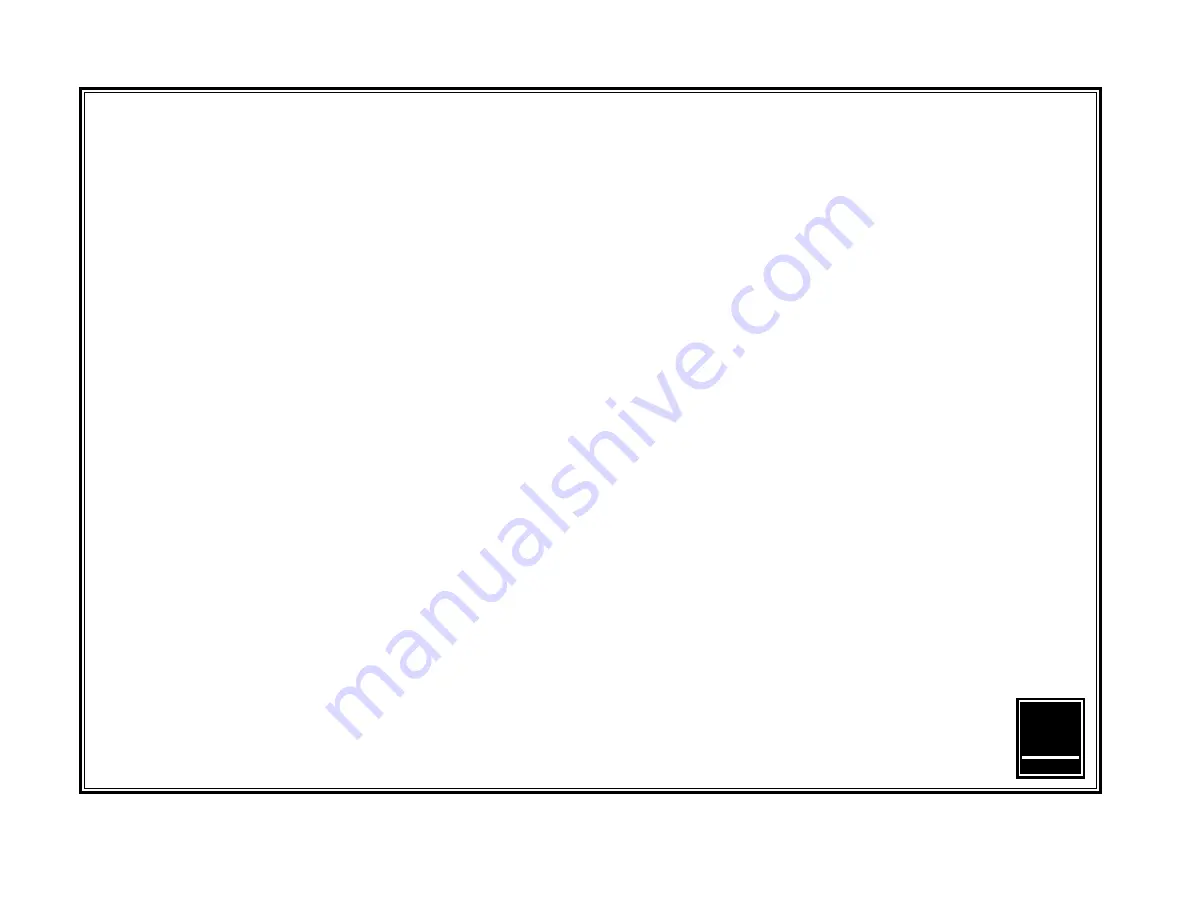
THERMO ELECTRON CORPORATION STANDARD PRODUCT WARRANTY
The Warranty Period starts two weeks from the date your equipment is shipped from our facility. This allows for shipping time
so the warranty will go into effect at approximately the same time your equipment is delivered. The warranty protection
extends to any subsequent owner during the first year warranty period.
During the first year, component parts proven to be non-conforming in materials or workmanship will be repaired or replaced
at Thermo's expense, labor included. Installation and calibration are not covered by this warranty agreement. The Technical
Services Department must be contacted for warranty determination and direction prior to performance of any repairs.
Expendable items, glass, filters and gaskets are excluded from this warranty.
Replacement or repair of components parts or equipment under this warranty shall not extend the warranty to either the
equipment or to the component part beyond the original warranty period. The Technical Services Department must give prior
approval for return of any components or equipment. At Thermo's option, all non-conforming parts must be returned to
Thermo Electron Corporation postage paid and replacement parts are shipped FOB destination.
THIS WARRANTY IS EXCLUSIVE AND IN LIEU OF ALL OTHER WARRANTIES, WHETHER WRITTEN, ORAL OR
IMPLIED. NO WARRANTIES OF MERCHANTABILITY OR FITNESS FOR A PARTICULAR PURPOSE SHALL APPLY.
Thermo shall not be liable for any indirect or consequential damages including, without limitation, damages relating to lost
profits or loss of products.
Your local Thermo Sales Office is ready to help with comprehensive site preparation information before your equipment
arrives. Printed instruction manuals carefully detail equipment installation, operation and preventive maintenance.
If equipment service is required, please call your Technical Services Office at 1-888-213-1790 (USA and Canada) or 1-740-
373-4763. We're ready to answer your questions on equipment warranty, operation, maintenance, service and special appli-
cation. Outside the USA, contact your local distributor for warranty information.
Rev. 2 1/03
ISO
9001
REGISTERED
Содержание 3010 Series
Страница 4: ...Model 3010 Incubator ___________________________________________________________________________ iii ...
Страница 29: ...7 2 Model 3010 Incubator ________________________________________________________________Spare Parts ...
Страница 30: ...7 3 Model 3010 Incubator ________________________________________________________________Spare Parts ...
Страница 31: ...7 4 Model 3010 Incubator ________________________________________________________________Spare Parts ...
Страница 32: ...7 5 Model 3010 Incubator ________________________________________________________________Spare Parts ...
Страница 33: ...Model 3010 Incubator __________________________________________________________Electrical Schematics 8 1 ...
Страница 34: ...Model 3010 Incubator __________________________________________________________Electrical Schematics 8 2 ...