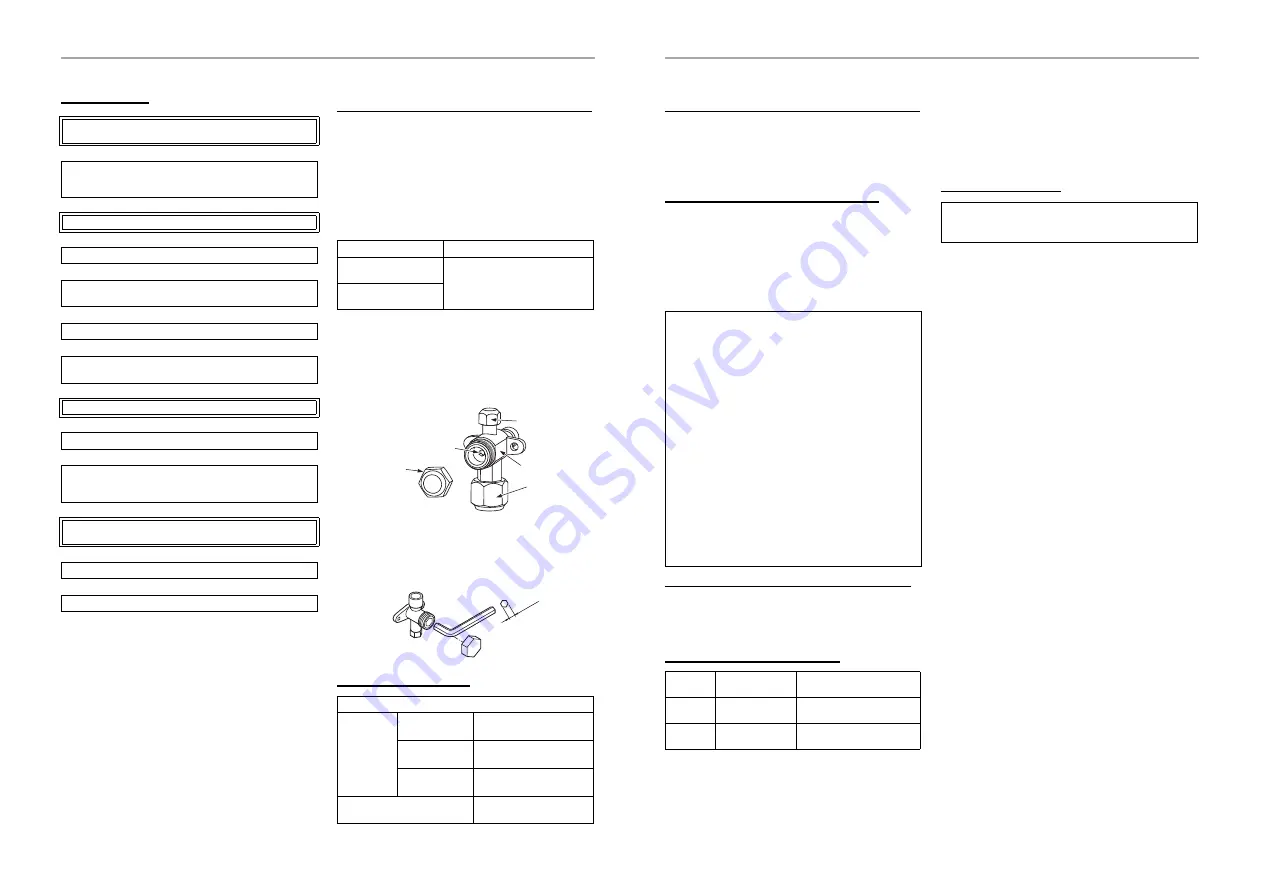
– 13 –
Outdoor Unit
Installation Manual
Vacuum pump
*1 Use the vacuum pump, vacuum pump adapter, and
gauge manifold correctly referring to the manuals
supplied with each tool before using them.
Check that the vacuum pump oil is filled up to the
specified line of the oil gauge.
*2 When air is not charged, check again whether the
connecting port of the discharge hose, which has a
projection to push the valve core, is firmly connected to
the charge port.
■
How to Open the Valve
Fully open the valves of the Outdoor Unit. (First fully
open the valve on the liquid side, and then fully open
the valve on the gas side.)
* Do not open or close the valves when the ambient
temperature is -20°C or less. Doing so may damage
the valve O-rings and result in refrigerant leakage.
Liquid side
Open the valve with hexagon wrench.
Gas side
<HWT-80, 110>
Service valve
Open the valve with hexagon wrench.
Hexagon wrench size : 5 mm
<HWT-40, 60>
Service valve
Open the valve with hexagon wrench.
Hexagon wrench size : 4 mm
Cap tightening torque
As shown in the figure, connect the charge hose after the
manifold valve is closed completely.
Attach the connecting port of the charge hose with a
projection to push the valve core (setting pin) to the charge
port of the set.
Open Handle Low fully.
Turn ON the vacuum pump. (*1)
Loosen the flare nut of the packed valve (Gas side) a little to
check that the air passes through. (*2)
Retighten the flare nut.
Execute vacuuming until the compound pressure gauge
indicates –101 kPa (–76 cmHg). (*1)
Close Handle Low completely.
Turn OFF the vacuum pump.
Leave the vacuum pump as it is for 1 or 2 minutes, and check
that the indicator of the compound pressure gauge does not
return.
Open the valve stem or valve handle fully. (First, at liquid
side, then gas side)
Disconnect the charge hose from the charge port.
Tighten the valve and caps of the charge port securely.
Model HWT-
Hexagon wrench size
40
60
4 mm
80
110
Cap tightening torque
Valve size
Ø6.4 mm
14 to 18 N•m
(1.4 to 1.8 kgf•m)
Ø12.7 mm
33 to 42 N•m
(3.3 to 4.2 kgf•m)
Ø15.9 mm
33 to 42 N•m
(3.3 to 4.2 kgf•m)
Charge port
14 to 18 N•m
(1.4 to 1.8 kgf•m)
Charge port
Valve stem
Valve unit
Flare nut
Valve stem
cap
4 m
m
■
Replenishing Refrigerant
This model is a 8 m* chargeless type that does not
need to have its refrigerant replenished for refrigerant
pipes up to 8 m
*
. When a refrigerant pipe longer than
8 m* is used, add the specified amount of refrigerant.
* HWT-40, 60: 15m
Refrigerant replenishing procedure
1. After vacuuming the refrigerant pipe, close the
valves and then charge the refrigerant while the Air
to Water Heat Pump is not working.
2. When the refrigerant cannot be charged to the
specified amount, charge the required amount of
refrigerant from the charge port of the valve on the
gas side during cooling.
Requirement for replenishing refrigerant
Replenish liquid refrigerant.
When gaseous refrigerant is replenished, the
refrigerant composition varies, which disables normal
operation.
Adding additional refrigerant
* The maximum refrigerant charge: 1.8kg
<HWT-40, 60>
The refrigerant need not be reduced for a 15 meter
(
or
less
)
refrigerant pipe.
<HWT-80, 110>
• The refrigerant need not be reduced for a 8 meter
(or less) refrigerant pipe.
Gas leak inspection
* Leak detectors for conventional HCFC
refrigerant (R22, etc.) cannot be used, as the
sensitivity drops to approximately 1/40 when
used for HFC refrigerant.
• R32 has a high working pressure, so failure to
perform the installation work properly may result in
gas leaks such as when the pressure rises during
operation. Be sure to perform leak tests on the piping
connections.
• Under no circumstances shall potential sources of
ignition be used in the searching for or detection of
refrigerant leaks. A halide torch (or any other
detector using a naked flame) shall not be used.
• Electronic leak detectors may be used to detect
refrigerant leaks but, in the case of flammable
refrigerants, the sensitivity may not be adequate, or
may need re-calibration.
• Ensure that the detector is not a potential source of
ignition and is suitable for the refrigerant used. Leak
detection equipment shall be set at a percentage of
the LFL of the refrigerant and shall be calibrated to
the refrigerant employed, and the appropriate
percentage of gas (25 % maximum) is confirmed.
• Leak detection fluids are also suitable for use with
most refrigerants but the use of detergents
containing chlorine shall be avoided as the chlorine
may react with the refrigerant and corrode the
copper pipe-work.
• If a leak is suspected, all naked flames shall be
removed/extinguished.
• If a leakage of refrigerant is found which requires
brazing, all of the refrigerant shall be recovered from
the system, or isolated (by means of shut off valves)
in a part of the system remote from the leak.
• Ensure that contamination of different refrigerants
does not occur when using charging equipment.
Hoses or lines shall be as short as possible to
minimise the amount of refrigerant contained in
them.
• Cylinders shall be kept in an appropriate position
according to the instructions.
• Ensure that the refrigerating system is earthed prior
to charging the system with refrigerant.
• Label the system when charging is complete (if not
already).
• Extreme care shall be taken not to overfill the
refrigerating system.
• Prior to recharging the system, it shall be pressure-
tested with the appropriate purging gas.
• The system shall be leak-tested on completion of
charging but prior to commissioning. A follow up
leak test shall be carried out prior to leaving the
site.
Model
HWT-
Pipe length: L
Adding additional
refrigerant
40
60
20~30 m: L
20 g × (L-20)
80
110
8~30 m: L
25 g × (L-8)
Use a leak detector manufactured specially for
HFC refrigerant (R32, R410A, R134a, etc.) to
perform the R32 gas leak inspection.
25-EN
26-EN
Содержание HWT-1101HRW-E
Страница 22: ...2F30251001 ...