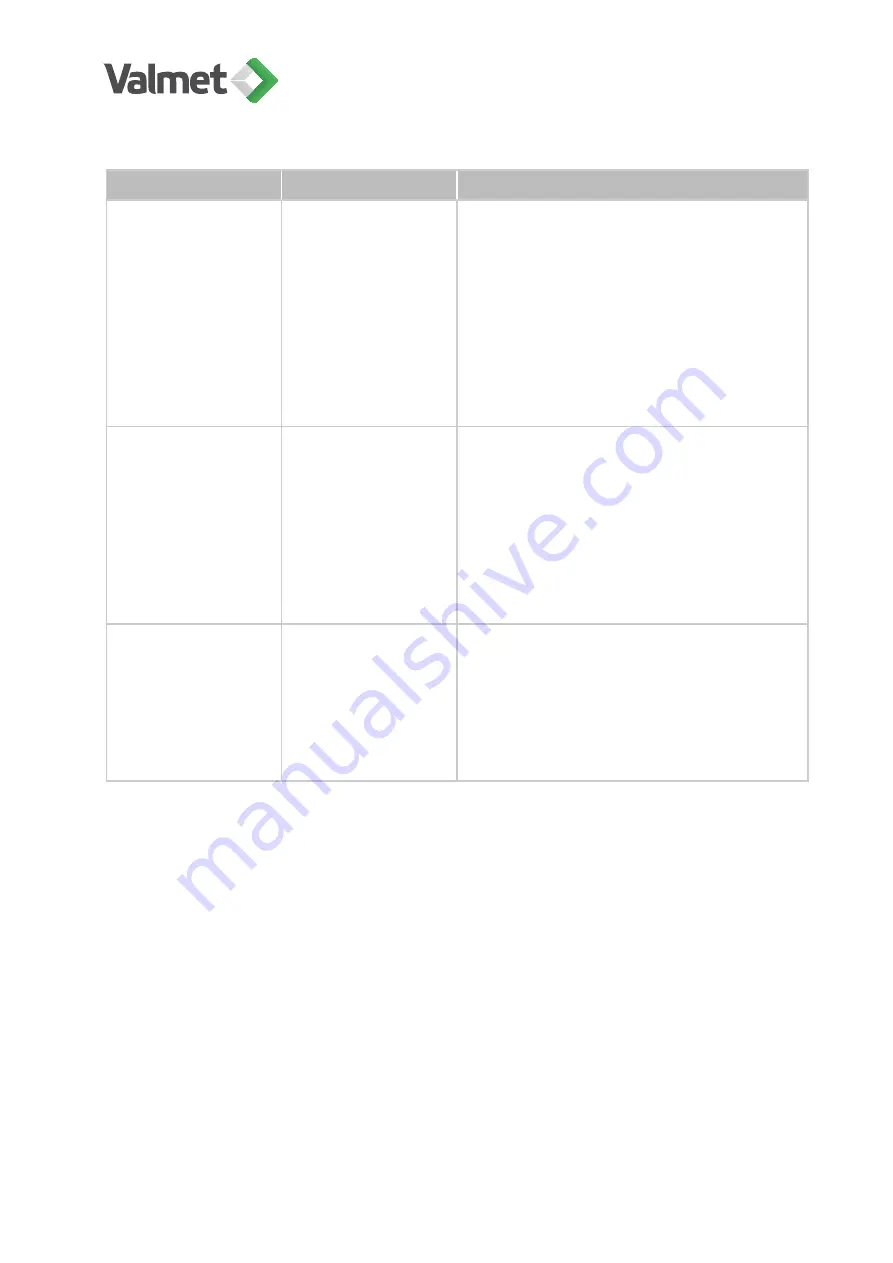
Message
Explanation
What to do
Measurement Signal
Stability
Measurement signal
is too noisy.
Check the diagnostic limit values.
Do sensor self-test:
Service
>
Mainte-
nance
>
Sensor self test
:
• Fail = sensor electronics malfunction.
• Pass = probably a process related issue.
In case of high consistency, signal stability
problems may be caused by the nature of the
measured material. Fine-tune the limits.
Reference Signal
Stability
Reference signal is
too noisy.
Check the diagnostic limit values.
Do sensor self-test:
Service
>
Mainte-
nance
>
Sensor self test
:
• Fail = sensor electronics malfunction.
• Pass = make sure that there is a proper
earth connection between the sensor and
process pipe (applies to FT models).
Process Pressure
Low
Process pressure is
under the set low lim-
it.
Check the diagnostic limit values.
Try to increase the pressure by adjusting
process control settings.
If the measured value does not correspond to
other pressure measurements (or to refer-
ence), the sensor may be defective.
Troubleshooting | 69 (93)
K17122 V1.1 EN - 1 - 06/2020
Содержание K17122
Страница 1: ...Valmet Microwave Consistency Measurement Valmet MCA Installation Operating Maintenance K17122 V1 1 EN...
Страница 34: ...10 3 Menu map Operating 34 93 K17122 V1 1 EN 1 06 2020...
Страница 58: ...Advanced calibration 58 93 K17122 V1 1 EN 1 06 2020...
Страница 60: ...Advanced calibration 60 93 K17122 V1 1 EN 1 06 2020...
Страница 88: ...18 WEEE information Valmet Bridge Sensor WEEE information 88 93 K17122 V1 1 EN 1 06 2020...
Страница 91: ...2 3 Valmet MCA Spare parts Valmet Automation Inc All rights reserved 7 10 9 12 14 15 13 11...
Страница 92: ...3 3 Valmet MCA Spare parts Valmet Automation Inc All rights reserved 16 17...