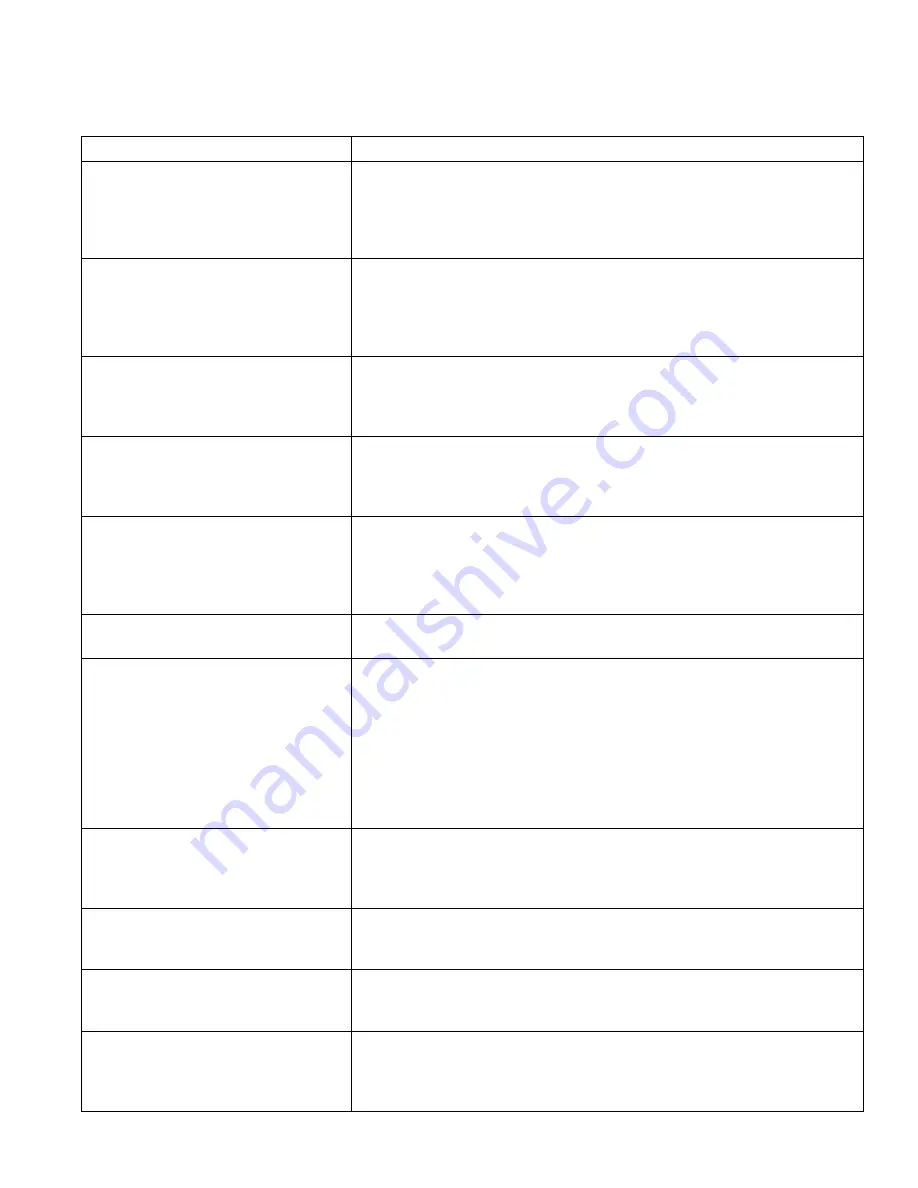
29
Low Temperature Reading/Alarm
The following summarizes some of the possible causes and solutions for heat tracing low temperature readings/alarms.
Possible Cause
Recommended Solutions
Temperature of product in process
line is below the alarm set point or
expected reading due to events other
than heat tracing—low pumping
temperatures, etc.
Let process operations return to normal conditions and then recheck for
alarms. Alternately adjust alarm set point (with project engineers approval)
to allow for this process condition.
Low temperature alarm programmed
setting or expected reading did
not consider natural temperature
undershoot associated with control
scheme.
Move control set point up to allow for natural undershoot or lower the low
temperature alarm set point (when approved by project engineer).
Damaged, open, or wet thermal
insulation does not allow the
heat provided to hold the desired
temperature.
Repair damage to insulation.
Wrong insulation size, type, or
thickness on all of circuit being traced.
Measure circumference of insulation, divide by π, and compare to
insulation diameter charts for proper over sizing. Check insulation type and
thickness against design specification. Replace insulation or review system
design for alternate operating possibilities which involve more heat output.
Wrong insulation size, type, or
thickness on part of circuit being
traced.
The insulation system should be as specified in the design for the entire
circuit being traced. Having a high heat loss on one part of the circuit and
a lower heat loss insulation on the other part of the circuit (perhaps where
the sensor is) will result in the poorly insulated line being too cold. Redo
the insulation to assure uniformity and consistency.
Improperly located RTD temperature
sensor.
Is RTD sensor next to pipe support, equipment, or other heat sink? Move
RTD sensor to location more representative of the majority of the piping.
Improperly installed RTD temperature
sensor or RTD temperature probe.
Permanent RTD temperature sensors are most accurate when installed
along the pipe or equipment with at least a foot of probe and sensor wire
running along the pipe before exiting through the insulation. Permanent
RTD sensors which enter the insulation at 90 degrees may be more
sensitive to error associated with them, depending on insulation installation
or how well the sensor is physically attached. Adjust control set point to
compensate for any accuracy offset. When using a 90 degree RTD probe
for diagnostics, verify this measurement technique on a known pipe in the
same general temperature range and insulation configuration.
Damaged RTD sensor.
Disconnect RTD sensor and measure resistance. Compare to resistance
tables for corresponding value of temperature. Compare to pipe or
equipment temperature known by another probe or sensor. If different, the
RTD sensor may need replacement.
Heat tracing undersized, improperly
installed or damaged.
Review design/installation. Check heat tracing for presence of proper
current and also meg for dielectric resistance. Repair or replace heat
tracing.
Heat tracing circuits are wired such
that the RTD for circuit A is controlling
circuit B, etc.
Trace and recheck field and panel wiring. Use circuit “turn -on “ and
“turn-off” technique or disconnect RTD’s one at a time to see if the proper
RTD failure alarm occurs on the right circuit.
Heat tracing does not heat. Breaker
has been switched off due to
maintenance activities or has possibly
malfunctioned.
As soon as maintenance activities cease and after conferring with
operations manager, switch breaker back ON. Note that some period
of time will elapse before the temperature alarm goes away (pipes and
equipment take time to heat up).