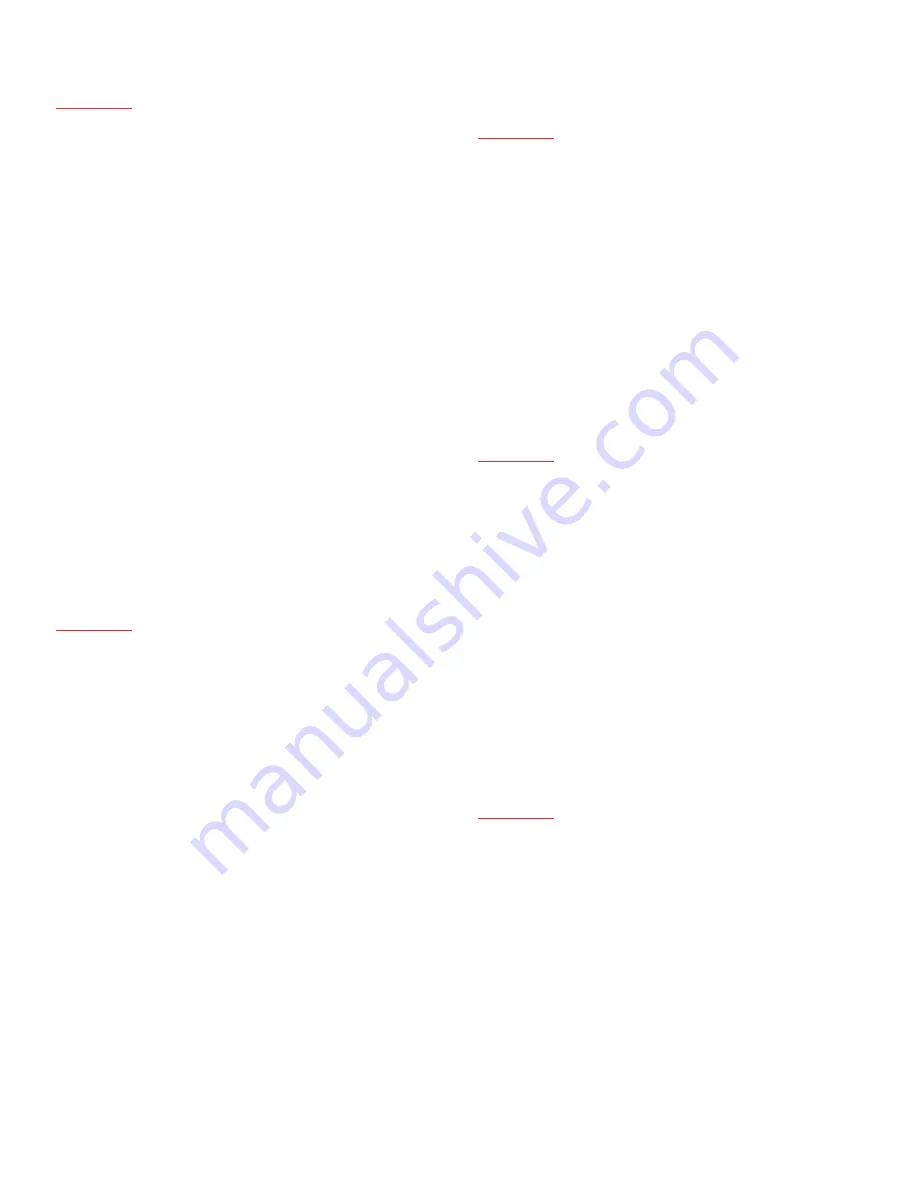
Gear Replacement
WARNING:
Before proceeding, follow the Pressure
Relief Procedure outlined on Page 5. Additionally,
follow all other warnings to reduce the risk of an
injection injury, injury from moving parts or electric
shock. Always unplug the sprayer before servicing!
1. Remove safety plate (#43).
2. Remove screws (#21) with a 3/16" allen wrench.
3. Slide pump section from crank slide (#300) pg. 24. If
pump section will not slide off, use a screwdriver to pry
pump section down, then slide off.
4. Remove cover (#44).
5. Remove (4) screws #21 with a 3/16" allen wrench.
6. Slide pump housing main assembly (#40) off motor box
housing #31.
7. Inspect gears beginning with crankshaft
assembly(#37). Then, output pinion gear (#33), followed
by pinion gear (#38).
8. Inspect pinion gear on motor armature assembly
(#139) pg. 18 by removing motor as described in motor
replacement section.
9. Reassemble by reversing the above order. When
reassembling, make sure that all washers are in place
and that gears and bearing are properly lubricated.
10. Grease Item #37 every 100 hours. Fitting located
under Plate #44.
11. Grease Item #300 on page 24 every 100 hours.
Fitting located on Item #300 under Plate #44.
On/Off Switch Replacement
WARNING:
Before proceeding, follow the Pressure
Relief Procedure outlined on Page 5. Additionally,
follow all other warnings to reduce the risk of an
injection injury, injury from moving parts or electric
shock. Always unplug the sprayer before servicing!
1. Remove Switch Cover Plate and screws (#56 & #55).
2. Disconnect the two black wires from the On/Off Switch
(#49).
3. Remove the rubber boot and plate (#47 & #48) with a
wrench.
4. Remove the On/Off Switch (#49).
5. Install a new Switch and reattach plate and rubber
boot. Tighten securely.
6. Reconnect the two black wires to the new On/Off
Switch.
7. Reinstall Switch Cover Plate and screws, with warning
label facing out.
Power Supply Cord
Replacement
WARNING:
Before proceeding, follow the Pressure
Relief Procedure outlined on Page 5. Additionally,
follow all other warnings to reduce the risk of an
injection injury, injury from moving parts or electric
shock. Always unplug the sprayer before servicing!
1. Remove Switch Cover Plate and screws (#55 & #56).
2. Disconnect the Power Supply Cord (#46) from; a) the
On/Off Switch (#49), b) the white wire connected to the
motor and, c) the green wire connected to the grounding
screw (#42). Refer to the Electrical Schematic, Figure 7.
3. Loosen the cord grip housing (#45) and remove the
power cord (#46).
4. Install the new cord in reverse order of disassembly.
5. Install the cover and screws with warning label facing
out.
Replacement of Motor Starter
WARNING:
Before proceeding, follow the Pressure
Relief Procedure outlined on Page 5. Additionally,
follow all other warnings to reduce the risk of an
injection injury, injury from moving parts or electric
shock. Always unplug the sprayer before servicing!
1. Remove Switch Cover Plate and screws (#55 & #56).
2. Disconnect wires, a) both white/red wires from the
pressure switch, b) the black wire from the motor and, c)
the black wire from the On/Off Switch.
3. Remove screws (#58) and washer and nuts (#52 #53).
4. Replace Motor Starter and resecure with screws,
washer and nuts (#58, #53 and #52). Always use heat
sink material on the back of the Motor Starter when
installing.
5. Reconnect wires according to Figure 7.
6. Reinstall switch cover and screws, with warning label
facing out.
Motor Brush Replacement
WARNING:
Before proceeding, follow the Pressure
Relief Procedure outlined on Page 5. Additionally,
follow all other warnings to reduce the risk of an
injection injury, injury from moving parts or electric
shock. Always unplug the sprayer before servicing!
1. Remove Brush Plate (#22).
2. Remover Brush Insulator (#23).
3. Remove Brush Spring (#25).
NOTE:
To remove brush
spring, push spring down and in for it to release.
4. Back-off screw. Hold Brush Wire and remove Brush.
5. Inspect Motor Brush. If damaged replace.
6. Repeat procedure for other brush.
7. To install Motor Brushes, reverse steps 1 through 6,
NOTE:
Never operate this unit without Brush Insulator
and Brush Plate installed.
21