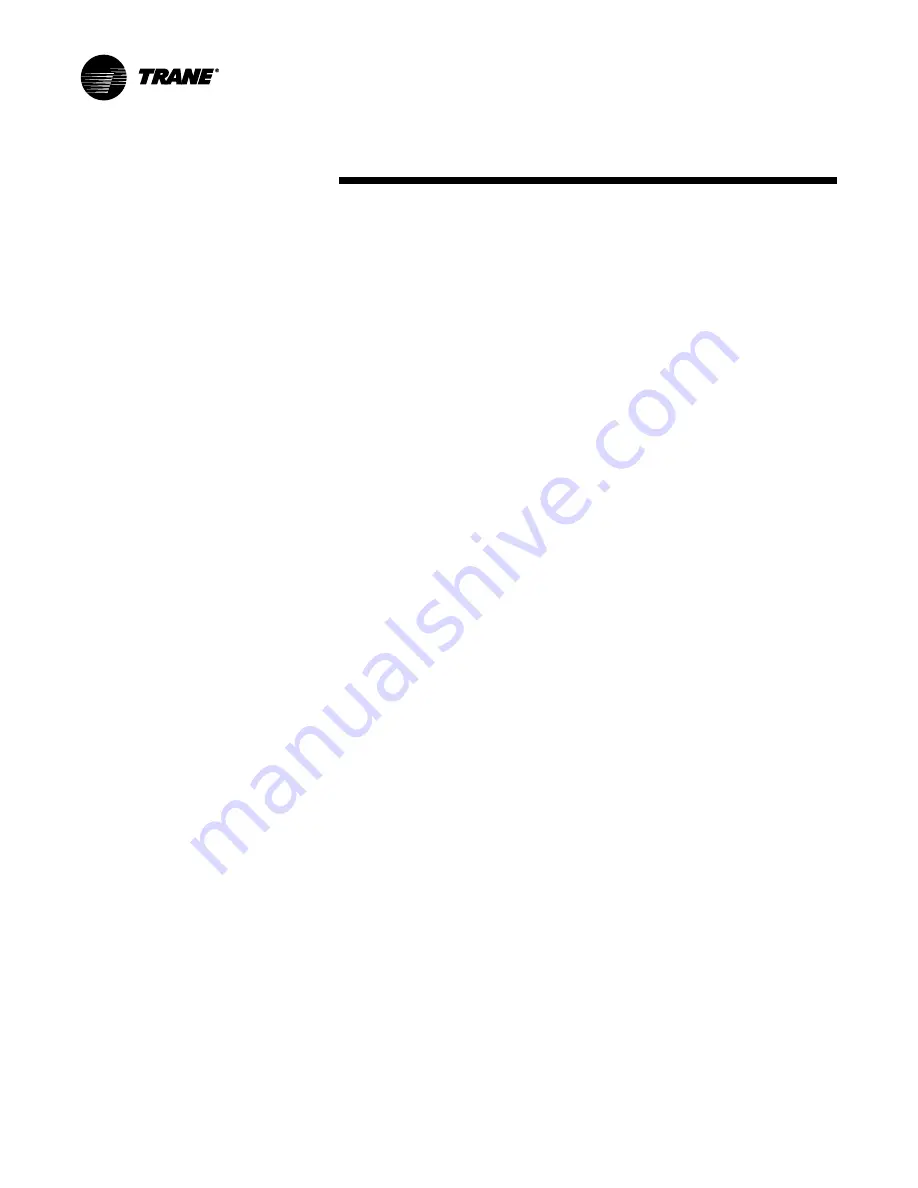
12
RT-PRC024-EN
Cooling Capacity
Note:
Cooling Capacity Procedure
is the same for cooling (TC*)
and gas/electric (YC*).
Step 1.
Calculate the building's total and
sensible cooling loads at design
conditions. Use the Trane calculation
methods or any other standard
accepted method.
Factors used in unit selection:
Total Cooling Load: 180 MBh
Sensible Cooling Load: 129 MBh
Airflow: 6000 cfm
Electrical Characteristics: 460/60/3
Summer Design Conditions:
Entering Evaporator Coil: 80 DB, 67
WB Outdoor Ambient: 95 DB
External Static Pressure: 0.49 in. wg
Rooftop - downflow configuration
Accessories
•
Roof curb
•
Economizer
•
Electric Heat
Step 2.
As a starting point, a rough
determination must be made of the
size of the unit. The final selection
will be made after examining the
performance at the given conditions.
Divide the total cooling load by
nominal BTUH per ton (12 MBh per
ton); then round up to the nearest
unit size.
180 MBh / 12 MBh = 15.0 tons
Step 3.
Table 7
shows that a TCD180B4 has a
gross
cooling capacity of 184 MBh
and 130 MBh sensible capacity at
6000 cfm and 95 DB outdoor
ambient with 80 DB, 67 WB air
entering the evaporator.
To Find Capacity at Intermediate
Conditions Not in the Table.
When the design conditions are
between two numbers that are in the
capacity table, interpolation is
required to approximate the
capacity.
Note:
Extrapolation outside of the
table conditions is not
recommended.
Step 4.
In order to select the correct unit
which meets the building's
requirements, the fan motor heat
must be deducted from the gross
cooling capacity. The amount of heat
that the fan motor generates is
dependent on the effort by the motor
- cfm and static pressure. To
determine the total unit static
pressure you add the external static
pressure to the additional static
related by the added features:
Note:
The Evaporator Fan
Performance
Table 24
has
already accounted for the
pressure drop for standard
filters and wet coils (see note
below
Table 24
). Therefore,
the actual total static
pressure is 0.60 -0.10 (from
Table 54
= 0.50 wg).
With 6000 cfm and 0.50 wg.
Table 24
shows 2.56 bhp for this unit. Note
below the table gives a formula to
calculate Fan Motor Heat,
3.15 x bhp = MBh.
3.15 x 2.56 = 8.06 MBh.
Now subtract the fan motor heat
from the gross cooling capacity of
the unit:
Net Total Cooling Capacity
= 184 MBh - 8.06 = 175.9 MBh.
Net Sensible Cooling Capacity
= 130 MBh - 8.06 = 121.9 MBh.
Step 5.
If the performance will not meet the
required load of the building -total or
sensible cooling load, try a selection
at the next higher size unit.
External Static Duct System
0.49 wg
Standard Filter 1 in. from
Table 54
0.10 wg
Economizer from Table 56
Table 54
(100% Return Air)
0.04 wg
Electric Heater Size 36 kW
from
Table 54
0.07 wg
(reference "Heating Capacity" section on
this page for determination of heater size).
No additional static add for gas/heat
exchanger.
Total Static Pressure
0.60 wg
Heating Capacity
Note:
Heating capacity procedures
DIFFER for cooling (TC*) and
gas/electric (YC*) units.
Step 1.
Calculate the building heating load
using the Trane calculation form or
other standard accepted method.
Step 2.
Size the system heating capacity to
match the calculated building
heating load. The following are
building heating requirements:
TC* cooling units:
460 volt/3 phase Power Supply
Total heating load of 115.0 MBH
6000 cfm
The electric heat accessory
capacities are listed in
Table 56
.
From the table, a 36 kw heater will
deliver 122.94 MBh at 480 volts. In
order to determine capacity at 460
volts, the heater voltage correction
factor from
Table 57
must be used.
Therefore, 122.94 MBh x .94 (voltage
correction factor) = 115.6 MBh.
YC* gas/electric: Fuel natural gas
total heating load of 195 MBh. Table
24 shows 250 MBh and 350 MBh
input models. The output capacities
of these furnaces are 203 MBh and
284 MBh respectively. The low heat
model with 203 MBh output best
matches the building requirements.
Air Delivery Selection
Note:
Air Delivery procedures is
the same for cooling (TC*)
and gas/electric (YC*) units.
External static pressure drop
through the air distribution system
has been calculated to be 0.50 inches
of water. From
Table 54
static
pressure drop through the
economizer is 0.04 and the 36 kw
heater is 0.07 inches of water (0.49 +
0.04 + 0.07). Enter
Table 54
for a
TCD180B4 at 6000 cfm and 0.50
static pressure. The standard motor
at 777 rpm will give the desired
airflow at a rated bhp of 2.71.
Selection Procedure
Содержание Voyager TC Series
Страница 10: ...10 RT PRC024 EN Features and Benefits Figure 1 Voyager Factory Installed Options Factory Installed Options...
Страница 84: ...84 RT PRC024 EN Figure 3 12 5 25 Tons Cooling with Optional Electric Heat Typical Wiring...
Страница 106: ......
Страница 107: ......