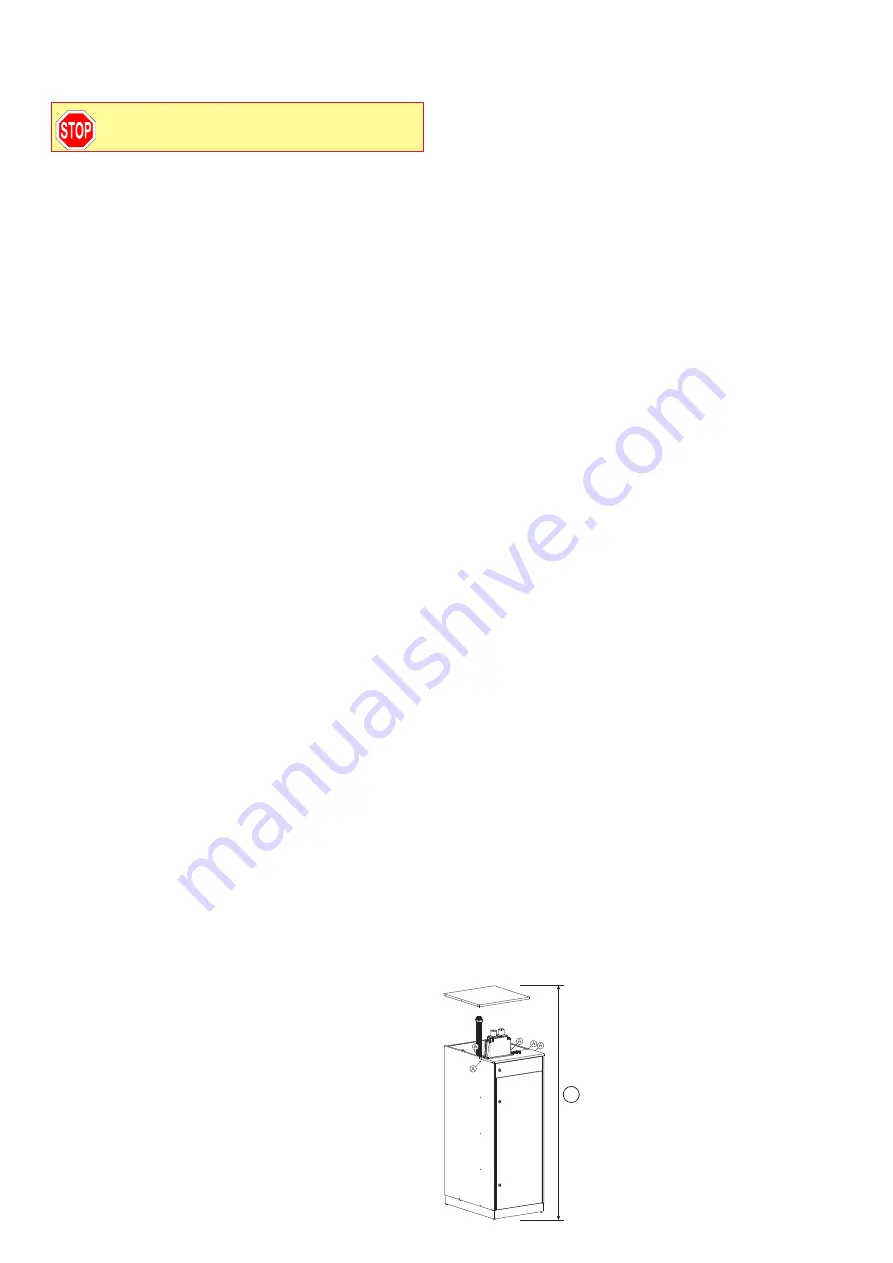
22
VÄRMEBARONEN EP 31 300
Installation must take place according to existing
regulations and standards.
Installation must take place according to existing rules
and standards.
The boiler must be placed indoors, standing.
The boiler can be placed directly on the floor, the location
must be dimensioned for the boiler’s weight when it is
filled with water.
At least 1 meter free space must be retained in front of
the boiler, note the ceiling height for future replacement
of the immersion heaters.
The room should have a floor drain.
Adjust the foot bolts so that the boiler is horizontal.
Pipes must be routed so that it is possible to open the
front and remove the roof plate for service.
Valves must be fitted between the boiler and the heating
system.
Expansion system - The safety pipe, the boiler must be
connected to an expansion system.
An electric boiler fitted with a closed expansion vessel
must undergo an installation inspection prior to first
operation. The inspection must be carried out by a person
who is qualified for the task. The boiler or expansion
vessel may not be replaced without another inspection.
The boiler is not intended for use with oxygenated water.
As frost protection, the water in the system may be mixed
with maximum 30% glycol. Check that the glycol contains
a suitable quantity of corrosion protection additive.
When glycol breaks down, one of the by-products is
carbonic acid, which increases the risk of corrosion.
Water quality
Tap water is usually classified from the point of view of hygiene.
Good water classified on this basis is not automatically suitable
for a heating system. To avoid problems, the water should be
analysed from a technical point of view and any deviations
from standard values should be adjusted.
If the volume of the heating system is low, it can be filled
with water that was not classified as good system water.
When the water is heated, some oxygen and carbonic acid
are emitted to the expansion vessel or vent valves. The remain-
der will react with the metals in the system. This corrosion
is generally insignificant. It is important for the system to be
leak-proof so that the water does not need to be replaced
with new water and the water is not oxygenated during
installation.
In practice, it is impossible to protect large systems against
leaks and oxygen admission. In such cases, an oxygen-
consuming agent can be added so that there is always a
slight surplus in the system. These agents often contain
corrosion-limiting additives.
Water quality - in respect of suitable tap water:
The alkalinity should exceed 60 mg/l to avoid corrosion.
Contents of carbonic acid over 25 mg/l increase the risk of
corrosion.
Sulphate contents over 100 mg/l may accelerate corrosion.
If the sulphate content is higher than the alkalinity, there is
a risk of copper corrosion.
Hard water causes boiler scale and is not suitable in a heating
system. The hardness must be approx. 5-6 dH°.
Very soft water may cause corrosion damage.
Chloride contents over 100 mg/l make the water aggressive,
particular when combined with lime deposits.
Low pH values may cause corrosion damage. The pH value
should be 7.5-8.5.
The incidence of carbonic acid in combination with low pH
and hardness values makes the water aggressive.
The water must not contain sludge or other impurities.
Flow requirements
The boiler must have a constant, sufficiently high flow to
function satisfactorily. The flow must be dimensioned so that
it is within specified limits.
Insufficient water flow can result in the following:
- The difference between the temperature setting and the
actual temperature achieved in the boiler increases.
- Irregular control with increased wear on the boiler's contac-
tors, with reduced service life as a result.
Excessive water flow can result in the following:
- Vibrations in the immersion heaters with noise and reduced
service life as a result.
- Unnecessary wear on the system's components.
Recommended flow produces a
∆
t of 10°C at the boiler's
maximum power. See Technical data.
For minimum ceiling height,
see Technical data.
A = M6 bolts for fixing cable trays, etc.
Pipes, cable ducts, etc. may not be
laid on the boiler's rear cover plate.
General