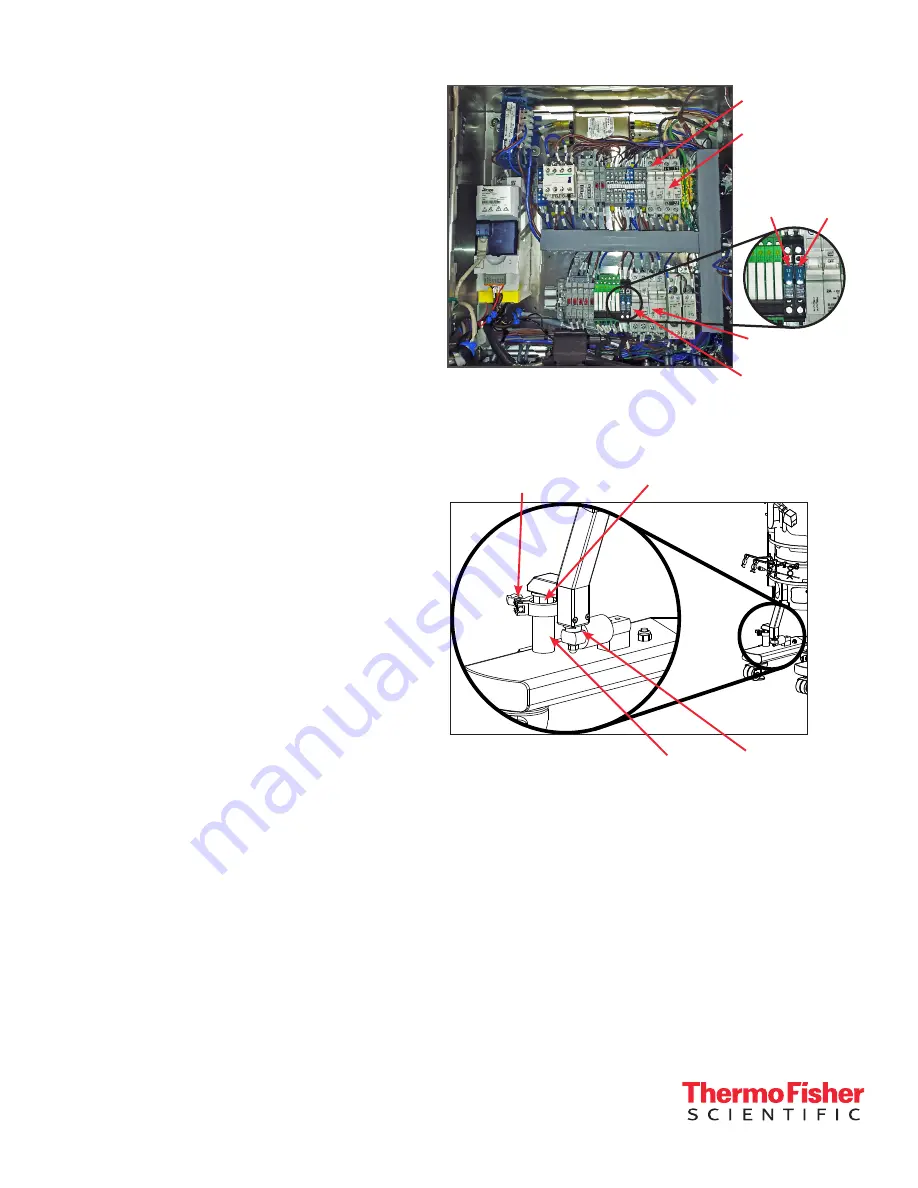
3
2. Close the E-Box and lock the panel using a
flat-head screwdriver before continuing.
3. Connect all electrical plugs to facility power. Refer
to hardware/electrical labels and schematics to
ensure proper electrical voltage is connected to
the DynaDrive S.U.B.
Note:
The yellow plug and
receptacle are for 120 VAC, and the blue plug and
receptacle are for 240 VAC S.U.B.s.
Unlocking load cells
Figure 3 illustrates the location and components of load
cells on on a standard HyPerforma S.U.B. The location
and process is the same for DynaDrive S.U.B.s.
All load cells must be fully locked down in order to
move the DynaDrive S.U.B. For DynaDrive S.U.B.
hardware units purchased with factory-installed load
cells, the load cells are shipped in the locked position
(threaded up) for equipment protection.
1. To unlock the load cells (after the system is in its
final location), remove and discard the delrin slip
ring if it is present. Remove the tri-clamp.
2. Loosen the lockout nut, using an adjustable or
1.25 in. wrench (not supplied), until the nut is tight
against the base or leg of the S.U.B. Repeat this
process for each load cell until all of the lockout
nuts are disengaged from the lockout posts. Do
not reinstall the tri-clamp.
3. At this point, the DynaDrive S.U.B. hardware is
ready to be prepared for BPC loading.
Leveling and connecting the system
All manual movements of the DynaDrive S.U.B.
hardware should be over smooth surfaces, with the
S.U.B. empty and disconnected from all power and
gas/feed sources. All load cells must be fully locked
down in order to move a S.U.B.
1. Verify that the facility electrical supplies are
sufficient to support the power requirements of the
DynaDrive S.U.B. and ancillary components, such
as controllers or pumps.
VFD breaker
Continuous power
breaker
Temp.
display
breaker
Main power
breaker
E-Stop power
breaker
Pressure
sensor
breaker
Figure 2. DynaDrive S.U.B. E-Box interior.
A
Figure 3. Load cell schematic.
Lockout nut
Delrin slip
ring
Lockout
post
38.1 mm (1.5 in.)
Tri-clamp