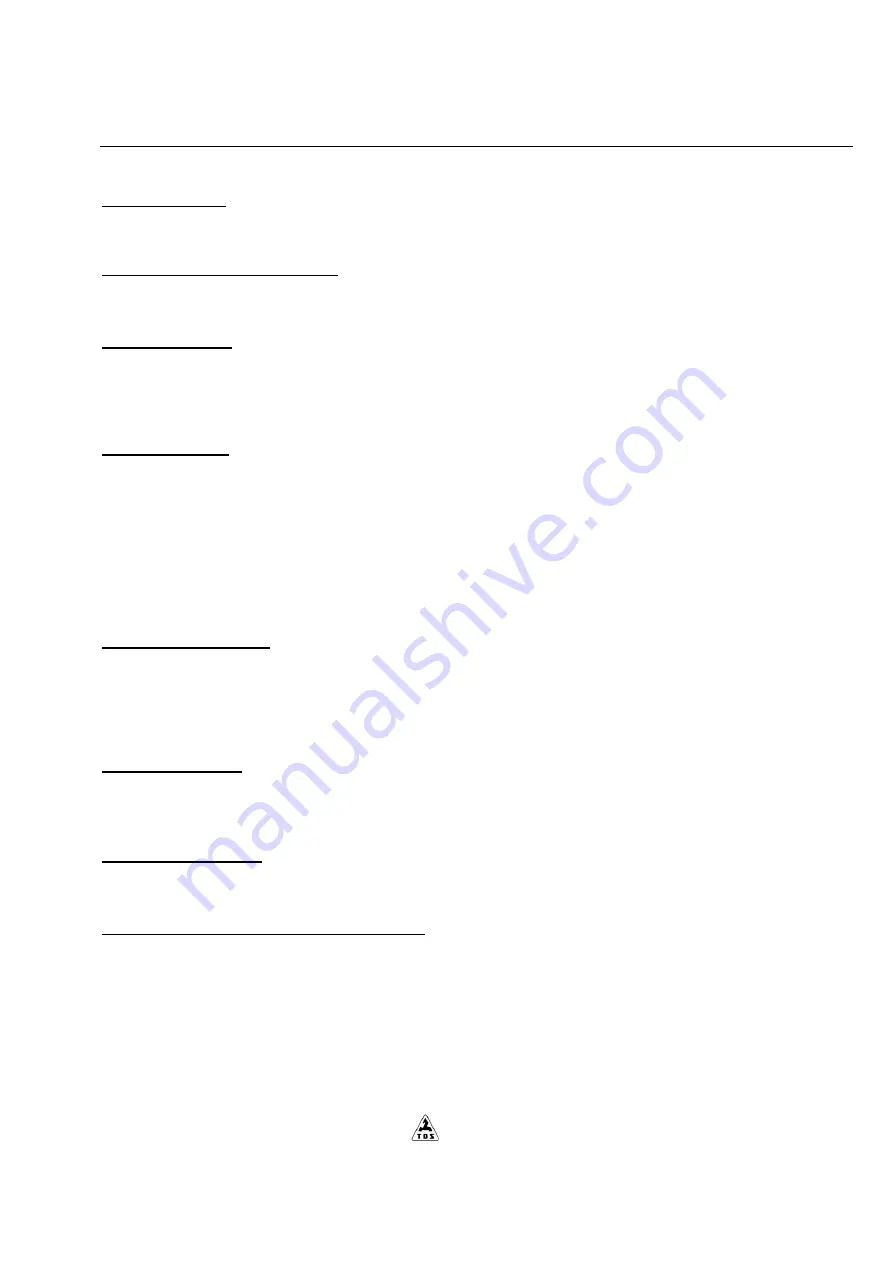
SUA 125 NUMERIC
34200003
TOS a.s. 02/2011
15
Emergency stop
Emergency stop corresponds to EN 60204, the article9.2.5.4 and EN 418, an actuator is located on the main control panel
and panel operated movement of tailstock.
Change-over switch for mode selection
The lathe is equipped with the mode switch which can be selected as “Operating mode“ as “Adjusting mode“. The selection
of modes ensures that in every time is only one active mode. The safety protection is effective in any mode.
Operating mode
If the moveble protective shield with blocking device is open in the operating mode it is only possible to open and close the
clamping device. Operating motions are possible when the moveable protective shields with blocking device are closed.
Moveable protective shields are equipped with blocking devices in accordance with EN 10888, article 3.3.3.4. and in
accordance with EN 292.2, article 4.2.2.3.
Adjusting mode
- is attainable by lockout change over switch of mode
- makes an approach to the cuting space possible when the protective shields with blocking device are closed on the
following conditions: feed rates are limited to a speed up to to 2 metres per minute and are controled by no arresting
actuator in any axis or they are limited to stepping motion with the lenght of the step not longer than 6 mm.
Note: The function “Block by block“ and progamme motion are impossible in this mode.
The following conditions are applied for the lathe:
- spindle rotation is possible only in revolutions of 50 r.p.m. or less and if the no arresting actulator is used.
Limited speed control
Control system connected with the safety for limited speed is in category 3 in accordance with EN 954-1.
For limited speed control by means of software two separated software canals have got a computer control with cross check.
For supplying the requirements of category 3 the control (excessive) loops for the acceleration check, threshold speed
check, etc. are used in above mentioned control.
Numerical control
Numerical control is self-checking, capable to comparison of input and output data which are protectived against possible
loss of programmes and electromagnetic effects and it is constant at error exposures of electric system.
Software connected with any safety should not be adjusted by user.
Power supply failure
It is secured by means of undervoltage protection device, which prevents an automatic repeated starting ( see EN 60204-1,
the article 7.5.).
Protection against mechanical risk factors
See description EN 292-1, the article 4.2 and principles EN 292-2, the article 4.
Содержание SUA 125 NUMERIC
Страница 27: ...SUA 125 NUMERIC 34200003 TOS a s 02 2011 27 Protection IP code IP 54 Interference elimination level 3...
Страница 39: ...SUA 125 NUMERIC 34200003 TOS a s 02 2011 39...
Страница 41: ...SUA 125 NUMERIC 34200003 TOS a s 02 2011 41...
Страница 43: ...SUA 125 NUMERIC 34200003 TOS a s 02 2011 43 5 2 3 Brake Fig 5 2 Fig 5 2 6...
Страница 46: ...SUA 125 NUMERIC 34200003 TOS a s 02 2011 46...
Страница 48: ...SUA 125 NUMERIC 34200003 TOS a s 02 2011 48 5 2 6 Work spindle Fig 5 4...
Страница 57: ...SUA 125 NUMERIC 34200003 TOS a s 02 2011 57...
Страница 63: ...SUA 125 NUMERIC 34200003 TOS a s 02 2011 63 Hydraulic chart...
Страница 64: ...SUA 125 NUMERIC 34200003 TOS a s 02 2011 64...
Страница 68: ...SUA 125 NUMERIC 34200003 TOS a s 02 2011 68 Fig 5 8...
Страница 70: ...SUA 125 NUMERIC 34200003 TOS a s 02 2011 70...
Страница 75: ...SUA 125 NUMERIC 34200003 TOS a s 02 2011 75...
Страница 93: ...SUA 125 NUMERIC 34200003 TOS a s 02 2011 93 Fig A transport locking...
Страница 95: ...SUA 125 NUMERIC 34200003 TOS a s 02 2011 95...
Страница 109: ...SUA 125 NUMERIC 34200003 TOS a s 02 2011 109 Fig B Working path length is 650 mm...
Страница 110: ...SUA 125 NUMERIC 34200003 TOS a s 02 2011 110 Longitudinal stops Fig C...