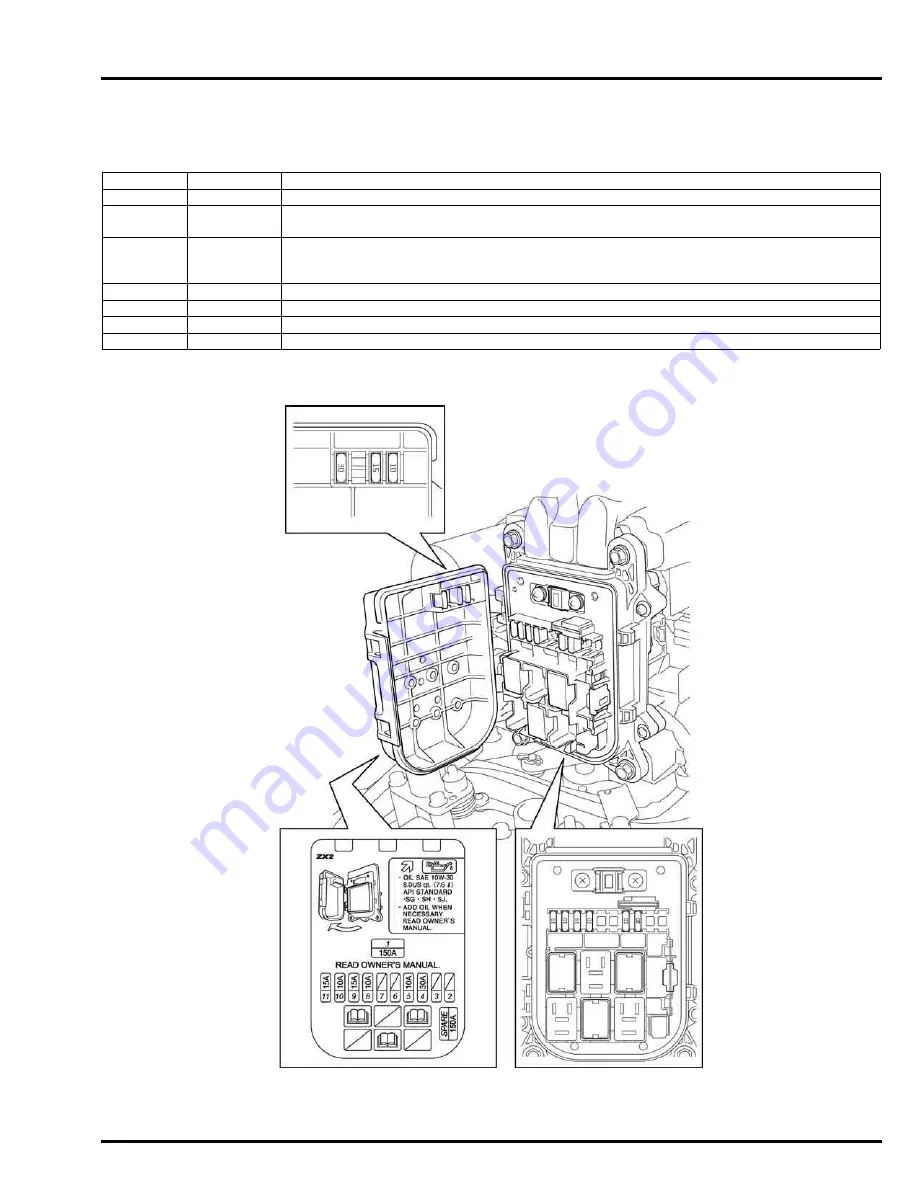
4-15
dummyhead
dummyhead
TROUBLESHOOTING
FUSE/ELECTRIC POWER LINE
TROUBLESHOOTING
FUSE CONNECTION TABLE
Fuse No.
Amps.
Component(s) or Circuit(s) Protected
1
150 A
Alternator (Output terminal)
4
30 A
ECM (Power supply), Fuel injector, Alternator, DLC, O
2
sensor heater, IAB control solenoid valve,
Direct ignition coil, Relay (Included in the junction box: Main relay, Starter relay, Fuel pump relay)
5
10 A
Alternator (Input terminal), Combination switch, Power tilt relay, Warning buzzer, Oil indicator
light, Overheat indicator light, MIL, Alternator indicator light, tachometer, Trim meter, Hour meter,
Volt meter, Relay (Included in the junction box: Main relay, Starter relay)
8
10 A
Fuel pump (High pressure side)
9
15 A
ECM (Power supply), Fuel injector
10
10 A
Alternator, O
2
sensor heater, IAB control solenoid valve, DLC
11
15 A
Direct ignition coil
Содержание BFT 250A
Страница 11: ...1 1 1 dummytext 1 GENERAL INFORMATION SERIAL NUMBER LOCATION 1 2 SPECIFICATIONS 1 2 DIMENSIONAL DRAWING 1 4...
Страница 92: ...MEMO dummyhead dummyhead...
Страница 122: ...MEMO dummyhead dummyhead...
Страница 250: ...MEMO dummyhead dummyhead...
Страница 252: ...6 2 dummyhead dummyhead ENGINE COVER COVER LOCK ENGINE COVER COVER LOCK COMPONENT LOCATION 10 N m 1 0 kgf m 7 lbf ft...
Страница 308: ...10 2 dummyhead dummyhead OTHER ELECTRICAL OTHER ELECTRICAL SYSTEM LOCATION POWER TILT RELAY FUSE RELAY JUNCTION BOX...
Страница 322: ...MEMO dummyhead dummyhead...
Страница 324: ...11 2 dummyhead dummyhead COOLING SYSTEM COOLING SYSTEM COMPONENT LOCATION 20 N m 2 0 kgf m 15 lbf ft...
Страница 325: ...11 3 dummyhead dummyhead COOLING SYSTEM TOOLS LIST Attachment 42 x 47 mm 07746 0010300 Driver 07749 0010000...
Страница 342: ...MEMO dummyhead dummyhead...
Страница 344: ...12 2 dummyhead dummyhead LUBRICATION SYSTEM LUBRICATION SYSTEM COMPONENT LOCATION 10 N m 1 0 kgf m 7 lbf ft...
Страница 359: ...13 3 dummyhead dummyhead ENGINE REMOVAL INSTALLATION TOOL LIST Engine hanger VSB02C000021...
Страница 371: ...14 3 dummyhead dummyhead CYLINDER HEAD 39 2 N m 4 0 kgf m 29 lbf ft 50 53...
Страница 373: ...14 5 dummyhead dummyhead CYLINDER HEAD Air supply attachment 07VAJ P8A010A...
Страница 414: ...MEMO dummyhead dummyhead...
Страница 454: ...MEMO dummyhead dummyhead...
Страница 552: ...MEMO dummyhead dummyhead...
Страница 554: ...18 2 dummyhead dummyhead MOUNT MOUNT COMPONENT LOCATION 83 N m 8 5 kgf m 61 lbf ft...
Страница 564: ...19 2 dummyhead dummyhead TRIM TILT TRIM TILT COMPONENT LOCATION 34 N m 3 5 kgf m 25 lbf ft 34 N m 3 5 kgf m 25 lbf ft...
Страница 606: ...MEMO dummyhead dummyhead...
Страница 608: ...20 2 dummyhead dummyhead CONTROLS CONTROLS COMPONENT LOCATION...
Страница 621: ...21 1 21 dummytext 21 TECHNICAL FEATURES SHIFT EFFORT REDUCTION SYSTEM 21 2 CHARGE OUTPUT ENHANCEMENT WHEN IDLING 21 4...
Страница 628: ...22 4 dummyhead dummyhead WIRING DIAGRAMS...