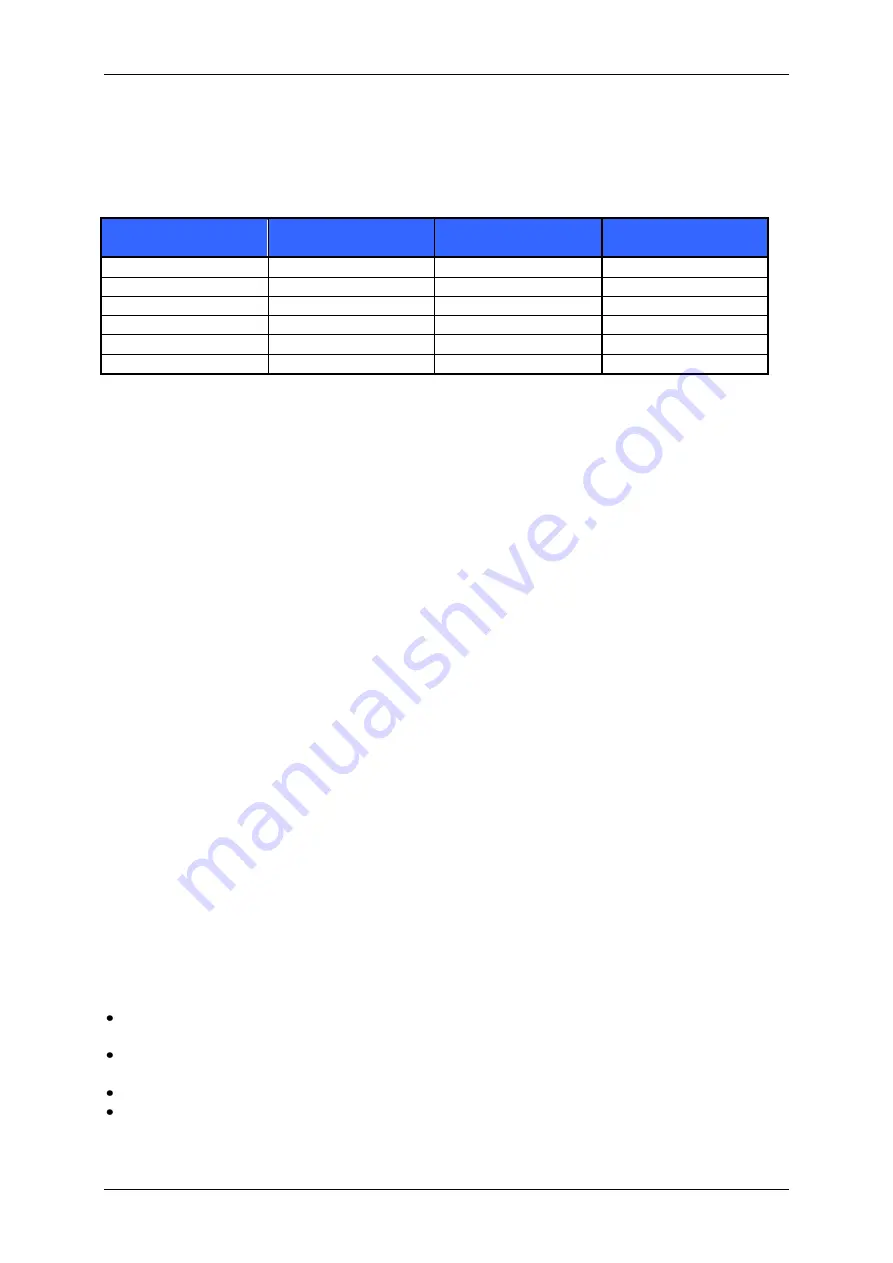
TMCM-035 Manual (V2.09 / February 27
th
, 2009)
13/18
Copyright © 2007-2009, TRINAMIC Motion Control GmbH & Co. KG
Another way of setting a different peak coil current is to connect the RSA pins to GND via an external
resistor and the RSB pin via the same size of resistor. The two resistors should be in the range
100mOhms to 1 Ohm. This possibility can also be used when the module is connected via its
analogue interface. However it is very important to use SMD resistors with low inductivity and very
short traces to GND for a stable operation in this configuration.
peak coil current
RMS current
(microstep operation)
RSA1, RSB1
RSA2, RSB2
1.0 A
0.7 A
open
each 0.22 R to GND
1.2 A
0.85 A
each 0.18R to GND
open
1.7 A
1.2 A
GND
each 1.5R to GND
2.1 A
1.5 A
GND
each 0.47R to GND
2.8 A
2.0 A
GND
each 0.15R to GND
4.2 A
3.0 A
each 0.27R to GND
GND
Table 4.8: Current fine adjustment with RSA and RSB
4.4.2
Standby current reduction for Step-/ Direction mode
In step / direction interface mode, the current control will switch to the INA and INB inputs when
there has been no step pulse for at least four seconds. Current control will switch back to the normal
value set via RSA/RSB pins when the next step pulse occurs. This way the standby current can be set
using the INA and INB pins (by applying a voltage between 0 (0%) and 2V (100%). The maximum
current while the motor is running must be set using the RSA/RSB pins.
The coil current should be reduced when the motor is standing still!
Power down current set value = Value from Table 4.7 * (INA/INB-Voltage) / 2V
4.4.3
Continuous Current restrictions / Thermal conditions
The module is designed as a microstepping module, with sine wave currents (sine and cosine) driving
both coils. The current peak of the sine wave can be as high as 5A, when the RMS current is set to
3.5A. The mean motor current (RMS) is calculated by dividing the peak current by 1.41.
The compact design of the module does not allow to continuously drive the full current unless forced
air cooling is used to keep the board temperature below 85°C, because of excessive heat generation.
On a short term basis, the board is allowed to reach 105°C, but it will shorten life time, if this occurs
in longer periods. However, since continuous maximum current operation also shortens the lifetime of
the motor, this is in most cases no restriction. The driver transistors on the module (8 transistors
labeled “4450” or similar) may heat up to 120°C at their surface - this is not critical!
The module provides a thermal protection, but this is only meant as a means against sudden
destruction, i.e. when a cooling blower fails and the module slowly overheats. The protection is not
meant to limit normal operation! It can not protect against all faults, since it is central in the TMC249
IC, and might react too slowly!
The following limits apply:
Maximum environment temperature for up to 3.5A RMS (=
5A
peak
) is
40°C
, module mounted
vertically
Maximum environment temperature for up to 2.5A RMS (=
3.5A
peak
) is
60°C
, module mounted
vertically
If the module is mounted horizontally, use forced air flow for current above 2.0A RMS.
The phase current should be reduced to a maximum of 70% of the above values while the motor
is standing