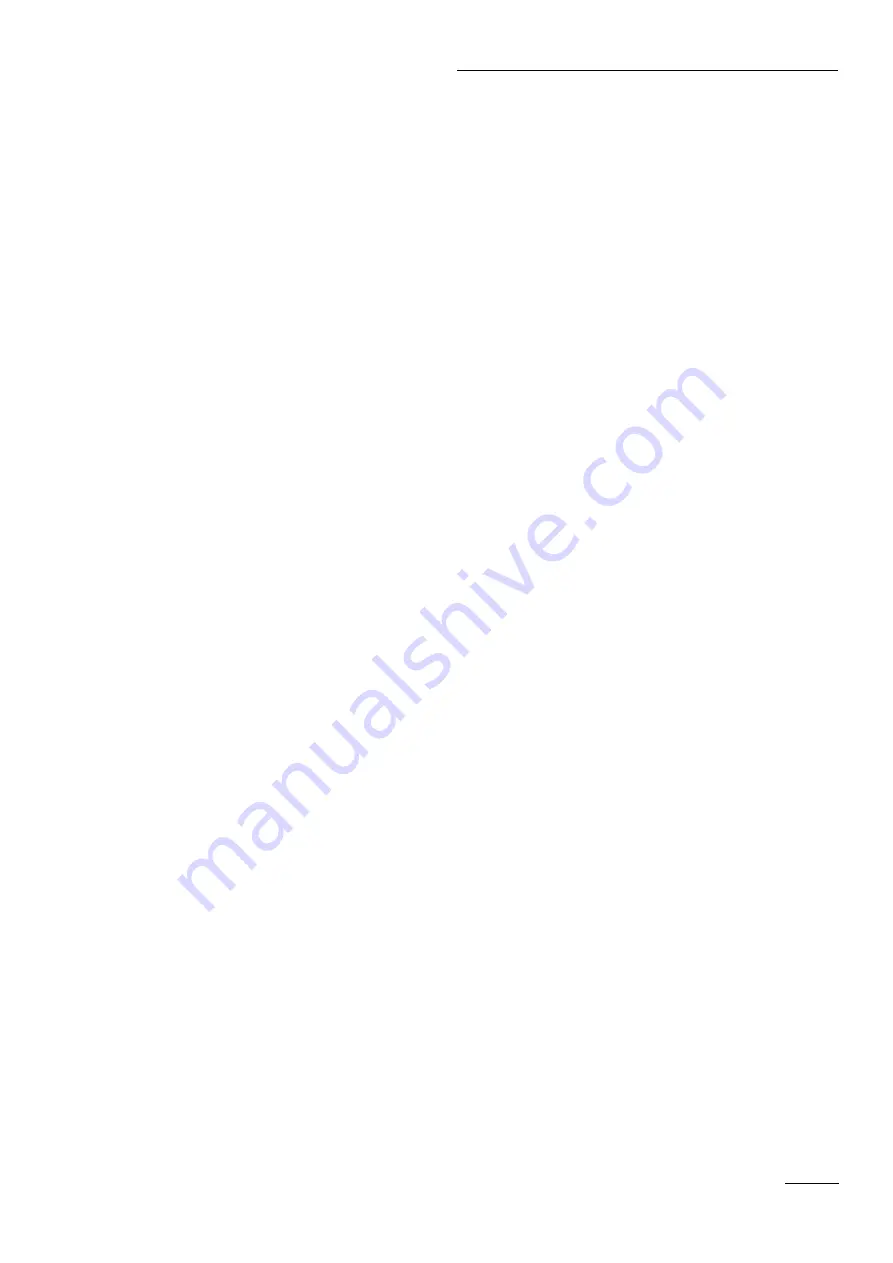
sharpness and correct reel-to-bedknife adjustment.
CUTTING UNIT
CHARACTERISTICS
The single-knob bedknife adjustment system simplifies
the procedure for delivering optimum mowing
performance. The precise adjustment possible gives the
control to provide a continual self-sharpening action—
thus maintaining sharp cutting edges, good quality of
cut, and greatly reduced need for routine backlapping.
Also, the rear roller positioning system permits optimum
bedknife attitude and location for varying heights of cut
and turf conditions.
DAILY CUTTING UNIT
ADJUSTMENTS
Before each day’s mowing, or as needed, check each
cutting unit to verify correct bedknife-to-reel contact. Do
this even though quality of cut is acceptable.
1.
Shut off the engine and lower the cutting units onto
a hard surface.
2.
Slowly turn the reel in the reverse direction,
listening for reel-to-bedknife contact. If no contact
is evident, turn the bedknife adjusting knob
clockwise, one click at a time, until you feel or hear
light contact.
3.
If you feel excessive contact, turn the bedknife
adjusting knob counterclockwise, one click at a
time, until no contact is evident. Then turn the knob
one click at a time clockwise, until light contact is
felt and heard.
IMPORTANT
: Light contact is preferred at all
times, otherwise bedknife and reel edges will not
self-sharpen. If excessive contact is maintained,
bedknife and reel wear will accelerate. Uneven
wear can result, adversely affecting quality of
cut.
Note:
As the reel blades run against the bedknife, a
slight burr will appear on the front cutting edge
surface over the full length of the bedknife.
Occasionally running a file across the front edge to
remove this burr will improve cutting.
After extended running, a ridge will eventually develop
at both ends of the bedknife. These must be rounded off
or filed flush with the cutting edge of bedknife to assure
smooth operation.
19
Operation
Содержание 02000 GROUNDS PRO 2000
Страница 5: ...Safety Instructions 5 ...
Страница 13: ...Before Operating 13 Figure 5 1 Bedknife adjusting knob ...
Страница 22: ...Figure 21 Figure 22 Figure 23 Figure 24 Figure 25 Figure 26 Maintenance 22 ...
Страница 35: ......
Страница 36: ......