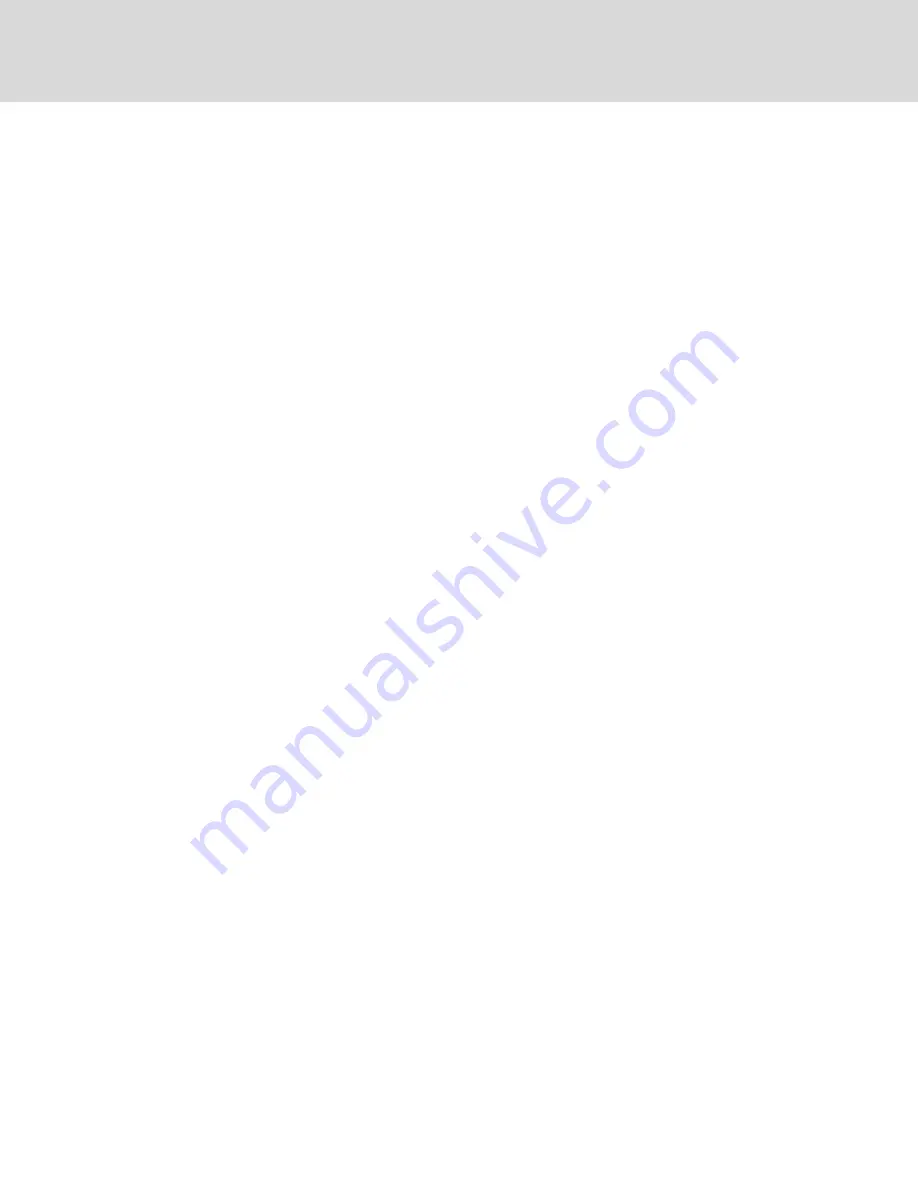
Water chemistry varies greatly by location, as do the required additives, called inhibitors, that
reduce the corrosive effect of the fluids on the piping systems and components. The chemistry
of the water used must be considered, because water from some sources may contain corrosive
elements that reduce the effectiveness of the inhibited formulation. Sediment deposits prevent
the formation of a protective oxide layer on the inside of the coolant system components and
piping. The water/coolant fluid must be treated and circulating through the system
continuously to prevent the buildup of sediment deposits and or growth of sulfate reducing
bacteria.
Proper inhibitor maintenance must be performed in order to prevent corrosion of the system.
Consult glycol manufacturer for testing and maintenance of inhibitors.
Commercial ethylene glycol, when pure, is generally less corrosive to the common metals of
construction than water itself. It will, however, assume the corrosivity of the water from which it
is prepared and may become increasingly corrosive with use if not properly inhibited.
We recommend installing a monitored fluid-detection system that is wired to activate the
automatic-closure of field-installed coolant-fluid supply and return shut-off valves to reduce
the amount of coolant-fluid leakage and consequential equipment and building damage. The
shut-off valves must be sized to close-off against the maximum coolant-fluid system pressure
in case of a catastrophic fluid leak.
NOTICE
Risk of no-flow condition. Can cause equipment damage.
Do not leave the water/coolant fluid-supply circuit in a no-flow condition. Idle fluid allows the
collection of sediment that prevents the formation of a protective oxide layer on the inside of
tubes. Keep unit switched On and water/coolant fluid-supply circuit system operating
continuously.
Refer to the appropriate piping general-arrangement schematics for your system for the recommended,
field-installed hardware such as shut-off valves. See Table 5.1 on page 23.
•
Use copper piping with a brazing alloy with a minimum temperature of 1350°F (732°C), such as
Sil-Fos. Avoid soft solders, such as 50/50 or 95/5.
•
Follow local piping codes and safety codes.
•
Qualified personnel must install and inspect system piping.
•
The water/glycol-cooled system will operate in conjunction with a cooling tower, city water or
drycooler.
•
Contact a local water consultant regarding water quality, corrosion protection and freeze-
protection requirements.
•
Install manual shut-off valves at the supply and return line to each unit to permit routine
service and emergency isolation of the unit.
•
Install a monitored, fluid-detection system that is wired to activate the automatic closure of
field-installed coolant-fluid supply and return shut-off valves to reduce the amount of coolant
fluid leakage and consequential equipment and building damage. The shut-off valves must be
sized to close-off against the maximum coolant-fluid system pressure in case of a catastrophic
fluid leak.
Vertiv | Liebert® CW™ Installer/User Guide
26
Содержание Liebert CW
Страница 1: ...Liebert CW Thermal Management System Installer User Guide 305 kW 375 kW 415 kW Capacity 50 60 Hz...
Страница 10: ...Vertiv Liebert CW Installer User Guide 6 This page intentionally left blank...
Страница 24: ...Vertiv Liebert CW Installer User Guide 20 This page intentionally left blank...
Страница 32: ...Vertiv Liebert CW Installer User Guide 28 This page intentionally left blank...
Страница 34: ...Vertiv Liebert CW Installer User Guide 30 This page intentionally left blank...
Страница 36: ...Vertiv Liebert CW Installer User Guide 32 This page intentionally left blank...
Страница 46: ...Vertiv Liebert CW Installer User Guide 42 This page intentionally left blank...
Страница 48: ...Vertiv Liebert CW Installer User Guide 44 This page intentionally left blank...
Страница 75: ...Vertiv Liebert CW Installer User Guide...