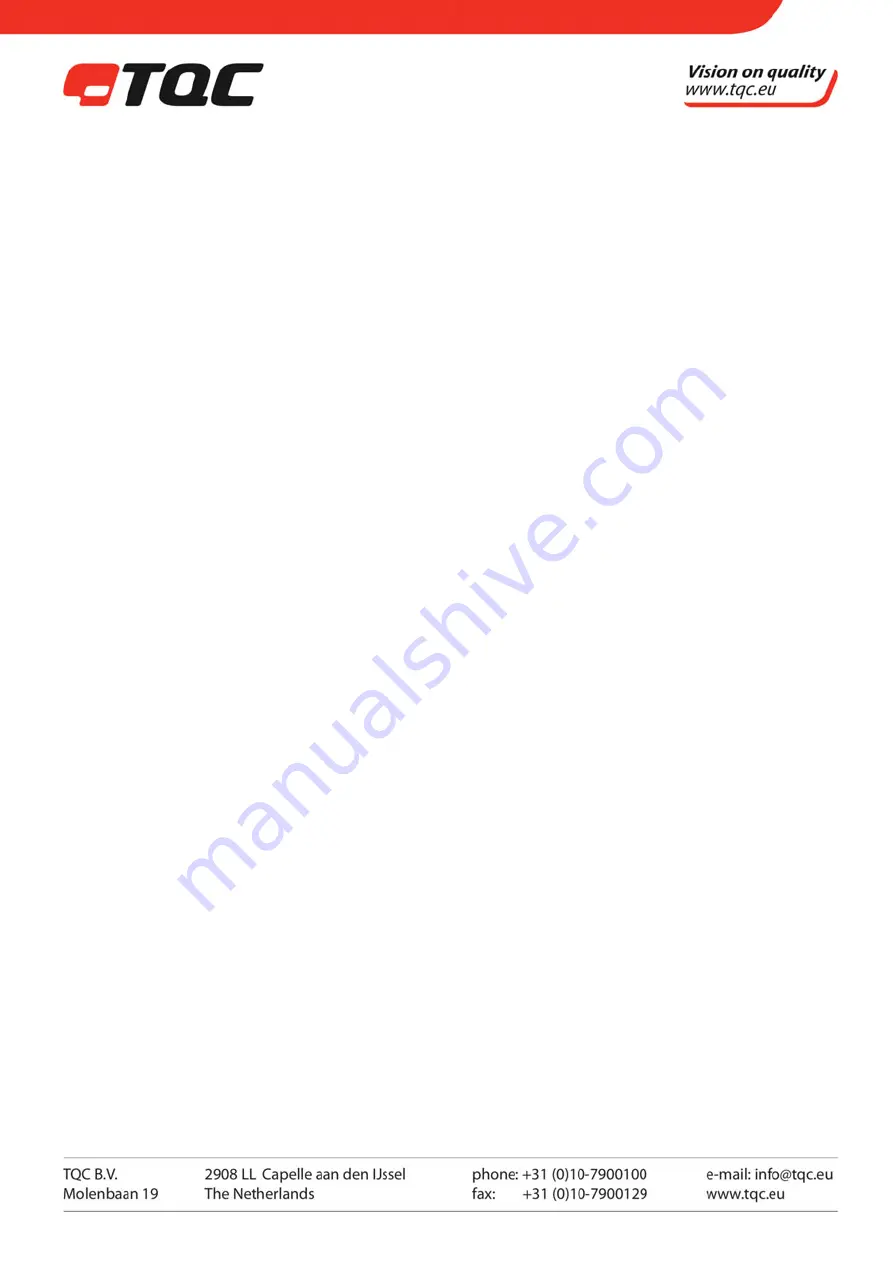
5 |
the backlight will be activated. Every operation the backlight will turn on for 7sec. until the gauge is switched
off again. If the gauge is not operated for over 2 minutes, it will automatically switch off and the backlight
function will be cancelled.
5.7 Measurement tips
1. Cleaning the surfaces
Before making a measurement please make sure dust, dirt rust and grease are removed from the surface.
2. Decreasing the surface roughness
Too rough surfaces may result in measuring faults or error readings. Please try to smooth the surface by milling,
polishing, filling or a use a high viscosity coupling gel.
3. Rough machined surfaces
The regular tiny texture/slots resulting from rough machining processes may cause errors. Please follow the
method as mentioned at paragraph 3 Operating Instructions “Roughness condition”. Adjusting the angle
between the crosstalk segregating board of the probe (a metal membrane crossing the detector bottom centre)
and linear texture slots (parallel or vertical) may also get better results.
4. Measuring cylindrical surfaces
When measuring cylindrical surfaces like pipes, oil tubes etc. it is critical to select an angle between the
crosstalk segregating board of the probe and axis of the material to be measured. In simple terms; couple
the probe and material, keep the crosstalk segregating board of the probe right-angled to the axis of the pipe
to be measured. For small pipes two measurements should be performed, one with the axis of the pipe
perpendicular, the other one parallel. The smallest of the 2 values displayed, should then be taken as the
thickness at that point.
5. Complex shaped materials
For complex shaped material measurements please check paragraph 4.7.3., the smallest of the two readings
should in this case be used as the thickness.
6. Non-parallel surfaces
To get a satisfying ultrasonic response, the surface must have got one measuring side parallel to another side,
otherwise the results will be faulty.
7. Material surface temperature influences
The size and sound velocity of material will change at different temperatures. When precision is critical please
make 2 different measurements under the same temperature conditions to determine the correct thickness
reading. When making steel measurements with high temperatures, this method may be used also to get a
correct reading.
8. High acoustic reduction materials
For materials such as fiber, poriferous or big granular, acoustic dispersion will cause energy attenuation which
may result in abnormal readings (the reading is less than the actual thickness) In this case, the material is not
suitable for the gauge.
9. Reference sample block
Calibrating the gauge, a given thickness or sound velocity of the material is very important. Calibration needs at
least one standard reference sample block. This gauge is provided with a 4.0mm sample block on the front of
the casing. Please check the calibration procedure.