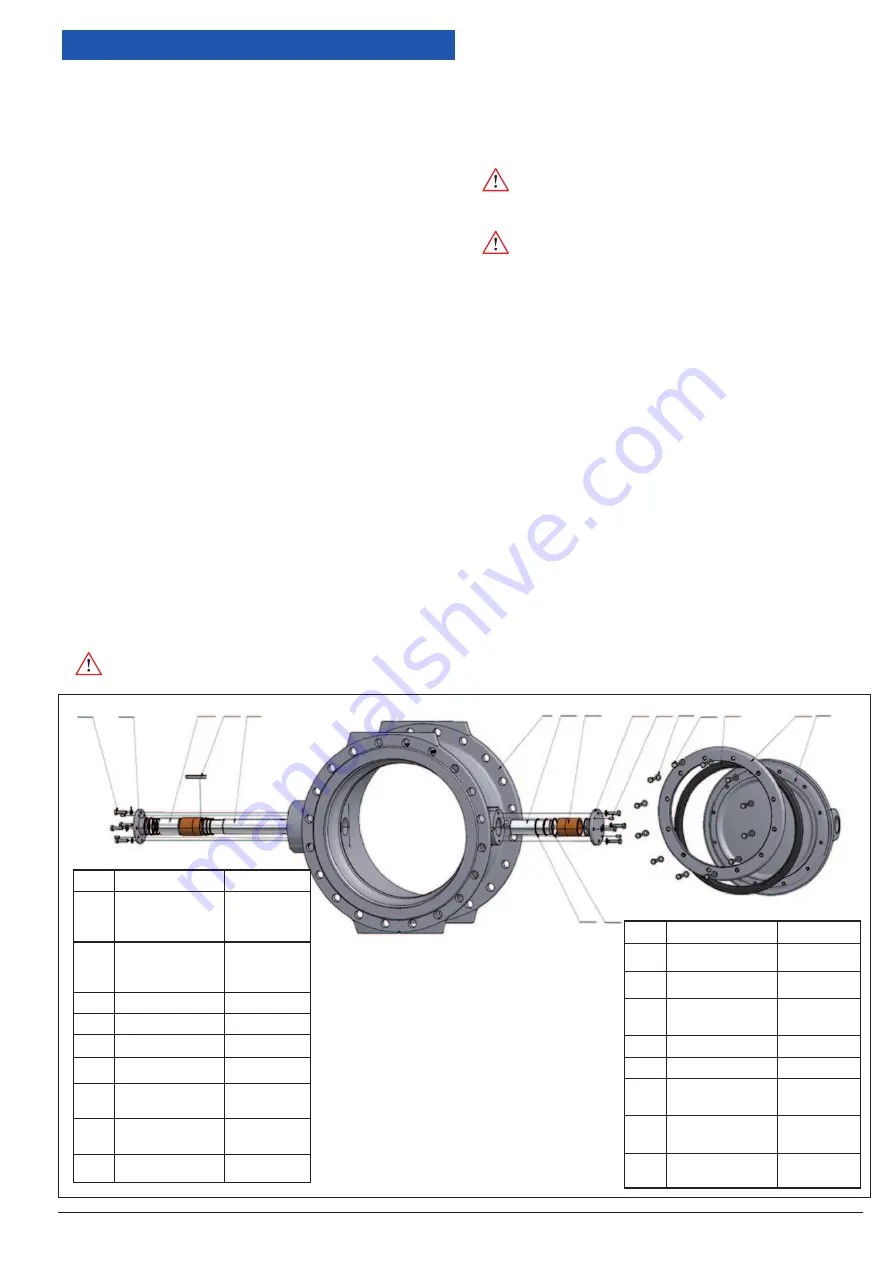
VAG Operation and Maintenance Instructions • 13
7.1 General safety instructions
Caution:
Prior to the performance of inspection and maintenance
work on the valve or its assemblies, shut-off the pressurised pipe-
line, depressurise it and secure it against inadvertent activation.
Depending on the type and risk of the fluid conveyed, comply
with all required safety regulations! After completing the mainte-
nance works and before resuming operation, check all connec-
tions for tightness. Perform the steps described for initial set-
up as described under Section 5 “Set-up and operation”. A VAG
EKN
®
Butterfly Valve type AWWA not equipped with a gear unit is
not self-locking. The actuator/the gear unit may not be disassem-
bled as long as the valve is pressurised. This also applies in case
the valve is completely dismantled. Statutory and local provisions
as well as the safety and accident prevention regulations must be
observed and complied with at all times. Couplings and connec-
tions must never be disassembled when they are under pressure.
Servicing, maintenance and inspection work as well as the repla-
cement of spare parts must only be done qualified staff. The plant
operator is responsible for determining the suitability of the staff
or for ensuring the relevant qualifications.
In case the operator’s employees do not have the qualifications
required, they need to attend a training course. This training
course can e.g. be held by VAG Service employees. In addition to
this, the plant operator needs to ensure that all employees have
understood these Operation and Maintenance Instructions as well
as all further instructions referred to in them. Protective equip-
ment such as safety boots, safety helmets, goggles, protective
gloves etc. must be worn during all work requiring such protective
equipment or for which such protective equipment is prescribed.
Improper or wrong use of the valve should be avoided. Prior to the
performance of any work on the valve and equipment it must be
ensured that the relevant pipeline section has been depressurised
and/or de-energised.
•
Danger:
Danger of bruise between valve body and
pipeline (-flanges) during removing the valve!
7 Maintenance and repair
Death or serious injury can result if persons remain between valve
and pipeline!
- Never stand under a suspended load!
- Lift the valve carefully until it is freely suspended.
- Avoid valve’s tilting by always moving it cautiously during lif-
ting and transport.
- Make sure that no person stays in hazardous area.
•
Danger:
Dangers from electrical current!
Death or serious injury can result when coming into
contact with energised parts.
•
Warning:
Suspended Load! All parts of the valve can tilt
and can be damaged while being lowered!
Danger of injury during lifting and transport.
7.2 Inspection and operation intervals
The valve should be checked for tightness, proper operation and
corrosion protection “at least once per year” .
In case of extreme operating conditions inspection should be per-
formed more frequently.
7.3 Maintenance work and replacement of
parts
7.3.1 Design
The design view in Picture 11 serves as a partial overview for the
descriptions of the working steps below.
No.
Designation
Material
1
Body
ASTM A536,
Grade 65-
45-12
2
Disk
ASTM A536,
Grade 65-
45-12
3
Profile seal
EPDM
4.1
Retaining ring
SA 105
5.1
Hexagonal screw SA 193 B8M
5.3
Washer
AISI 316
7
Shaft, driven end A276 Grade
304
8
Shaft, free end
A276 Grade
304
10
Bearing flange
A383C-A
No.
Designation
Material
11
Bearing cover
A383C-A
12
Bearing bush
C90800
13
Spacer bush
AISI 304
14
Hexagonal screw A383C-A
15
Threaded pin
A383C-A
16
O-Ring
EPDM
17
O-Ring
EPDM
20
Tapper pin
A276 Grade
431
Picture 11: Design and sub-assemblies
14
10
13
20
7
1
8
12
11
15
5.3 5.1 3
4.1 2
17
16