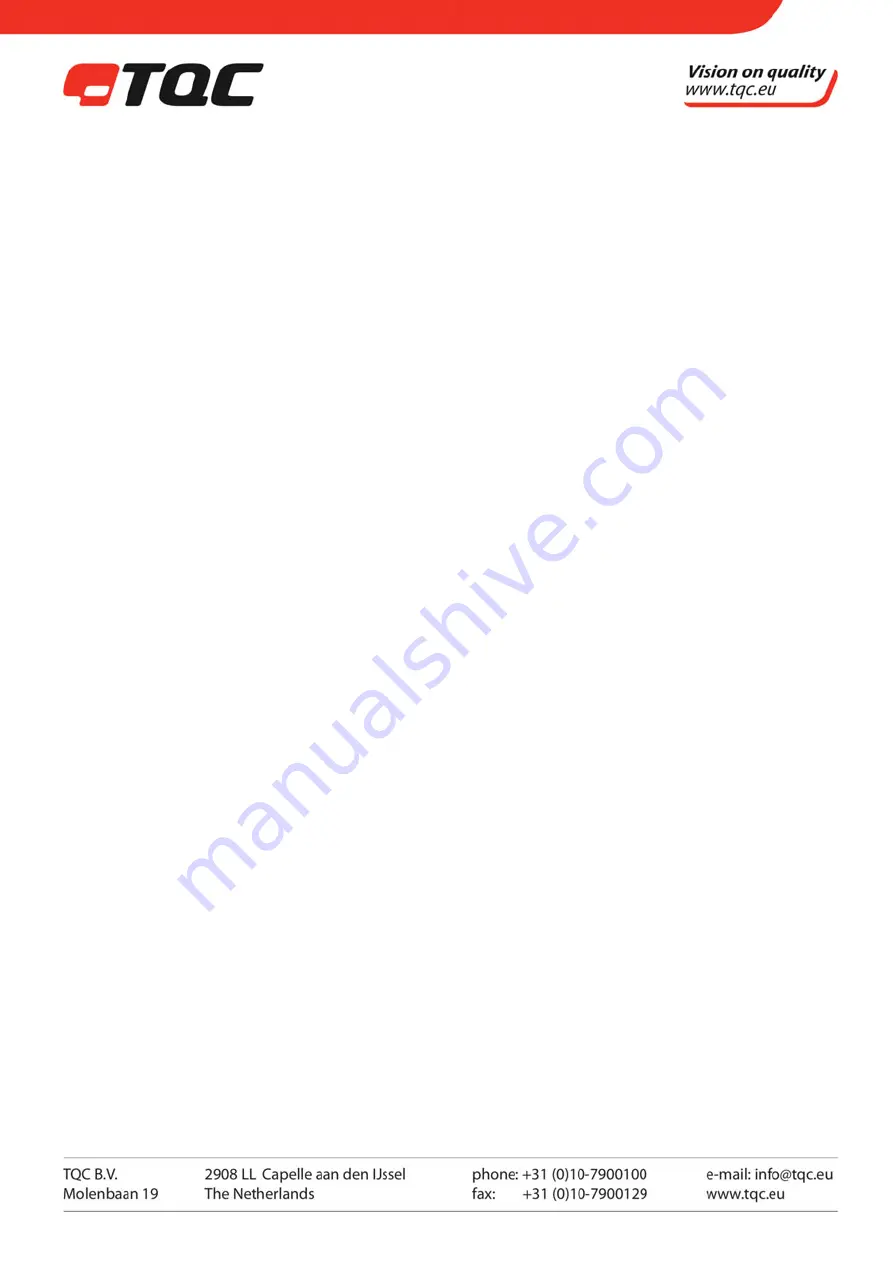
6 |
With different materials and situations, only one sample block may not be enough to get the most exact
calibration. The more similar sample blocks, the more exact readings will be obtained. Ideally reference blocks
are a group of different thicknesses of the same material. When calibration the gauge with different blocks, the
variation of sound velocity will be minimised. To get a most exact measurement, a set of reference blocks is very
important.
In most situations using only one reference block will result in a proper measurement. This reference block must
be the same material and thickness as the parts to be tested. The thickness of the reference block should be
read out in micrometers.
When measuring thin materials of which the thickness is close to the minimum limit range of the gauge, please
use a reference block to define the exact limit of the material (1.2mm for steel material) Do not measure
material from which the thickness is under the minimum limit.
When material consist of a complex alloy in a large size, a block which has a similar material thickness, should be
used for calibration.
Forged or casted hardware mostly have different inner structures which results in slightly different sound
velocities. To reach the exact reading, the reference block most have a similar structure as the hardware. With
common measurements you have to check the sound velocity table stated in this manual instead of calibrating
the gauge with a reference block. However this table is just for reference, sometimes the sound velocity will be
different caused by different physical/chemical factors. The sound velocity of mild steel is mentioned in the
reference table.
5.8 Accuracy precautions
1. Thin material
When the thickness of the material is less than the minimum limit, any ultrasonic thickness gauge will give
faulty measurements. Use the sample block comparing method to get a minimum limit of a material. When
measuring thin material, an error may occur (the thickness reading is two times the actual thickness) To prevent
wrong readings with thin material, double check the minimum limit of the material.
2. Stained/rusted material:
Stained or rusted surfaces on the contra side will result usually in wrong readings. Sometimes a small stained
spot is hard to find. Be careful while measuring known rust spots/suspicious areas or use sound insulation
board-celotex to locate the spots in different test angles.
3. How to determine velocity of various materials
A faulty reading will be obtained, when measuring the material with a velocity calibrated with a previous
material. So a correct velocity should be obtained. The faulty reading may also result from the difference
between the actual velocity of the calibrated value.
4. Wearing of the probe
Because the probe is made of propylene, long term use will cause the surface to roughen, this will result
eventually in wrong readings. Please polish the surface with sand paper or whetstone to assure the smoothness.
If the readings are still unsteady, the probe should be replaced by a new one.