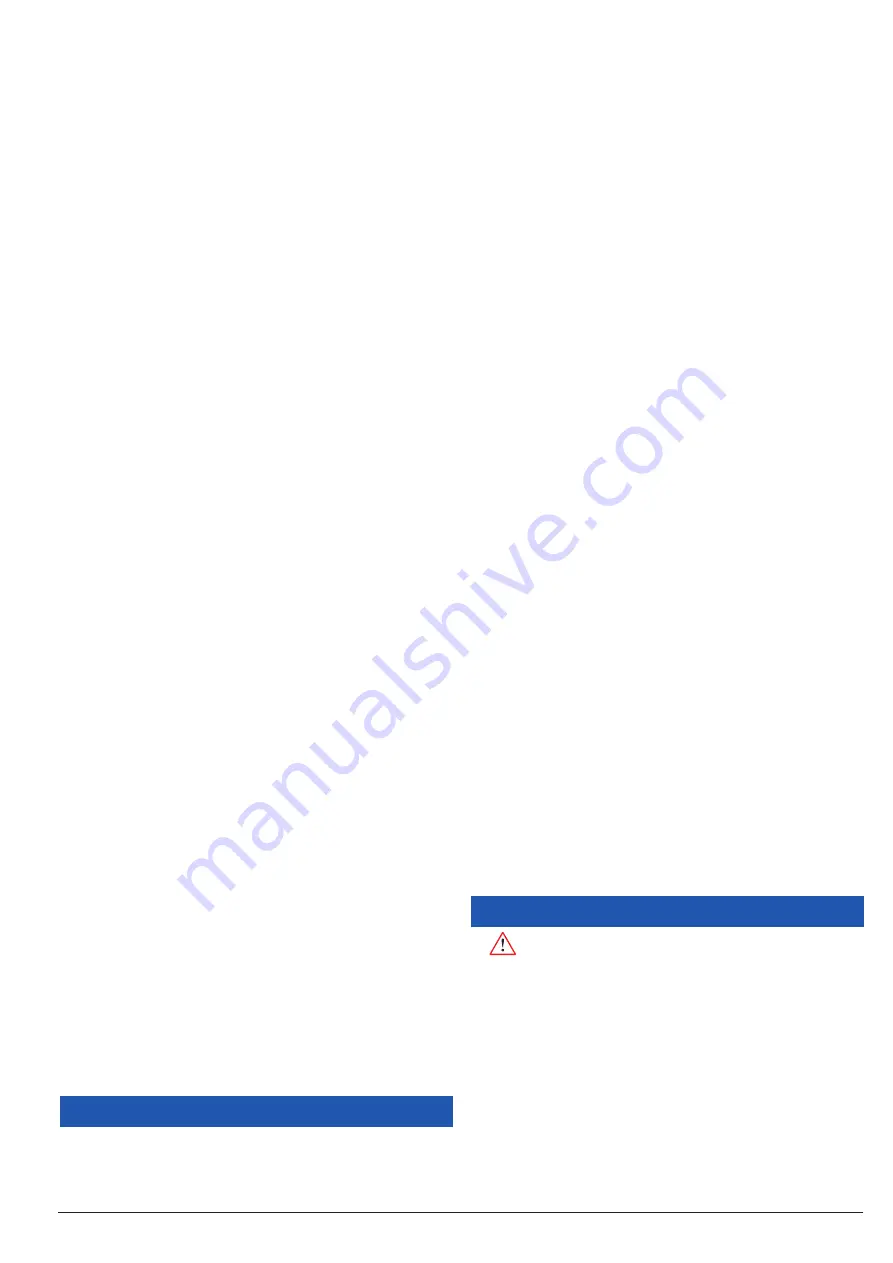
VAG Operation and Maintenance Instructions • 11
4.4 Assembly instructions and fittings
Caution:
Check the valve for possible damage that it may have
suffered during transport and storage. Protect the valve against
dirt caused on the construction site by adequate covering until
installation. Prior to installation all components essential for pro-
per function, such as the seat and the sealing ring of the disk
must be thoroughly cleaned to remove all dirt particles. VAG does
not assume any liability for consequential damage caused by dirt,
shot-blasting gravel residues etc.
The sealing and operational parts should be checked for proper
operation prior to installation.
Should the valves be repainted later on, You should ensure that
no paint is applied to the sealing and operational parts . The iden-
tification plates must not be painted over either. If the equipment
is sand-blasted for cleaning prior to installation, these parts must
be adequately covered. If solvents are used for cleaning, You
should ensure that the solvents do not destroy the seals of the
pipeline or the valve.
For the assembly of the VAG EKN
®
Butterfly Valve type AWWA it
must be ensured that proper load suspension devices as well as
means of transport and lifting devices are available.
In open position, the disk of the VAG EKN
®
Butterfly Valve type
AWWA protrudes beyond the overall length. It needs to be made
sure that there is sufficient space between the disk and other ins-
tallations in the pipeline.
Suspending the valve by its disk may lead to damage to or de-
struction of the disk or valve.
When connecting the valve with the pipeline flanges, hexagon
bolts and nuts with washers from flange to flange must be used
in the through holes. Fasten the bolts evenly and crosswise to
prevent unnecessary tension and the resulting cracks or breaks.
The pipeline must not be pulled towards the valve. Should the gap
between valve and flange be too wide, this should be compen-
sated by thicker seals.
The material of the seal needs to be selected according to the
operation conditions.
The operator needs to select bolts and nuts suitable for the res-
pective operation pressure, temperature, the flange material, the
operational loads and the seal. As depending on the seal materials
used and whether they are used in main friction connections or
secondary friction connections, very different tightening torques
of the flange bolts result, the operator must choose the tightening
torque of the flange bolts according to the above parameters.
Do not over-tighten the bolts of the flanges as this may result in
the flanges cracking.
While the valve is being installed, it must be ensured that the
flanges of the pipeline it is connected to are aligned and level with
each other. Welding works on the pipeline must be performed be-
fore the valves are installed to prevent damage to the seals and
the corrosion protection. Welding residue must be removed befo-
re the equipment is put into operation.
The pipeline must be laid in a way that prevents harmful pipeline
forces from being transmitted to the valve body. Should construc-
tion works near or above the valve not be completed yet, the valve
must be covered to protect it from dirt.
5 Set-up and operation of the valve
bolted connections have been properly fastened.
5.2 Function check and pressure test
Prior to installation, the function parts of the valve have to be ope-
ned and closed completely at least once and should be checked
for trouble-free operation.
Caution:
When a pressure test is performed in the pipeline with a
test pressure exceeding the admissible nominal pressure in clo-
sing direction, the pressure must be compensated by way of a
bypass.
If the VAG EKN
®
Butterfly Valve type AWWA is operated in dry
state, higher actuation torques may be expected.
Newly installed pipeline systems should first be thoroughly purged
to remove all foreign particles. Residue or dirt particles present
in the pipeline may impair the function of the valve .or prevent its
free movement.
In particular after repair work or upon the commissioning of new
equipment, the pipeline system should be purged again with the
valve being fully open position. If detergents or disinfectants are
used it must be ensured they do not attack the valve materials. As
a standard, the valve is closed by turning clockwise at the gear.
The dimensions of the stems and actuators allow operation of the
valve by one person via the handwheel. Extensions for operation
are not permissible as they may damage the valve due to exces-
sive force. The 90° turn is limited by a limit stop located at the
gear. If it is turned further using excessive force, this may cause
damage. Proper function is to be checked by opening and closing
the valve several times.
5.3 Putting electric actuators into operation
Turn the valve into medium intermediate position by hand. Check
the rotary motion at the gear and thus the direction of rotation of
the motor by shortly starting the actuator electrically. If the direc-
tion of rotation is wrong, reverse the polarity of the motor con-
nection.
By short electrical start-up, check the direction of rotation again
by checking the direction of motion.
Check the switch-off function of the torque and limit switches in
both directions by manually operating the switches in intermedia-
te position. Reverse the polarity, if necessary. The valve must not
be operated over its entire travel until the direction of rotation and
the switch-off function are correct.
Caution:
If the direction of rotation is wrong, the limit and torque
switches have no effect at all!
6 Actuators
Warning:
Non compliance of these directives may cause
danger to life and limb and/or cause damage
to material or pipeline system.
6.1 General
Actuators (gears, pneumatic, hydraulic and electric actuators)
are designed for flow velocities according to AWWA Class 150 B
(valves used for water supply; requirements relating to fitness for
use). Any deviating operating conditions need to be specified. The
adjustment of the limit stops (OPEN, CLOSE) must not be chan-
ged without the manufacturer’s consent.
Caution:
Danger of damages to the VAG Butterfly Valve!. False
settings of limit stops may cause mechanical risk of injury of the
valve and gearbox.
5.1 Visual inspection and preparation
Before putting the valve and the equipment into operation, per-
form a visual inspection of all functional parts. Check whether all