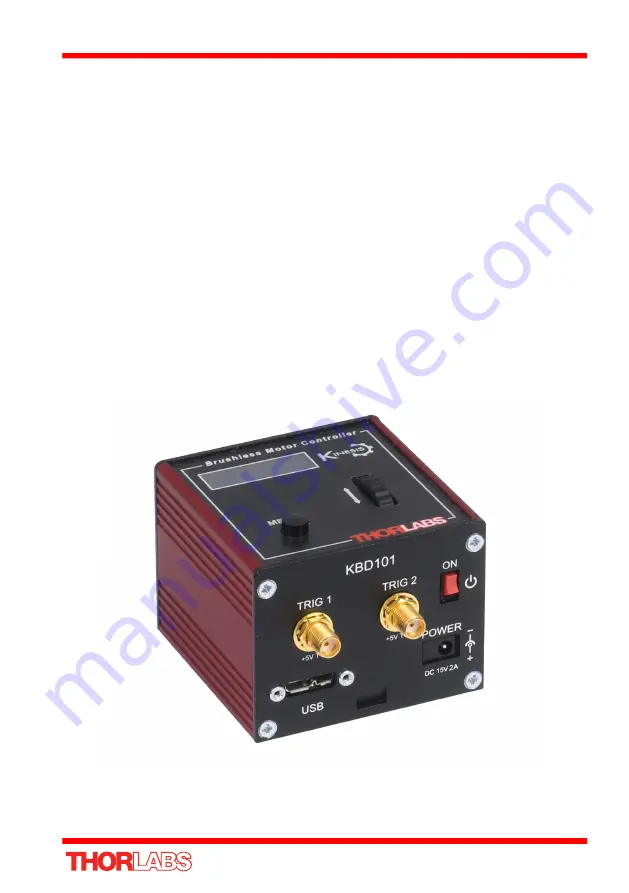
5
Chapter 2 Overview and Setup
2.1 Introduction
The KBD101 Brushless DC Motor K-Cubes are ideal for motion control applications
demanding high speed (100s of mm/s) and high encoder resolution (<100 nm)
operation. These single channel drivers offer high-precision motion control in a wide
range of applications, and in particular when used along with our DDSM100 fast
translation stage where speeds of up to 500 mm/sec can be achieved. Designed
using latest digital and analog techniques and with high-bandwidth high-power servo
control circuitry, these new drivers are capable of driving a range of rotary and linear
brushless 3-phase DC motors of up to 2 Amp peak coil current.
Integrated into the apt family of products, it offers Thorlabs standard control and
programming interface, allowing easy integration into the customer’s own automated
motion control applications. These units are cable of being reprogrammed in-field,
allowing the option of upgrading the units with future firmware releases as soon as
new programming interfaces (such as microscopy standard command sets) are
added.
Fig. 2.1 K-Cube Brushless DC Servo Motor driver (KBD101)