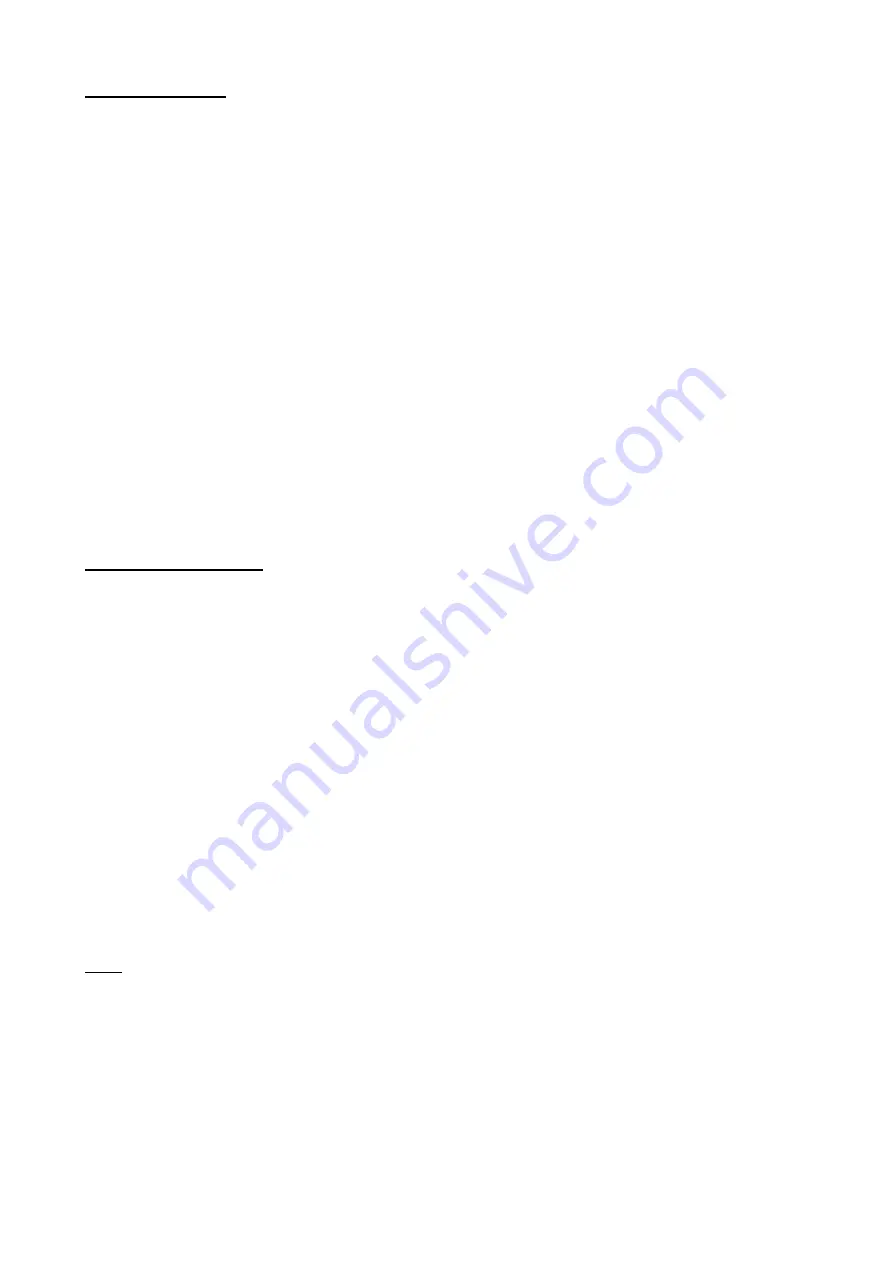
26
8.3 Boiler firing
1. Check the water volume in heating system.
2. Check, whether the closing valves between the boiler and heating system are open.
3. Check the circulating pump functionality
4. Clean the combustion chamber, firing chamber and the ash-pan
5. Check the correct way of mounting the ceramic plates in combustion chamber.
6. Fill the reservoir with prescribed fuel.
7. The boiler is put into operation by means of a manual regime of regulator. By means of screw conveyor
we supply the fuel to the combustion space. Let the conveyor in operation until a half of the fire chamber
is filled with fuel..
8. Place the kindling on the fuel (it means paper, wood chips, PEPO, solidified alcohol or other material
intended for this purpose), light it and let it burn up (approx. 1 - 2 min).Than using a shovel add to burning
kindling a small amount of pellets and switch on the ventilator for a short time. Repeat this procedure.
2 - 3 times.
9. Close the door and let the fire flare up properly (approx. 3 - 5 min). The stoking and ash-pan doors must
be kept permanently closed during the boilers operation.
Note: During the boiler firing process the regulator follows the outlet water temperature. There is
expected an increase in temperature above 30 °C. If this doesn’t occur within 60 min, regulator
will pass over into the stop status (ventilator, fuel conveyor and the pump switch off with after-
running).
The same will happen already after 30 min if during the automatic operation for any reason the
output water temperature drops below 30 °C. The regulator will switch off all units while respecting
the after-running and will be left in stop status until the manual operation has been carried out. All
the time the inscription STOP is alight on the display.
8.4 Boiler operation
After the above parameters have been set and the fuel started to flare properly it is possible to pass into
the automatic operation with ventilator and screw conveyors cycling switched on. On display there is
displayed the actual heating water output temperature and the system status.
Once the water temperature set on the control thermostat has been achieved the boiler operation will
become automatic, with set air and fuel supply. Then the boiler automatically will pass into „inhibition” regime
where it will be left until the heating medium temperature has dropped below the value set on control
thermostat
If the heating system takes a minimum volume of thermal energy the boiler is able to work continuously in
the „inhibition” regime (top-fed stove operation) as long as the fuel is in reservoir. In this status like at setting
the inhibition duration of 30 minutes the average boiler output is approx. 1,5 kW at the fuel consumption of
0,37 kg/h.
In case of feeding voltage (230 V, 50 Hz) outage the regulator remembers its status and keeps it after
supply restoration. If it was in automatic operation then it comes back into automatic operation with water
output temperature control (>30 °C) for 30 minutes. If the temperature during this time does not exceed
30 °C, the regulator switches off the fuel conveyor, ventilator and the pump with after-running. In case that
the regulator before the outage was in inhibition, then after the supply restoration the regulator immediately
gets for 2 minutes into the automatic operation (like in inhibition) and after this time it is controlled according
to the actual status.
Once the critical output water temperature has been exceeded the emergency thermostat will respond
and it will switch off the fuel conveyor and ventilator, independently on regulator. The pump is left in
operation.
If the emergency thermostat control lamp is on:
1.) The heating water critical temperature was exceeded and the emergency thermostat responded to it by
disconnecting the fuel conveyor and ventilator supply. The emergency thermostat can only be switched
on after the temperature has dropped below the set value by unscrewing the black cover of the
emergency thermostat and we press the red pushbutton using a suitable object.
2.) The emergency thermostat red control lamp can also signalise the current overloading of screw
conveyor engines. In this case it is necessary to switch off the boiler at the main switch, remove the
obstruction causing the overloading from conveyor and by turning the main switch again put the boiler
into normal operation.