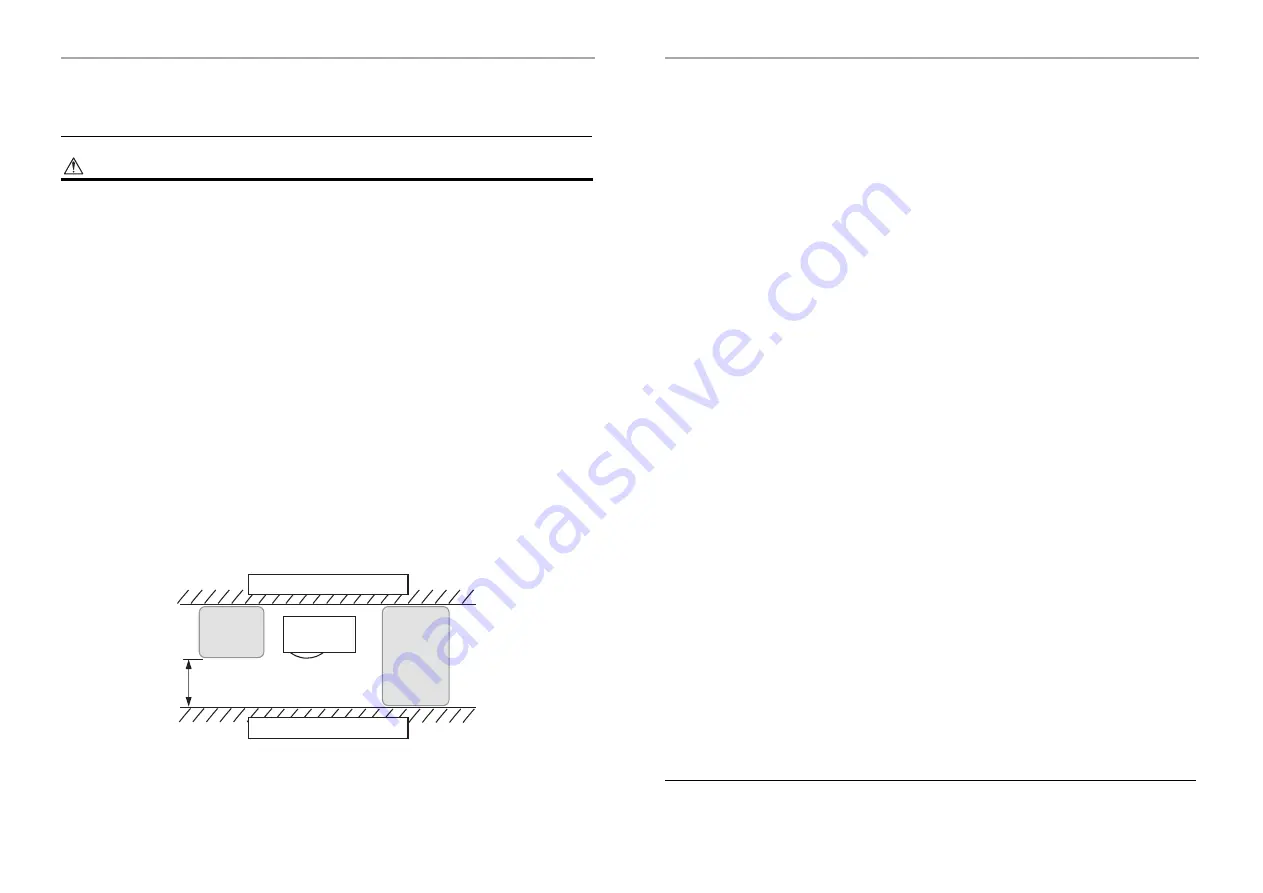
– 5 –
Outdoor Unit
Installation Manual
•
The pipe-work shall be protected from physical damage.
•
Compliance with national gas regulations shall be observed.
This Air to Water Heat Pump adopts the HFC refrigerant (R32) which
does not destroy the ozone layer.
• R32 refrigerant has a high working pressure and is apt to be affected
by impurities such as water, oxidizing membrane, and oils. Therefore,
during installation work, be careful that water, dust, previous
refrigerant, refrigerating machine oil, or other substances do not enter
the R32 refrigeration cycle.
• Special tools for R32 or R410A refrigerant are required for installation.
• For connecting pipes, use new and clean piping materials, and make
sure that water and/or dust does not enter.
Cautions for Outdoor Unit installation space
• In the event that the Outdoor Unit is installed in a small space and
refrigerant leaks, accumulation of highly concentrated refrigerant may
cause a fire hazard. Therefore, be sure to follow the installation space
instructions in the Installation Manual, and provide open space on at
least one of the four Outdoor Unit sides.
• In particular, when both the discharge and intake sides face walls and
obstacles are also placed on both sides of the Outdoor Unit, take steps
to provide space wide enough for a person to pass (600 mm or more)
on one side to prevent leaked refrigerant from accumulating.
To disconnect the product from main power supply
• This product must be connected to the main power supply by means of
a switch with a contact separation of at least 3 mm.
CAUTION
600 mm or more
Obstacle
Obstacle
Outdoor Unit
Building or wall
Building or wall
Do not wash Air to Water Heat Pump with pressure washers
• Electric leaks may cause electric shocks or fires.
Precautions for recovery of refrigerant when servicing or relocating
unita
• When removing refrigerant from a system, either for servicing or
decommissioning, it is recommended good practice that all refrigerants
are removed safely.
• When transferring refrigerant into cylinders, ensure that only
appropriate refrigerant recovery cylinders are employed. Ensure that
the correct number of cylinders for holding the total system charge is
available. All cylinders to be used are designated for the recovered
refrigerant and labelled for that refrigerant (i.e. special cylinders for the
recovery of refrigerant). Cylinders shall be complete with pressure-
relief valve and associated shut-off valves in good working order.
Empty recovery cylinders are evacuated and, if possible, cooled before
recovery occurs.
• The recovery equipment shall be in good working order with a set of
instructions concerning the equipment that is at hand and shall be
suitable for the recovery of all appropriate refrigerants including, when
applicable, flammable refrigerants. In addition, a set of calibrated
weighing scales shall be available and in good working order. Hoses
shall be complete with leak-free disconnect couplings and in good
condition. Before using the recovery machine, check that it is in
satisfactory working order, has been properly maintained and that any
associated electrical components are sealed to prevent ignition in the
event of a refrigerant release. Consult manufacturer if in doubt.
• The recovered refrigerant shall be returned to the refrigerant supplier in
the correct recovery cylinder, and the relevant waste transfer note
arranged. Do not mix refrigerants in recovery units and especially not
in cylinders.
• If compressors or compressor oils are to be removed, ensure that they
have been evacuated to an acceptable level to make certain that
flammable refrigerant does not remain within the lubricant. The
evacuation process shall be carried out prior to returning the
compressor to the suppliers. Only electric heating to the compressor
body shall be employed to accelerate this process. When oil is drained
from a system, it shall be carried out safely.
9-EN
10-EN
Содержание HWT-1101HRW-E
Страница 22: ...2F30251001 ...