
Middle Diaphragm
5
Lower-Middle Chamber
6
Lower Diaphragm
7
Strainer Assembly
8
Strainer o-ring
9
Strainer Screen
10
Lower Chamber
11
Solenoid Valve
12
Auto Vent
13
Auto Vent Protective Cap
14
Auto Vent Knob
15
Outlet Orifice
16
Gasket
17
Upper Piston
18
Isolating Diaphragm
19
Lower Pison
20
Middle Spring
21
Lower Spring
22
Outlet Eyelet
23
Inlet Eyelet
24
Isolating Diaphragm Retainer
25
Upper Diaphragm Retainer
26
Outlet Orifice O-ring
BILL OF MATERIALS
Exaggerated for clarity
Item
Description
DISCONTINUED
PRODUCT